The Essential Role of Weighing Controllers in Modern Industrial Processes
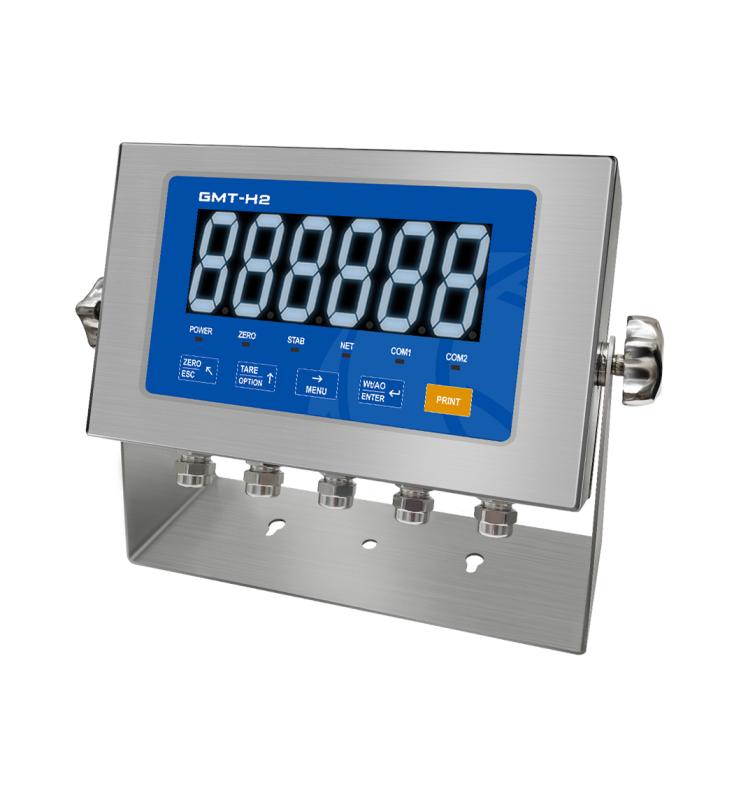
In today’s highly automated industrial landscape, weighing controllers play a pivotal role in ensuring precision, efficiency, and reliability across a range of industries, from manufacturing and agriculture to logistics and packaging. These advanced devices are crucial for maintaining accurate measurements, streamlining production lines, and enhancing overall productivity.
What is a Weighing Controller?
A weighing controller is a specialized instrument designed to monitor, control, and regulate weight measurements in various industrial processes. It integrates with load cells, sensors, and other weighing equipment to deliver real-time data that is essential for process control. Whether it's for batching, filling, or packaging, a weighing controller ensures precise weight management by automating the entire weighing process.
Weighing controllers are often used in industries that require high accuracy and reliability, such as pharmaceuticals, food processing, and material handling. They not only ensure that products meet stringent quality standards but also help companies optimize their resource usage and minimize waste.
Key Features of Weighing Controllers
High Accuracy: Weighing controllers are designed to provide precise measurements down to the smallest increments. This level of accuracy is critical in applications like batch production, where even minor discrepancies in weight can affect product quality.
Real-Time Data Monitoring: Most modern weighing controllers come equipped with digital displays and remote monitoring capabilities. This allows operators to view real-time data, adjust settings, and make necessary changes without interrupting the production process.
Customizable Settings: Depending on the application, weighing controllers offer customizable parameters for speed, precision, and control limits. This flexibility is particularly useful in complex processes like mixing or blending, where the controller must adjust weights dynamically.
Connectivity and Integration: Weighing controllers often come with communication interfaces such as Ethernet, RS232/RS485, or Modbus, enabling them to be integrated into larger control systems. This allows for seamless data flow between the controller and other automation equipment, improving overall system efficiency.
Applications of Weighing Controllers
Batching Systems: In industries like food production, chemical processing, and construction, batching systems rely heavily on weighing controllers to measure and dispense precise amounts of material. Accurate batching ensures that each batch is consistent in quality and meets regulatory standards.
Filling Machines: For manufacturers of liquids, powders, or granular materials, weighing controllers are used in filling machines to control the amount of product dispensed into containers. This prevents overfilling or underfilling, both of which can lead to product loss and customer dissatisfaction.
Packaging Systems: Weighing controllers are an integral part of packaging machines, ensuring that the right amount of product is packed in each container. This is crucial for maintaining product quality and preventing costly errors that can arise from improper weighing.
Checkweighers: In quality control systems, checkweighers are used to verify the weight of finished products. A weighing controller helps ensure that each item meets the specified weight range, rejecting any that are under or overweight.
Advantages of Using Weighing Controllers
Increased Efficiency: By automating the weighing process, controllers eliminate the need for manual intervention, which speeds up production and reduces the likelihood of errors. This increases overall throughput and allows for more efficient use of resources.
Cost Savings: Weighing controllers help reduce material wastage by ensuring accurate measurements. This not only minimizes the cost of excess materials but also helps avoid fines and penalties for non-compliance with weight regulations.
Enhanced Product Quality: Consistent weight measurements are essential for maintaining product quality. Weighing controllers ensure that products meet exact specifications, which is crucial in industries where quality is tightly regulated.
Data Logging and Reporting: Many modern weighing controllers are equipped with data logging features that allow operators to track weight measurements over time. This data can be used for quality assurance, auditing, and process optimization.
Conclusion
The weighing controller is a vital component in modern industrial processes, offering high precision, real-time monitoring, and seamless integration with other automation systems. Whether used in batching, packaging, or quality control, it enhances efficiency, reduces waste, and ensures consistent product quality. For industries looking to optimize their operations, investing in a reliable and advanced weighing controller is a key step toward achieving better results.
Comments