How to prolong the working life of your pellet machine?
Types of pellet machines
Roughly, wood pellet machine can be classified into flat die pellet machine and ring die pellet machine. In flat die pellet machine, the roller is installed on the flat die and the pressure is downward. In ring die pellet machine, the roller is installed in the center of the ring die, the pressure is outward. Usually, ring die pellet machines have the production capacity more than 1t/h, while flat die pellet machines are less than 1t/h.
The size of dies
The pellet output is also determined by the size of dies. The number of holes on φ560 ring die is one third less than that on φ700 ring die. Therefore, under the same rotating speed, the production is half less. In terms of dies of the same size, the larger the hole size, the less the number of holes, and the less the pellet production. Usually, the hole sizes of the flat die is 4mm, 6mm and 8mm. 8mm flat die has much less holes than 4mm flat die.
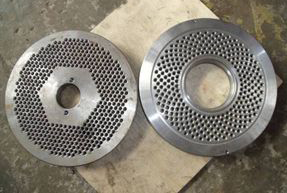
Electric motor power
Ring die pellet machine usually adopts 4-grade electric motor. The rotating speed is 1450-1500r/h, and the main shaft also have a certain speed after reduction. For raw materials with high hardness and too much fibers, the pellet output will decline. So they need larger power to ensure the production.
In terms of flat die pellet machine, the larger the size, the higher the power, and the larger the production capacity.For hard raw materials, only high-power pellet machine can complete the work.
The clearance between roller and die
The suitable clearance between roller and flat die is 0.1-0.3mm. If the clearance is larger than 0.3mm, the raw material layer will be too thick, and the roller is easy to slip, so the pellet output will decline.
In ring die pellet machines, the central line of the roller and ring die should be the same, or the pressures on the 2 sides of the roller are different. As we know, the instant pressure of roller on the ring die can reach up to 4000t, any deviation would increase local pressure by multiple times.
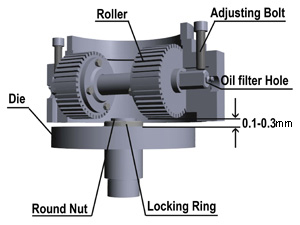
Raw materials property
Due to different cellulose and lignin content, raw materials has different adhesive force. For example, sawdust has high forming rate, while rice husks need to be mixed with other materials to improve the forming rate. To improve the pellet output, you can add some binders to raise the forming rate.
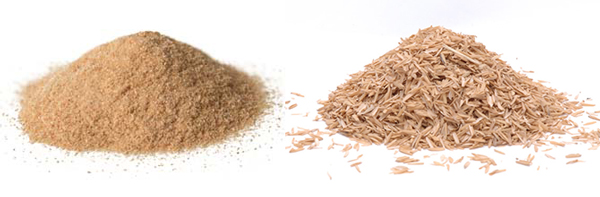
How to improve the output of wood pellet machine?
Check the compression ratio of dies
For new pellet machine or new die, you should check if the compression ratio matches with the raw material. If the compression ratio is too large, the raw materials receive more resistance when they pass through the die holes. The produced pellets are too hard and the output is low. If the compression ratio is too small, the pressed raw materials are not formed. If the die holes are irregular and rough inside, the wood pellets are hard to get out.
Check the abrasion of the roller and die
The wear of the roller and die will affect the production capacity. If the ring die wears severely, you need repair it, and countersink the holes. In terms of flat dies, you turn it over to use the other side when one side wears out. If the rollers wear out, you must replace them, or the pellet output would decline seriously.
Control the quality of raw materials
The moisture content of raw materials for making biomass pellets is between 14% and 20%. If the moisture content is too high, the raw material will slip on the die and not easy to be extruded out. If the materials are too dry, the forming rate will be affected.
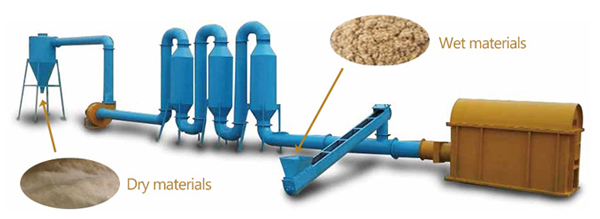
The fineness of raw materials also influence the forming rate of pellets. If the size of raw materials are too large, the abrasion of the roller and die and the power consumption will increase, and the production will decline. It's neccessary to prepare a hammer mill to crush the biomass materials into small size.
Grind the new die before production
Some new dies has scrap iron and oxide attached to the inner wall of the holes. They need to be polished to reduce the frictional draw and improve the pellet production. Before installing the die in the pellet machine, you can use a drill to clear the iron bits inside the holes.
Grind the die holes with oil mixture. The oil mixture is composed of waste oil, sand and sawdust. Feed the oil mixture into the pellet machine and repeat this process for 20-30min. Then start the machine and feed it with oil mixture (mixed waste oil, sand and sawdust). Repeat this process for 20-30min. With the increase of the smooth finish, the produced pellets should be loose.
Check if there are holes get blocked
The holes blockage arise from such reasons: using unqualified raw materials; the new dies are not grinded; raw materials coking when the pellet machine continue to work when holes are blocked; holes are not filled with oil mixtures after pelletizing. When the holes are blocked, you can use a drill to burst it through. If it doesn’t work, you can dip the die into a container filled with engine oil, and heat it if necessary.
Beside, every time after you finish pellet production, remember to feed oil mixtures to the pellet machine and let them fill the holes on dies. In this way the dies are free from blockage, and it can save your time for the next time pelletizing.
Comments