How to Select the Perfect Liquid Filled Gauge for Accuracy
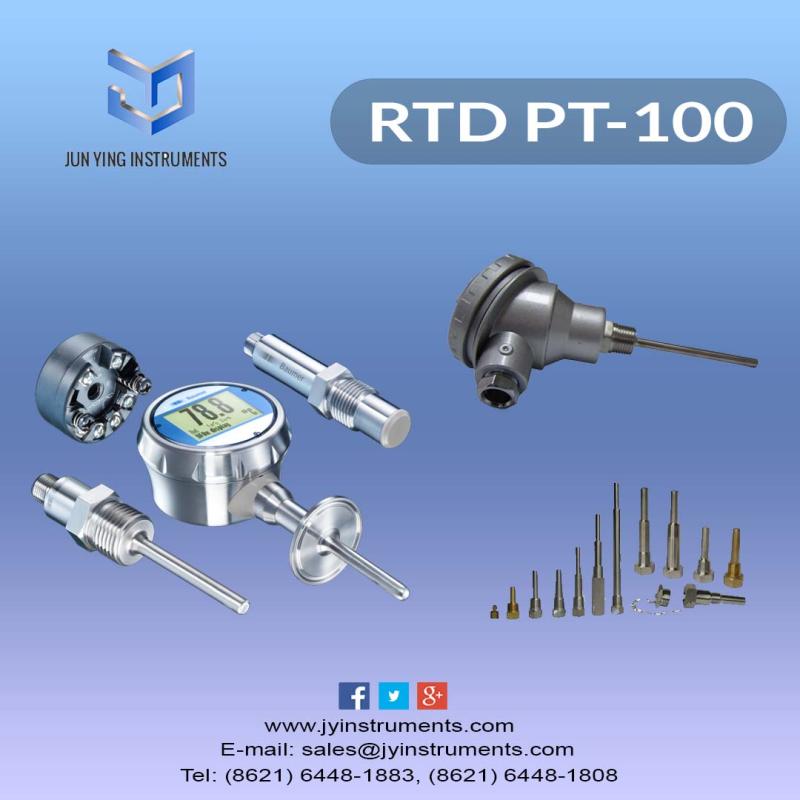
Liquid-filled gauges are widely
used in various industries for their ability to provide precise pressure
readings while withstanding harsh environments. Selecting the right
liquid-filled gauge for your application is critical to ensure accuracy,
durability, and reliability. This guide walks you through the key factors to
consider when choosing a liquid-filled gauge.
Understand the Basics of
Liquid-Filled Gauges
A liquid-filled gauge contains a
fluid, typically glycerin or silicone oil, within the casing. This liquid
dampens the movement of the internal components, reducing vibrations and
protecting against sudden pressure spikes. The result is improved accuracy and
extended lifespan compared to dry gauges.
Key Factors to Consider
Pressure Range
Determine the maximum pressure
your application will encounter. The gauge’s range should exceed this maximum
by 25-50% to prevent overstressing the instrument.
Avoid selecting a gauge with a
range too high above your operating pressure & Glass Tube Thermometer, as
it may reduce reading precision.
Operating Environment
Assess the conditions where the
gauge will operate, such as temperature, humidity, and exposure to chemicals or
corrosive substances.
For extreme temperatures,
silicone-filled gauges perform better than glycerin-filled ones due to their
wider operating range.
If the gauge will be exposed to
aggressive chemicals, select materials like stainless steel for enhanced
corrosion resistance.
Accuracy Grade
Gauges are categorized by
accuracy grades, typically expressed as a percentage of the full-scale reading.
For instance, a 1% accuracy grade indicates that the reading will be within 1%
of the maximum range.
Choose a gauge with an accuracy
grade suitable for your application. Critical applications may require a higher
accuracy grade, such as 0.25% or 0.5%, while general-purpose uses can work with
lower grades like 1% or 2%.
Dial Size
The dial size impacts
readability. Larger dials (e.g., 4-6 inches) are ideal for applications where
gauges are mounted at a distance or in low-light environments.
Smaller dials (e.g., 2-3 inches)
are more compact and suitable for tight spaces but may be harder to read.
Connection Type and Size
Ensure compatibility with your
system by selecting the appropriate connection type (e.g., NPT, BSP) and size.
Common sizes range from ¼ inch to
½ inch. Verify the thread size to ensure a secure fit.
Liquid Type
The type of liquid used in the
gauge affects its performance. Glycerin is suitable for most applications but
may freeze in very low temperatures.
Silicone is preferred for
high-temperature or low-temperature environments and for applications requiring
quicker response times.
Vibration and Pulsation
Protection
If the application involves
excessive vibration or pulsation, ensure the gauge’s liquid filling and
internal components are designed to handle these conditions.
A snubber or pulsation
dampener may further enhance durability and accuracy.
Material Compatibility
Check that the materials used in
the gauge are compatible with the media it will measure. For example, use brass
for non-corrosive media and stainless steel for corrosive substances or high-pressure
applications.
Compliance and Certification
Depending on your industry,
ensure the gauge complies with relevant standards, such as ASME, ANSI, or ISO
certifications. These certifications guarantee quality and safety.
Tips for Optimal Gauge
Performance
Calibration: Regularly calibrate
your gauge to maintain accuracy, especially in critical applications.
Mounting: Install the gauge
correctly, avoiding stress on the connection to prevent leaks or damage.
Inspection: Periodically inspect
the gauge for signs of wear, such as leaks, cracks, or cloudiness in the
liquid.
Environment Protection: Use
protective covers or enclosures if the gauge operates in harsh conditions.
Conclusion
Selecting the right Liquid Filled Gauge involves
careful consideration of your application’s specific requirements, including
pressure range, operating environment, accuracy needs, and material
compatibility. By evaluating these factors, you can ensure reliable and
accurate pressure readings, extending the gauge’s lifespan and optimizing
system performance. Taking the time to choose the perfect gauge ultimately
results in better safety, efficiency, and cost-effectiveness for your
operations.
Comments