In-motion Checkweigher: Ensuring Efficient and Accurate Weight Control
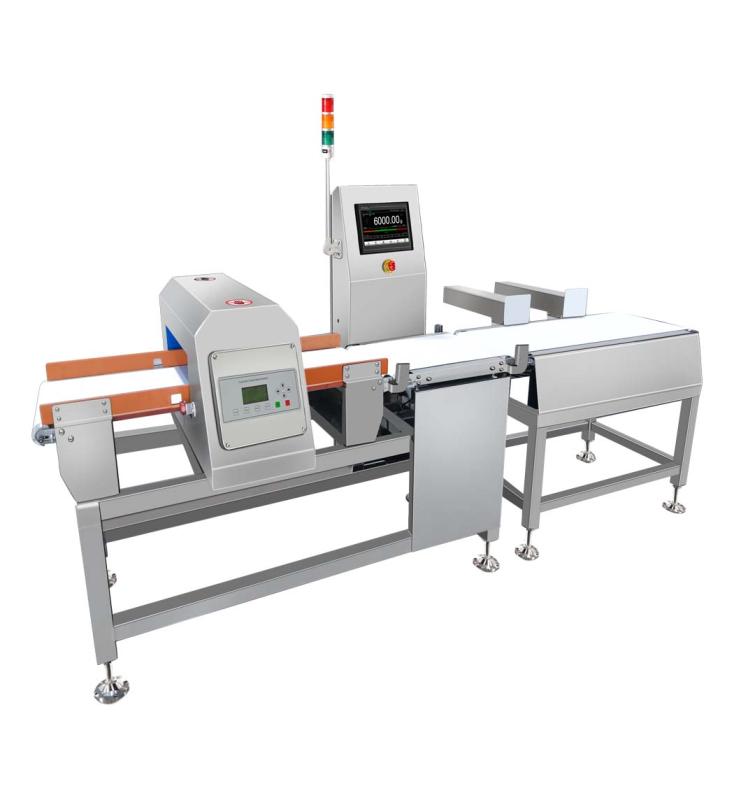
An In-motion Checkweigher is an essential piece of equipment used in industries that require accurate and efficient weight monitoring for products moving along a production line. Unlike static checkweighers, the in-motion version allows for real-time weight checking without stopping the conveyor system. This functionality increases productivity, especially in high-speed environments like packaging, logistics, and manufacturing.
In-motion checkweighers are designed to automatically reject products that are under or overweight, ensuring that only items within the specified weight range proceed to the next phase. This helps businesses maintain product consistency, avoid legal complications regarding weight discrepancies, and reduce product giveaways.
Some key features of in-motion checkweighers include high-speed sensors, touchscreen controls, and easy integration with existing production systems. With technological advancements, these machines now offer data collection and analysis, helping companies improve their production processes based on real-time feedback. The reliability and accuracy of an in-motion checkweigher make it indispensable in industries such as food and beverage, pharmaceuticals, and manufacturing, where precise weight measurement is critical for quality control.
Load Cell Indicators: Accurate Measurement for Precision Weighing
Load Cell Indicators are crucial devices that display weight information obtained from load cells. Load cells are sensors that measure force or weight, and indicators translate this data into readable and actionable information for operators. They are used in various industries, including agriculture, logistics, and industrial manufacturing, where precision weighing is essential for production and compliance.
A load cell indicator connects to multiple load cells and consolidates the readings into a single display, allowing operators to monitor and control weight in real-time. These indicators are often found in industrial scales, weighing platforms, and bulk material handling systems. One of the critical features of modern load cell indicators is their ability to provide accurate digital readouts, which can be integrated into automated systems for seamless operations.
With advancements in technology, many load cell indicators come with features such as high-contrast displays, data logging, remote access, and user-friendly interfaces. These features improve operational efficiency by providing quick and precise feedback on weight measurements. As businesses continue to automate their operations, load cell indicators play a vital role in ensuring accuracy and reducing human error in weight management processes.
Remote Display: Enhancing Operator Efficiency with Real-Time Data
A Remote Display is a vital tool that provides real-time visibility of weight and measurement data from weighing systems at a distance. It’s commonly used in environments where operators need to monitor weighing systems from different locations. Remote displays can be mounted on walls or placed on control panels, giving operators flexibility in how they manage production and logistics processes.
These displays are often used in conjunction with weighbridges, in-motion checkweighers, and bulk weighing systems to ensure that operators always have access to the necessary data, even from afar. This is especially useful in large facilities or environments where the weighing equipment is located far from the control room.
Modern remote displays come equipped with features like large LED or LCD screens, wireless connectivity, and compatibility with various weighing systems. This not only improves operational efficiency but also enhances safety by reducing the need for personnel to be near potentially hazardous weighing areas. The ability to access weight data remotely is critical for industries such as logistics, manufacturing, and agriculture, where speed and precision are essential.
Bagging Scale: Streamlining the Packaging Process with Precision
A Bagging Scale is an essential tool in industries where materials need to be weighed and packed accurately. These scales ensure that the correct amount of material is bagged, reducing waste and increasing efficiency in the packaging process. Whether it’s grains, powders, or other bulk materials, bagging scales provide fast and accurate measurements, ensuring that each bag meets the desired weight specification.
Bagging scales can be automated or semi-automated, depending on the production scale. They come with features such as high-precision load cells, user-friendly interfaces, and fast bagging speeds, which make them ideal for use in industries like agriculture, food processing, and chemicals. With an automated system, bagging scales can dispense material, weigh it, and then seal the bag in a single seamless process.
One of the main advantages of using bagging scales is their ability to minimize errors and ensure consistent packaging, which helps maintain product quality and reduce costs. In many cases, these scales are integrated with conveyors and other automated systems to streamline the entire production process, making them an indispensable tool for businesses looking to optimize their packaging operations.
Comments