Maximizing Precision in Industrial Weighing: A Guide to Weight Indicators, Weighing Controllers, and
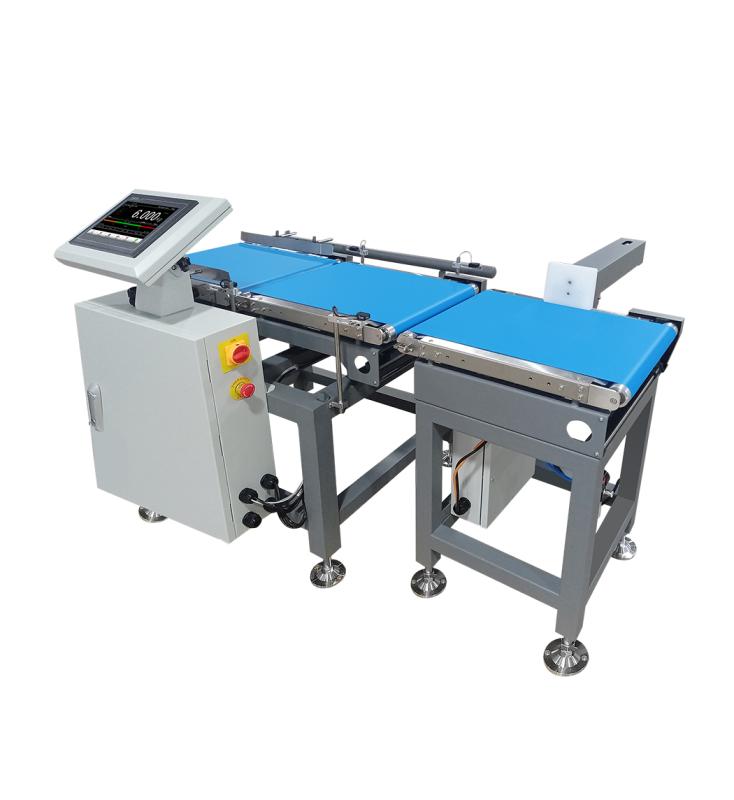
In today's industrial landscape, accurate weighing and measuring systems are essential for operational efficiency, regulatory compliance, and cost management. Whether you're dealing with bulk materials or delicate packages, understanding the various components of industrial weighing systems is crucial. In this article, we will explore weight indicators, weighing controllers for batching, checkweighers, weigh controllers, weighing scale indicators, and automatic checkweighers. By the end of this guide, you’ll have a comprehensive understanding of these essential tools and how they contribute to precise measurements in diverse industrial applications.
Understanding Weight Indicators and Their Role
Weight indicators are the heart of any weighing system, displaying the measured weight and often transmitting data to other devices. These devices are typically connected to load cells that sense weight and send data to the indicator, which then processes and displays the reading. Weight indicators come in various types, including digital and analog, and can offer additional functionalities like data storage, integration with other systems, and remote access.
Weight indicators are the heart of any weighing system, displaying the measured weight and often transmitting data to other devices. These devices are typically connected to load cells that sense weight and send data to the indicator, which then processes and displays the reading. Weight indicators come in various types, including digital and analog, and can offer additional functionalities like data storage, integration with other systems, and remote access.
For industries that handle large volumes, such as agriculture, construction, or logistics, weight indicators ensure that the correct amount of material is processed, loaded, or shipped. This precision minimizes waste, optimizes operations, and enhances quality control.
The Significance of Weighing Controllers in Batching Applications
When it comes to batching, a process commonly used in industries like food processing, pharmaceuticals, and chemical manufacturing, precision is key. A weighing controller for batching provides the required level of control over multiple ingredients, ensuring that each component is measured accurately and mixed in the correct proportions. Weighing controllers work by regulating the flow of materials, often through valves, conveyors, or feeders, to meet exact weight requirements.
These controllers also offer automated functionalities that can adjust for fluctuations in material flow, reducing human error and improving the efficiency of the batching process. By using a weighing controller for batching, manufacturers can maintain consistent quality in their products and meet stringent regulatory requirements.
Checkweighers: Ensuring Product Consistency and Quality Control
Checkweighers are essential tools for quality control, ensuring that each product meets specific weight criteria. Used in a variety of industries, from food and beverage to pharmaceuticals and consumer goods, checkweighers help detect underweight or overweight products, which can then be rejected or diverted.
Modern checkweighers integrate advanced technology like high-speed sensors and digital load cells to provide accurate and rapid weight measurements. They can handle various product types and sizes, making them versatile additions to any production line. By preventing non-compliant products from reaching customers, checkweighers protect brand reputation and ensure regulatory compliance.
The Role of Weigh Controllers in Industrial Settings
A weigh controller is a device that manages and regulates the weighing process in industrial environments. These controllers can handle complex tasks, such as controlling the feeding and discharge of materials, managing multi-ingredient recipes, and ensuring precision in the weighing process.
Weigh controllers are often integrated with other systems, such as conveyors and feeders, to streamline operations and improve accuracy. In addition to weight measurement, they can monitor parameters like flow rate and process timing, providing a comprehensive solution for managing industrial weighing tasks. This level of control enhances efficiency and supports consistent production quality.
Weighing Scale Indicators: Displaying and Transmitting Critical Data
Weighing scale indicators are the display units for weighing scales, showing the weight measurements in real time. These indicators are crucial for environments where operators need immediate feedback on weight data, such as during loading, unloading, or mixing processes.
Modern weighing scale indicators offer various connectivity options, allowing data to be shared with other devices, such as computers, printers, or PLCs (Programmable Logic Controllers). With features like data logging and remote monitoring, these indicators enhance productivity and enable better decision-making based on accurate, real-time information.
Automatic Checkweighers: Automation for High-Speed Accuracy
Automation checkweighing are designed to handle high-speed weighing tasks with minimal human intervention. These systems are particularly useful in fast-paced industries where products move quickly along production lines. Automatic checkweighers are equipped with sensors and software that allow them to weigh products on the fly, instantly identifying items that fall outside the acceptable weight range.
Automation in checkweighing not only speeds up the production process but also increases accuracy and consistency. With the ability to weigh hundreds of products per minute, automatic checkweighers are indispensable for large-scale manufacturing operations. This automation reduces manual labor, lowers operational costs, and enhances overall productivity.
Key Features to Look for in Industrial Weighing Systems
When selecting equipment like weight indicators, weighing controllers, or checkweighers, it’s important to consider several features that can affect performance and compatibility:
Accuracy and Precision: Look for devices with high accuracy ratings to ensure precise measurements.
Durability: Industrial environments can be harsh, so choose equipment built to withstand conditions like dust, moisture, and temperature fluctuations.
Connectivity: Modern weighing systems should offer options for data connectivity, allowing seamless integration with other industrial systems.
User-Friendly Interface: Equipment with intuitive controls and displays can simplify operation and reduce the likelihood of errors.
Automation Capabilities: For high-volume applications, automation can significantly boost productivity and accuracy.
The Benefits of Integrating Weighing Systems in Industrial Operations
Integrating weighing systems into your operations offers multiple benefits, such as improved accuracy, enhanced productivity, and better compliance with industry regulations. With real-time data on material weights, companies can optimize their supply chain, reduce waste, and ensure product consistency.
Weighing systems also support automated reporting, which simplifies record-keeping and provides valuable insights into operational efficiency. By using advanced weighing technologies, companies can achieve greater precision in their manufacturing processes, ultimately leading to higher-quality products.
Comments