Electron Beam Welding: The Future of Precision Welding
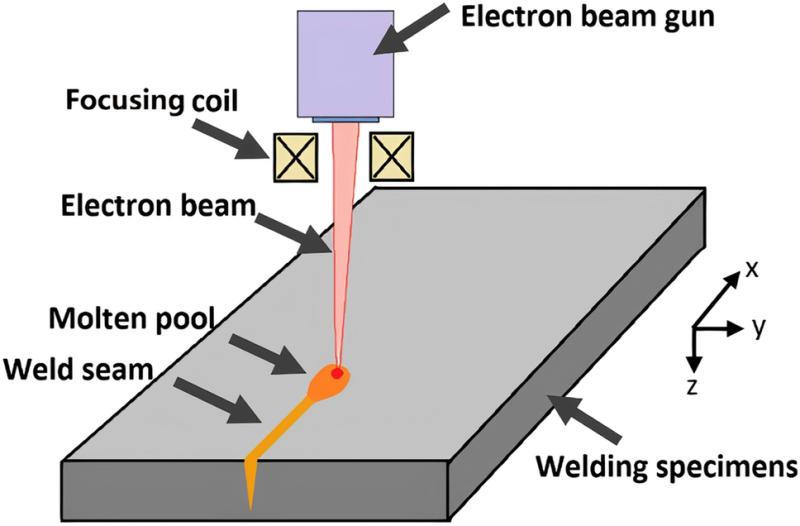
As industries continue to demand higher levels of precision, efficiency, and durability in manufacturing processes, electron beam welding (EBW) has emerged as a cutting-edge solution. This advanced welding technique is revolutionizing how metals are joined, offering unparalleled benefits in applications where traditional methods fall short. From aerospace to medical devices, the versatility and precision of EBW make it an attractive choice for a wide range of industries. In this article, we explore why electron beam welding is considered the future of precision welding.
What is Electron Beam Welding?
Electron beam welding (EBW) is a specialized, high-energy welding technique that uses a focused stream of high-velocity electrons to melt and join metals. Unlike conventional welding methods, which rely on a heat source such as a flame or electric arc, EBW uses an electron beam generated in a vacuum environment. The electron beam is directed at the metal workpieces, causing the atoms at the point of contact to rapidly vibrate, generating the heat necessary to melt the material.
The process typically takes place in a vacuum chamber, which prevents contamination and oxidation, leading to cleaner welds. This makes EBW particularly suitable for high-precision, high-performance applications, such as aerospace, automotive, electronics, and medical device manufacturing.
The Key Benefits of Electron Beam Welding
1. Unmatched Precision and Control
Electron beam welding Benefits is gaining popularity due to its exceptional precision. The focused electron beam enables fine control over the weld, ensuring minimal heat input and small, accurate weld pools. This is ideal for high-tolerance applications, where small deviations can compromise product integrity. Additionally, it reduces distortion with a low heat-affected zone, allows for welding of dissimilar materials, and prevents oxidation in a vacuum environment, ensuring cleaner, stronger joints. These benefits make it a preferred method in industries like aerospace, medical devices, and electronics.
In traditional welding methods, heat often spreads beyond the intended weld area, potentially distorting the surrounding material. EBW, on the other hand, minimizes this thermal spread, preserving the structural integrity of delicate components.
2. Deep Weld Penetration with Minimal Distortion
EBW can achieve deep weld penetration without significantly affecting the surrounding material, which is crucial in industries where strength and durability are paramount. The ability to produce deep, narrow welds means that less material is needed to form a strong bond, contributing to lighter, more efficient structures.
Additionally, because the process generates minimal heat, there is less risk of thermal distortion or warping, making EBW ideal for high-precision parts and assemblies that require tight tolerances.
