Granulating and mixing equipment
Granulating and mixing equipment
Most of China injection moulding companies cannot go to the expense of having a complete reprocessing plant consisting of
granulator, mixer/extruder, and die face or lace cutter. The general
arrangement is to have a room in a fairly remote corner of the building where
material can be granulated using an ordinary masson type cutter. Although this
produces re-work of irregular shaped particle size,with a fair
amount of powdery material,it is perfectly satisfactory for injection moulding.
- Granulators.
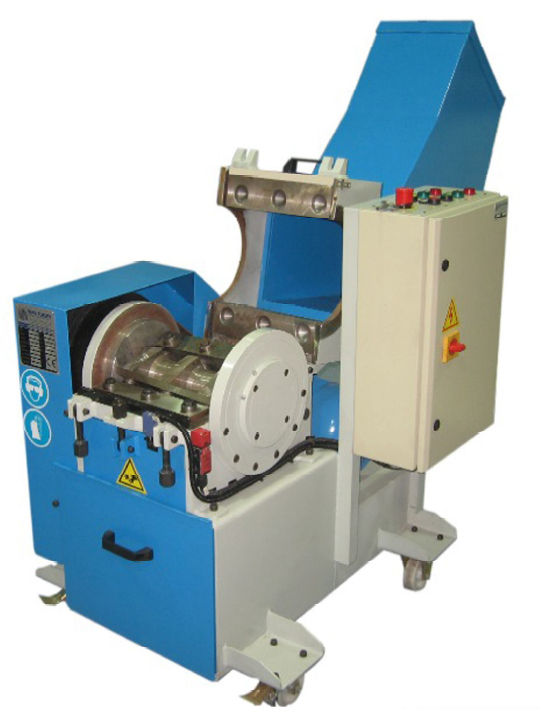
The normal granulator has a powerful electric motor driving a heavy rotor,to which are
clamped two or more stout cutting blades. The rotor and blades are a clearance
fit in a cylindrical chamber having a set of stationary knives. A long feed
throat with spring-loaded baffles prevents injury to the operator and also
stops pieces of material from flying back from the cutting chamber. About
one-third of the cylinder wall of the cutting chamber consists of a screen of
suitable size to allow granules for moulding to pass through and a tray
underneath catches the granulated plastic.
This type of machine is extremely noisy and the operator wears ear muffs. It also creates a lot of dust and must be against an outside wall,and well ventilated. The walls of the room or cabinet should be of double skin or of sound-insulating block board.
One important hazard which must
not be overlooked is that of dust. Any accumulation of plastic powder should be
prevented because, if this were to be disturbed and form into a dust cloud,a spark even
static electricity could cause an explosion. Material for granulating must be
kept free from dirt and moisture and when the re-grind is being used in the
moulding machine,a magnetic screen to prevent access to the cylinder of any small
pieces of ferrous metal from the cutting knives should be inserted in the feed
hopper.
- Mixing equipment.
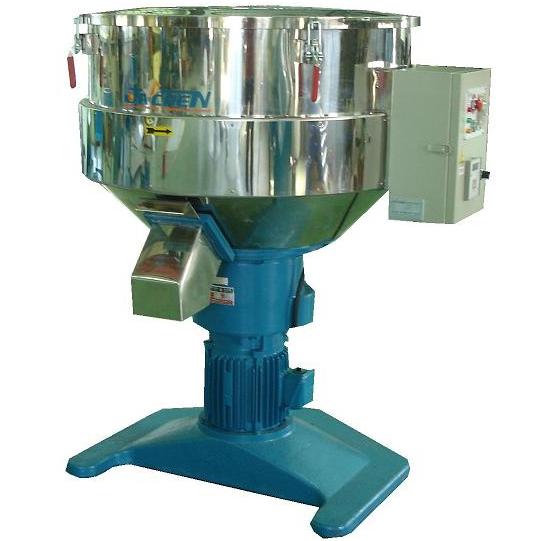
Mixing equipment can be simple or complicated. For small quantities
of up to 5 kg,a polythene bag of double the capacity of the material can be used.
The ingredients are placed in the bag,which is then
screwed up from the open end to seal it and to trap a volume of air. This allows
the material to be shaken about in the bag and gives extremely good mixing in a
few minutes- For larger quantities,mechanical mixing is
desirable.
The simplest mechanical mixer consists of a
drum capable of holding,say, 50,100 or 200 kg of material. This is mounted on a framework which can
be rotated by an electric motor,causing the drum to tip end-over-end. Not more than half the
capacity of the drum should be mixed at one time. Some equipment is so arranged
that the drum does not rotate end-to-end but diagonally,corner to
corner. Baffles may also be mounted inside the drum. Many machines are designed
to accommodate the standard drums used in industry.
More sophisticated mixers work on the same
principles but have variously shaped mixing chambers,with a view
to getting better mixing action. Thorough mixing takes time and it cannot be
expected that the best blending, say, of colour in a 100 kg batch would be
achieved in less than 20-30 min.
Where large quantities of material,such as coloured masterbatch and natural polymer,are to be mixed, mechanical equipment which meters the correct amount of each ingredient from separate bulk storage silos is used. The material passes along a tube having in it an Archimedean screw which rotates and gives a mixing action as it conveys the plastic.
Other systems use a tube with a series of baffles which cause
turbulence in a current of air used to convey the plastic and so bring about
mixing. It should be remembered that any device,such as a mixer or
conveyor, that introduces a current of air into the plastic, whether directly
or by breaking a vacuum, should be looked on as a means of allowing the ingress
of moisture. Such devices would not be recommended for use with the more
hydrophylic plastics,such as nylon,acrylic,ABS,and polycarbonate, unless the air was completely dry.
Comments