Optimizing Manufacturing Workflows & Product Lifecycle with Data Collection Services
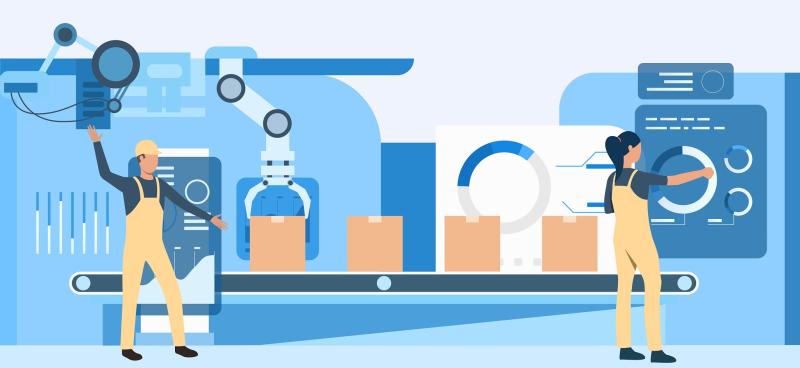
Advanced technologies such as RPA, AI, and ML have painted a new picture of the modern manufacturing landscape. The integration of these technologies has made the processes more efficient, adaptive, and scalable. In fact, manufacturers don't have to struggle anymore to increase productivity or firefight issues, while gaining operational efficiencies and ensure compliance. Can you guess what is at the heart of this transformation? Data collection.
Process at Glance: Data Collection in Manufacturing
Manufacturing is a data-intensive domain where every stage, from design to production and distribution, literally spews vast quantities of data. Traditionally, the data was collected using pen and paper where the operators present on shop floors used to manually record information such as machine readings, record process results, register stops, etc. What’s even more surprising, manually counting the entire throughput!
Obviously, the process was time-consuming, prone to human errors, and lacked real-time insights or feedback. Thanks to advanced data collection solutions, manufacturers don’t have to struggle with this non-core but important process. In fact, integrating AI in data collection helps manufacturers filter out “noise” from the data and derive actionable insights in real-time.
While there are plenty of ways to collect manufacturing data, it solely depends on the type of facilities available on the shop floor. Some of the common methods used by a professional data collection company include Supervisory Control and Data Acquisition (SCADA) systems, RFID, IoT sensor integration, observations, surveys, document reviews, and more.
Wait there’s more! Other than the technological equipment, manufacturers can also leverage “human sensors.” Wondering who they are? The frontline workers. Being on the factory floor, they are the first ones to experience safety, quality, and maintenance issues. That said, equipping these workers with appropriate tools helps in collecting shop floor data more effectively.
Next comes the type of data! Well, it depends on the nature of work, devices used, and the area of operation. All these factors determine the type of data generated on the shop floor. It can be inventory data to track items that are underutilized, and the ones that have to be restocked. Or think of machine data such as machine performance metrics, equipment runtime and downtime, and other machine-related problems.
Other than inventory and machine data, there’s quality and inspection data like energy consumption, production rates, quality control statistics, environmental conditions, etc. Collecting and analyzing this shop floor data allows manufacturers to make informed decisions and enhance operational excellence.
Benefits of Data Collection in Manufacturing
1. Enhancing Operational Efficiency
Offline and online data collection helps manufacturers improve bottom line efficiency. How? A thorough analysis of collected data such as equipment performance and production metrics allows manufacturers to identify bottlenecks and areas for improvement.
Consider the case of machine downtime. It can be minimized through predictive maintenance, which uses data collection and analysis to forecast potential equipment failures before they disrupt business operations. Isn’t this a smart way to reduce maintenance costs while ensuring uninterrupted production?
2. Optimal Resource Usage
Shop floor data collection offers valuable insights into production workflows and processes. Without this visibility, how can you determine whether the resources are used optimally? Certainly, there’s no other way! Collecting and analyzing patterns in energy consumption, raw material usage, and workforce productivity helps stakeholders map out strategies for waste minimization. Besides, take this as a pro tip to enhance profitability and contribute to sustainability!
3. Improving Quality Control
Product quality is important in the manufacturing sector. Data collection allows you to monitor production processes continuously and ensure that quality standards are met consistently. Sensors embedded in production lines, for example, measure variables such as temperature, pressure, and dimensions in real-time. The sensors trigger alerts if there’s any deviation from predefined thresholds, allowing operators to take corrective measures promptly.
What’s more? Manufacturers can identify the root cause of defects and prevent recurrence by analyzing the collected historical data. And, as a ripple effect of this, companies achieve higher product consistency, reduced returns, and enhanced customer satisfaction.
4. Continuous Improvement
The adage “there’s always room for improvement” stands true for manufacturing processes. Data collection helps with process improvement. How? Monitoring the collected data allows manufacturers to identify areas that are performing well and loopholes in the process if any. In short, it provides the baseline to measure success and determine if there’s any improvement in the business outcomes or not.
There’s more here! Continuous improvement leads to higher product quality and reduced resource waste. Above all, manufacturers can save big deals on cost and time!
5. Enhancing Product Lifecycle Management
Product lifecycle management implies overseeing a product right from its inception to its end of life. Can you connect the dots between data collection and product lifecycle management? The process provides a continuous feedback loop, allowing manufacturers to make informed decisions during each phase:
• Design and Development – data from previous products helps in making better design choices and accelerates time-to-market.
• Production and Distribution – real-time tracking ensures optimal production rates and on-time delivery
• End-of-Life Recycling – detailed product data helps in efficient recycling and material discovery
Closing Thoughts
Data collection is undoubtedly an important process in the manufacturing industry. It lays the foundation for effective processing and analysis that drives informed decision-making. Thus, any discrepancy during the data collection process can negatively impact an organization. And given the resource-intensive and time-consuming nature of the process, errors are bound to happen.
So, what’s the solution? Investing in data collection services. They have the required resources to collect manufacturing data effectively. Above all, they follow the industry’s best practices and adhere to compliance standards. Thus, businesses get access to regulatory compliant manufacturing data to make informed decisions and achieve operational excellence.
Comments