3. High Efficiency and Speed
Electron beam welding is highly efficient due to its vacuum environment, which minimizes heat loss and maximizes energy use. The focused electron beam enables rapid heating and faster welding times compared to traditional methods.include industries like aerospace, where it joins critical components such as turbine blades, and medical device manufacturing for high-precision implants. In electronics, it’s used for delicate components like circuit boards. These applications highlight electron beam welding's efficiency and versatility in producing high-quality, precise products.
In industries where production speed is critical, such as automotive manufacturing, EBW offers significant time savings without sacrificing the quality of the weld. Furthermore, the precision of the technique reduces the need for additional post-weld processing, further speeding up the overall manufacturing process.
4. Minimal Heat-Affected Zone (HAZ)
The heat-affected zone (HAZ) is the portion of the material adjacent to the weld that experiences changes in mechanical properties due to heat exposure. In traditional welding, a large HAZ can lead to structural weakness or compromised material properties, particularly in high-performance alloys.
With EBW, the heat input is highly concentrated in the weld area, resulting in a very narrow HAZ. This minimizes the risk of unwanted material property changes, ensuring that the weld’s strength and performance are maintained across the entire workpiece. This is particularly important in industries like aerospace and medical device manufacturing, where material integrity is crucial.
5. Ability to Weld Thick Materials
While many welding methods struggle with thicker materials, EBW excels at joining thick metal parts. The concentrated energy from the electron beam allows for deeper penetration, which is essential when working with materials like titanium, steel, or exotic alloys.
The ability to weld thicker sections without excessive heat input means that EBW can be used to fabricate large, robust components for industries like aerospace, where structural integrity is critical. Moreover, because the electron beam is so focused, the process can still achieve high levels of precision even when working with larger workpieces.
6. Clean and Contaminant-Free Welds
Since Electron beam welding Benefits occur in a vacuum environment, the risk of contamination is significantly reduced compared to traditional welding methods. The absence of air allows the process to be free from oxidation, oxidation byproducts, and other impurities that can affect the quality of the weld. This is especially important in industries such as medical device manufacturing, where cleanliness and sterility are paramount.
Furthermore, the reduced risk of contamination ensures that the welds produced are stronger, more reliable, and free from defects, such as porosity or inclusions, which can compromise the integrity of the final product.
Applications of Electron Beam Welding
The precision and versatility of EBW have led to its adoption in a wide range of industries. Some key applications include:
Aerospace: EBW is used extensively in the aerospace industry to weld high-strength, lightweight materials like titanium and aluminum alloys. The process’s ability to achieve deep welds with minimal distortion makes it ideal for aerospace components, such as turbine blades, structural parts, and engine components.
Medical Devices: The medical industry benefits from EBW’s precision and clean welds, which are essential for producing implants, surgical instruments, and other critical components. The ability to weld dissimilar materials, such as titanium and stainless steel, also adds to EBW’s appeal in medical device manufacturing.
Automotive Manufacturing: EBW is used in automotive applications for welding critical components, such as engine parts, exhaust systems, and fuel tanks, where precision and strength are paramount.
Electronics: The electronics industry uses EBW to fabricate small, intricate parts with tight tolerances. This includes components like heat exchangers, semiconductor devices, and connectors.
The Future of Electron Beam Welding
As industries continue to push the boundaries of performance, electron beam welding is poised to play a crucial role in advancing manufacturing technology. Its ability to produce high-quality, precise welds quickly and efficiently will continue to drive its adoption in high-performance industries.
Moreover, as automation and robotics become more integrated into manufacturing, EBW is expected to evolve further, making it even more accessible and cost-effective for manufacturers. As the demand for complex, high-performance parts increases, the benefits of electron beam welding will only become more apparent, solidifying its place as the future of precision welding.
Conclusion
Electron beam welding represents a significant leap forward in welding technology. Its precision, efficiency, and ability to handle complex, high-performance materials make it an indispensable tool for modern industries. As technological advancements continue to shape the manufacturing landscape, EBW will remain a key driver of innovation, offering solutions for some of the most challenging and demanding welding applications.