Test Plug FAQs: Key Questions on Pressure
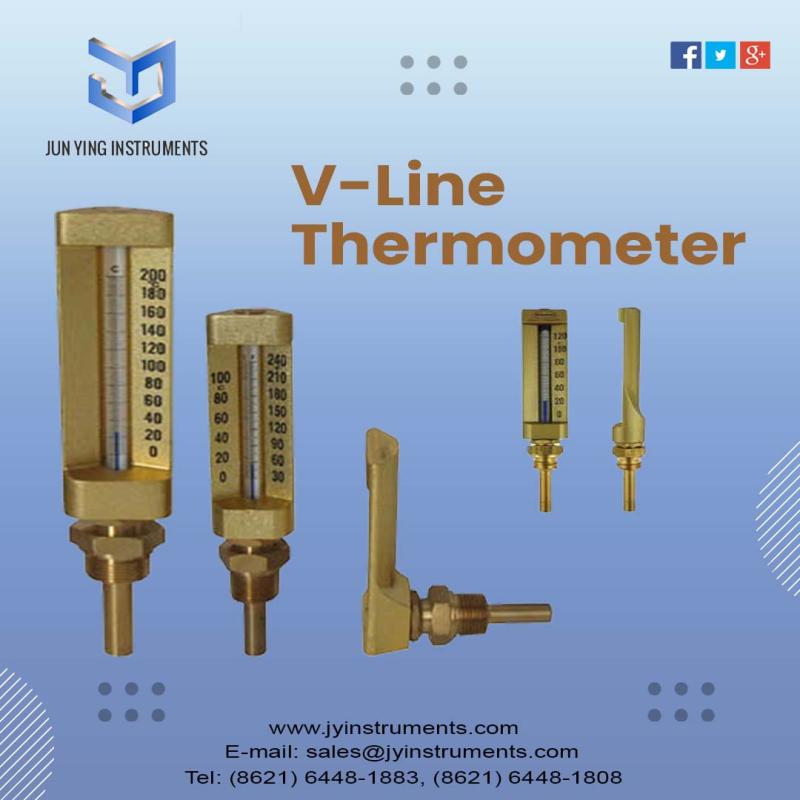
Test plugs are essential for
professionals who work with pressure and temperature gauges in various
industrial and commercial applications. They offer a quick, reliable, and safe
way to test and calibrate equipment without interrupting the flow of a system.
Here, we cover frequently asked questions about test plugs, their importance,
and how they enhance efficiency in pressure and temperature gauge operations.
1. What is a Test Plug, and
Why is it Important?
A test plug, sometimes called a
pressure test valve or test point, is a small, specialized fitting that allows
technicians to measure system pressure and temperature directly at specific
points without having to shut down the system. It is typically installed near Pressure Gauge Syphon,
pumps, or critical points in a system for easy access. Test plugs are
especially important in HVAC, water systems, gas pipelines, and other
industrial applications that require routine system checks and maintenance.
Test plugs save time and money by
eliminating the need to halt operations for regular checks. They also enhance
safety by reducing exposure to pressurized fluids and high temperatures, as
measurements can be taken quickly and efficiently through the test plug.
2. How Do Test Plugs Work?
A test plug is fitted with a
self-sealing valve that remains closed when not in use. When a technician needs
to take a reading, they insert a test probe or a pressure gauge adapter into
the test plug. This insertion opens the valve and allows the instrument to
measure the fluid or gas in the system. Once the reading is taken, the probe is
removed, and the valve reseals, preventing leaks.
The design of test plugs ensures
minimal system disruption and greatly reduces the risk of contamination or
leakage. By using test plugs, technicians can take multiple readings from
different locations in the system, leading to more accurate diagnostics and
timely adjustments.
3. What Are the Key Benefits
of Using Test Plugs?
There are several advantages to
using test plugs, including:
Non-intrusive testing: Test plugs
eliminate the need to stop a system or dismantle parts for routine gauge
checks.
Increased safety: The risk of
exposure to pressurized fluids, gases, or extreme temperatures is minimized, as
the readings can be taken without breaking the seal.
Improved accuracy: Technicians
can take readings from multiple points in the system, providing a more
comprehensive analysis.
Cost savings: Reducing system
downtime and maintenance costs helps save money and improve efficiency.
4. What Types of Test Plugs Are
Available?
There are various types of test
plugs designed for specific applications:
Pressure Test Plugs: Used
primarily to measure system pressure. They’re available in different pressure
ratings, usually measured in PSI or bar.
Temperature Test Plugs: Used to
monitor temperature changes within a system, often in conjunction with
temperature probes.
Combo Test Plugs: These plugs
allow for simultaneous pressure and temperature testing, which can be useful in
systems that require frequent monitoring of both metrics.
High-Temperature Test Plugs:
Designed for systems that handle high-temperature fluids or gases, typically
made from materials like stainless steel or brass to withstand extreme
conditions.
5. How Are Test Plugs
Installed?
Test plugs are typically
installed in-line, close to the equipment that needs regular monitoring. They
are usually threaded or welded into place, depending on the design and
materials of the system. In many cases, the installation is straightforward and
can be done during system setup or during routine maintenance.
Careful installation is important
to ensure a leak-free seal and to position the test plug in a location that
allows easy access for routine checks. Installation of Thermowell should also
comply with any relevant safety and industry standards to ensure reliable
operation over time.
6. How Often Should Test Plugs
Be Used?
The frequency of using test plugs
depends on the system’s operating conditions, regulatory requirements, and the
equipment's maintenance schedule. In critical systems where safety and
precision are paramount, regular checks may be necessary, ranging from daily to
weekly intervals. For less critical systems, monthly or quarterly readings may
be sufficient.
Routine use of test plugs helps
in early detection of potential issues such as pressure drops or temperature
changes, which could indicate leaks, blockages, or equipment malfunctions. By
catching these early, operators can prevent costly repairs or system downtime.
7. What Are the Safety
Precautions for Using Test Plugs?
Though test plugs are designed for
safety and convenience, following certain precautions is essential:
Use the correct test equipment:
Ensure that the test probe or gauge adapter matches the test plug’s
specifications to avoid damaging the valve.
Wear protective equipment: In
high-pressure or high-temperature systems, personal protective equipment (PPE)
such as gloves and eye protection is recommended.
Avoid overuse of plugs: Excessive
or forceful insertion and removal can wear down the seal over time, which can
lead to leaks.
Check for leaks regularly:
Routine checks ensure that the test plug’s self-sealing valve is functioning
correctly.
8. Conclusion
Test plugs for Pressure and
temperature gauge are invaluable tools in modern industrial and
commercial systems. They simplify routine testing, enhance safety, and allow
technicians to maintain optimal operating conditions without disrupting
workflow. By choosing the right test plug for your application and following
recommended usage practices, you can maximize efficiency, improve safety, and
ensure reliable, accurate system performance.
Comments