What Is the Machine Used for Crushing Rocks?
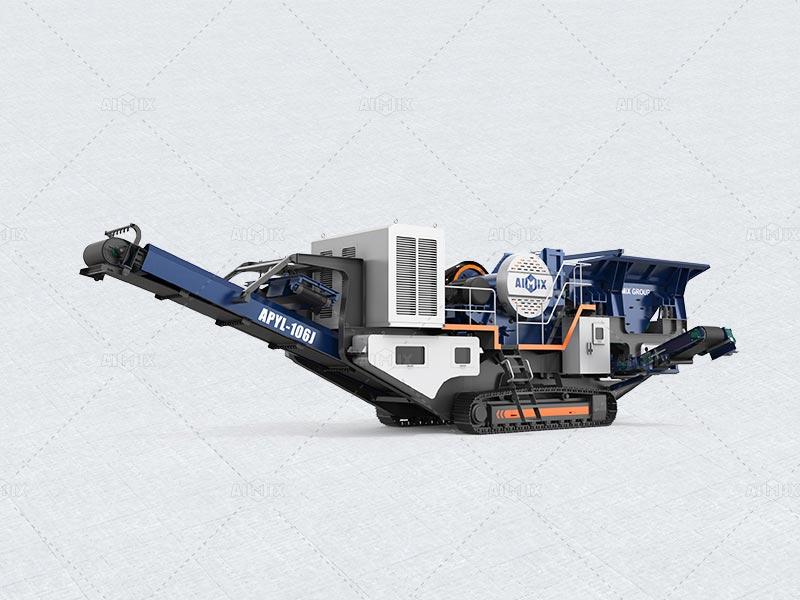
In industries such as mining, construction, and quarrying, the efficient breakdown of rocks is a fundamental process that underpins many operations. From extracting minerals to preparing construction materials, the right machinery can make all the difference. In this article, we'll explore the crusher machine used for breaking down rocks and their significance in different industries.
Types of Rock-Breaking Machines:
A. Hydraulic breakers:
Mechanism and operation:
Hydraulic breakers, also known as rock breakers or hammers, are powerful attachments mounted on excavators or other heavy machinery. They operate by hydraulically-powered pistons that deliver high-impact blows to break down rocks. These machines are versatile and effective for breaking up concrete, asphalt, and hard rock formations.
Applications and limitations:
Hydraulic breakers find applications in various industries, including mining, demolition, and road construction. However, they may not be suitable for all rock types or sizes. Their effectiveness can be limited by factors such as rock hardness, depth of penetration, and equipment compatibility.
B. Rock crushers:
Crushing methods and principles:
Rock crushers are machines designed to crush large rocks into smaller, more manageable sizes. They operate by applying mechanical force to break rocks apart. Common crushing methods include compression, impact, and attrition, each suited to different rock types and sizes.
Varieties and suitability for different rock types:
Rock crushers come in various types, including jaw crushers, cone crushers, and impact crushers. Each type has its advantages and limitations, depending on factors such as feed size, hardness of the rock, and desired final product size. Selecting the right rock crusher machine for the job is crucial for optimizing crushing efficiency and product quality.
C. Explosives and blasting:
Process and safety considerations:
Explosives and blasting are another method used for breaking down rocks, particularly in mining and quarrying operations. This process involves drilling holes into the rock, inserting explosives, and detonating them to fragment the rock. While effective, blasting requires careful planning, strict safety protocols, and compliance with regulatory requirements to minimize risks to personnel and the environment.
Environmental impacts and regulatory measures:
Blasting can have significant environmental impacts, including air and noise pollution, ground vibrations, and fragmentation of rock formations. Regulatory agencies impose strict guidelines and permits to mitigate these impacts and ensure the responsible use of explosives in rock-breaking operations. Measures such as monitoring, reclamation, and community engagement are essential for sustainable blasting practices.
Considerations for Choosing the Right Rock-Breaking Machine:
A. Nature of the rock and its properties:
The characteristics of the rock, including hardness, density, and geological structure, influence the choice of rock-breaking machine. Understanding these properties is crucial for selecting the most suitable equipment and optimizing performance. View more info here.
B. Project requirements and constraints:
Project-specific factors such as budget, timeline, and site conditions play a significant role in determining the appropriate rock-breaking machine. Considerations such as space limitations, access to utilities, and environmental sensitivities may also impact equipment selection.
C. Cost-effectiveness and efficiency factors:
In addition to technical considerations, cost-effectiveness and efficiency are critical factors in choosing a rock-breaking machine. Evaluating factors such as equipment purchase and operating costs, maintenance requirements, and productivity rates can help maximize returns on investment and ensure project success.
In conclusion, the machine that breaks down rocks plays a vital role in various industries, from mining and construction to quarrying and demolition. Hydraulic breakers, stone crusher machine, and explosives are among the primary tools used for this purpose, each with its advantages and limitations. By understanding the characteristics of the rock, project requirements, and cost-effectiveness factors, stakeholders can make informed decisions to optimize rock-breaking operations and achieve their objectives efficiently and responsibly.