Why Choose Liquid Filled Gauges Over Dry Ones?
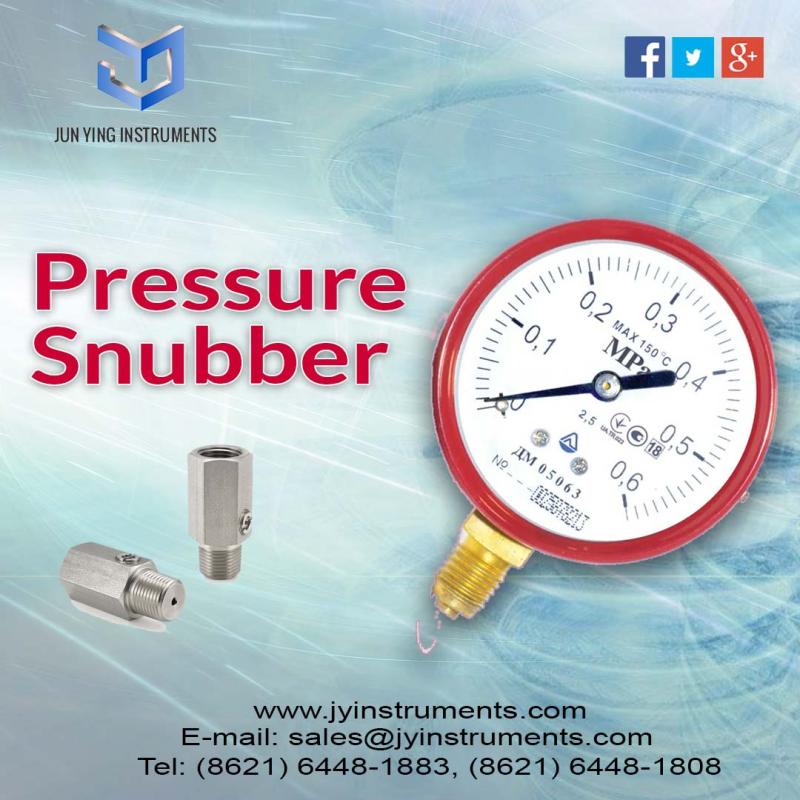
Pressure gauges are vital instruments used in various industries to measure and monitor pressure levels in systems. Choosing the right type of gauge is crucial for ensuring accuracy, durability, and reliability. Among the options available, liquid-filled gauges offer distinct advantages over dry gauges, making them the preferred choice in many applications. This article explores the benefits of liquid-filled gauges and why they often outperform their dry counterparts.
Understanding Liquid-Filled Gauges
Liquid-filled gauges are Low Pressure Gauge filled with a dampening fluid, typically glycerin or silicone. The fluid inside the gauge casing serves as a buffer against external vibrations and internal oscillations, providing stability to the gauge mechanism. This design feature distinguishes liquid-filled gauges from traditional dry gauges, which do not have such fluid dampening.
Advantages of Liquid-Filled Gauges
1. Enhanced Durability
One of the standout features of liquid-filled gauges is their ability to withstand harsh environments. The fluid inside the gauge absorbs shocks and vibrations that could otherwise damage the internal components of a dry gauge. This makes liquid-filled gauges particularly suitable for applications in high-vibration settings, such as industrial machinery, construction equipment, and marine environments.
Additionally, the fluid acts as a lubricant for the gauge's internal components, reducing wear and tear. This prolongs the life of the instrument, ensuring reliable performance over an extended period.
2. Improved Accuracy
Accuracy is a critical factor in pressure measurement. Vibrations and rapid pressure fluctuations can cause the needle of a dry gauge to oscillate, leading to difficulty in obtaining a precise reading. In contrast, the liquid inside a filled gauge dampens these oscillations, stabilizing the needle and providing a clear and accurate reading even in dynamic conditions.
This feature is particularly beneficial in industries where precise pressure measurements are essential, such as chemical processing, food production, and pharmaceutical manufacturing.
3. Protection Against Environmental Factors
Liquid-filled gauges are better equipped to handle extreme environmental conditions compared to dry gauges. The liquid filling creates a seal that protects the internal components from moisture, dust, and other contaminants. This makes them an excellent choice for outdoor applications or environments with high levels of particulate matter.
Furthermore, the fluid helps maintain the integrity of the gauge in extreme temperature conditions. Glycerin-filled gauges are ideal for moderate temperatures, while silicone-filled ones are preferred for applications involving extreme heat or cold.
4. Resistance to Overpressure
Overpressure, or sudden spikes in pressure, can damage the internal mechanisms of a dry gauge. Liquid-filled gauges, however, are designed to withstand such conditions more effectively. The dampening effect of the liquid reduces the impact of pressure spikes, preventing potential damage and maintaining measurement accuracy.
5. Reduced Maintenance Needs
Dry gauges often require regular maintenance to remain functional in demanding environments. Components may wear out faster due to exposure to vibrations, dirt, and extreme temperatures. Liquid-filled gauges, on the other hand, require less frequent maintenance because the fluid acts as both a protective barrier and a lubricant for the moving parts.
This reduction in maintenance needs translates to cost savings and increased efficiency in operations, especially in industries where downtime is costly.
Applications of Liquid-Filled Gauges
Due to their superior performance and durability, liquid-filled gauges find applications in a wide range of industries, including:
- Oil and Gas: Monitoring pressure in pipelines and drilling equipment.
- Manufacturing: Ensuring consistent performance in machinery.
- Automotive: Measuring pressure in hydraulic and pneumatic systems.
- HVAC Systems: Monitoring pressure in heating, ventilation, and air conditioning systems.
Conclusion
When it comes to choosing between Liquid Filled Gauge and dry gauges, the decision often boils down to the operating environment and the specific needs of the application. Liquid-filled gauges offer enhanced durability, accuracy, and resistance to environmental challenges, making them the preferred choice for demanding conditions. While dry gauges may suffice in less rigorous settings, the advantages of liquid-filled gauges make them a valuable investment for industries that prioritize reliability and precision in pressure measurement.
By understanding the benefits of liquid-filled gauges, professionals can make informed decisions that contribute to the efficiency and safety of their operations.
Comments