How to maintain pellet mill die and roller?
The roller and die are the wearing parts in a pellet machine. To use and maintain them in right way can reduce the failure rate, improve the production, raise the working efficiency, save time and labor. If there is any problem in the roller and die, the forming rate and production would decline.
Fill the die with oil mixture
Every time after using, or when you want to replace the die, remember to feed oil mixture (mixed sawdust and waste oil) to the pellet machine, squeeze out all the biomass materials and fill the die holes with oil mixture.
The biomass materials contains moisture, which would accelerate the corrosion of the die, and cause it rough inside. The oil mixture filled in the die doles will protect them from rusting or corrosion.
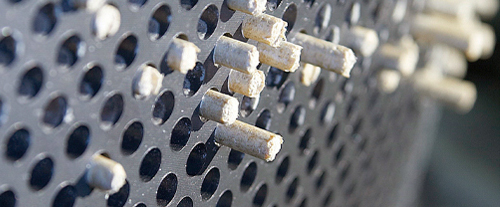
Replace the oil mixture every half a year
If you have leaved the pellet mill die aside for over a half year. You need to replace the oil mixture in the die for new, or they would harden and block the holes. This will affect the use for next time.
Solve the block of the pellet mill die
If the die holes are blocked and the wood pellets don’t come out, we can use oil soak or cooking to soften the raw materials, and make pellets again. If this method doesn’t work, you can use drills to extrude the raw materials out, and feed oil materials and fine sand mixture to grind the die.
Place the spare parts in right places
Preserve the pellet mill dies in ventilate and dry place. If preserved in damp place, they will corrode easily. If you don’t use it for long time, you can coat it with a layer of waste oil to prevent corrosion of moisture in the air. Don’t put the pellet mill die where the raw materials are stored. The raw materials are easy to absorb moistures, which would accelerate the corrosion of the die.
Smooth the die and chamfer the die orifices
The holes on the pellet mill die are processed by high-speed gun drill, which has high smoothness. Check if there is any bulges on the surface of the die, if so, smooth them with a flint glazing machine. If the die orifice are sealed or have inversion, you should chamfer the die orifices and renovate it.
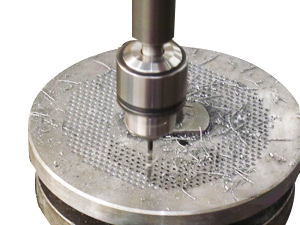
Adjust the clearance between the roller and die
In flat die pellet machine, the suitable clearance between roller and die is 0.1-0.3mm. If the clearance is too small, the abrasion between the roller and die will intensify. If the clearance is too large, the raw materials layer will be thick and the production will decline. In ring die pellet machine, the suitable clearance is 0.1-0.4mm.
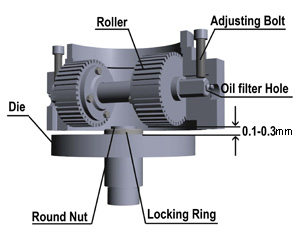
Keep the pellet mill die and roller clean
When the wood pellets have worked for 30 days, you need to clean up the roller and die with diesel or gasoline. Coat them with lubricant oil and install them again. To ensure steady high production, we should keep the inside of the die clean.
If the ash is attached to the roller or the lubricating oil is insufficient, the rollers would rotate unsteadily, and the production speed will be affected. Users should check the working condition of rollers regularly.
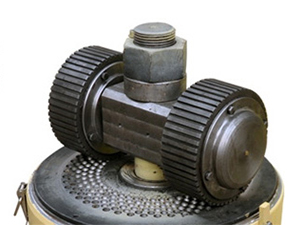
Preheat the pellet machine
Every time before making wood pellets, feed the oil mixture repeatedly until the temperature inside is up to 50℃. Then you can feed the biomass materials to make pellets.
In winter, as the weather is cold, the die is frail, we should preheat the machine for longer time, so that the pellet machine can work better, the production is higher, and the service life is longer.
Ensures raw materials quality
During the working of wood pellet machine, you should ensure there is no stones or irons in the raw materials, in case they cause damage to the die.
The moisture content in the raw materials should be 10%-18%. Dry material are hard to mold, which will intensify the abrasion of the pellet machine. If the raw materials are too damp, the moisture would evaporate and mix with the wood powders, and block the holes on die.
Comments