The Future of Industrial Equipment & Tools: Innovation Driving Efficiency
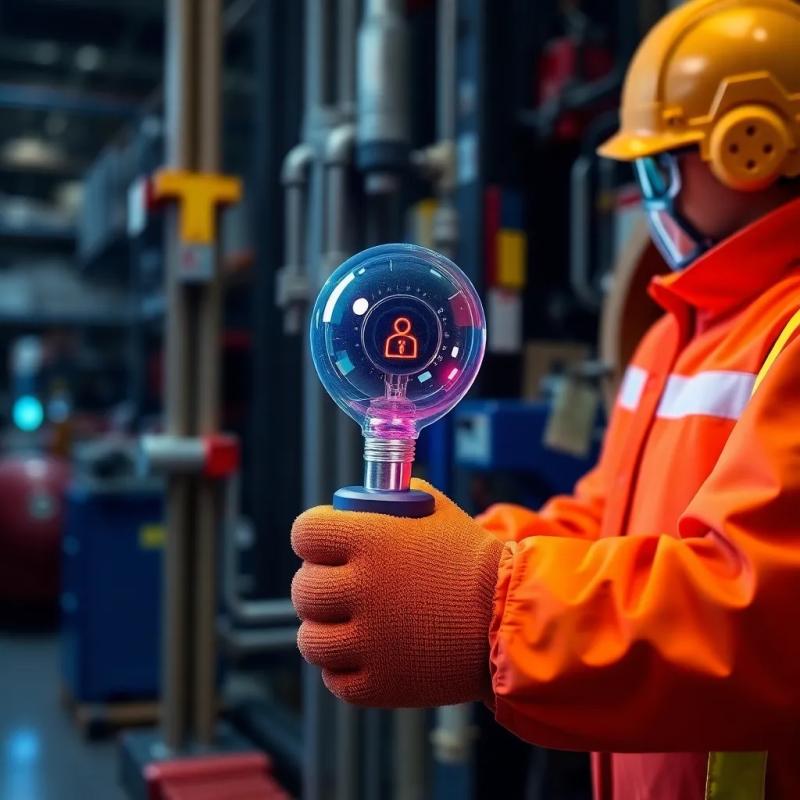
As industries continue to evolve in the digital age, the demand for cutting-edge industrial equipment and tools has never been higher. From advanced robotics to precision machinery, new technologies are reshaping the manufacturing landscape. This transformation is being driven by the need for greater efficiency, precision, and sustainability, with the global industrial equipment market expected to reach $934 billion by 2028, according to Fortune Business Insights.
In 2024, key trends are emerging that will define the future of industrial tools and equipment, marking a shift towards smarter, greener, and more connected solutions. This article takes a deep dive into these trends and the role they will play in revolutionizing manufacturing, construction, and other industrial sectors.
The Growing Demand for Automation and Robotics
One of the most significant trends driving the future of industrial equipment is automation. As industries aim to reduce labor costs and increase productivity, robots and automated machinery are taking center stage. According to the International Federation of Robotics (IFR), global sales of industrial robots reached 384,000 units in 2022, a figure that is expected to climb steadily in the coming years.
Automated equipment such as CNC (Computer Numerical Control) machines and robotic arms are now commonplace in sectors like automotive manufacturing, electronics, and heavy industries. These machines offer unparalleled precision, allowing for the creation of intricate parts and components with minimal human intervention. This not only reduces errors but also significantly cuts down on production time, enabling companies to meet the rising demand for mass customization.
A 2023 report from McKinsey & Company predicts that by 2030, up to 50% of tasks in manufacturing could be automated, driving efficiency while reducing operational costs.
The Role of Advanced Cutting Tools in Precision Manufacturing
Precision has always been a cornerstone of industrial manufacturing, and advanced cutting tools are playing a pivotal role in achieving this. Whether it’s producing parts for aerospace, automotive, or medical industries, manufacturers rely on high-performance cutting tools like carbide inserts, diamond-tipped drills, and laser cutting machines to meet exacting specifications.
According to a study published in the Journal of Manufacturing Processes, the global market for precision cutting tools is set to grow at a compound annual growth rate (CAGR) of 7.1% between 2022 and 2028. Companies are investing in next-generation tools that offer greater durability and faster cutting speeds. Innovations such as cryogenic cooling, which uses liquid nitrogen to reduce tool wear, are enabling manufacturers to push the limits of speed and accuracy while minimizing waste.
Moreover, new developments in 3D printing technology are providing additional layers of customization in tool production. Engineers can now design and manufacture specialized cutting tools tailored to the specific needs of a project, further enhancing efficiency and reducing material waste.
The Rise of Smart Equipment: Data-Driven Manufacturing
As industries embrace Industry 4.0, data is becoming an integral part of how machines operate. Smart industrial equipment, equipped with sensors and connected to the Internet of Things (IoT), is enabling real-time monitoring and optimization of production processes. These tools can collect data on factors like temperature, vibration, and pressure, helping operators detect potential issues before they cause downtime.
A 2023 report by Deloitte highlights that predictive maintenance, made possible by IoT and AI, can reduce machine downtime by 30% and extend the lifespan of equipment by 20%. By analyzing data trends, manufacturers can predict when a machine is likely to fail and schedule maintenance accordingly, saving both time and money.
Smart tools are also making it easier to track inventory, manage energy usage, and improve overall plant efficiency. Digital twins—virtual models of physical equipment—are becoming an essential part of industrial operations. By simulating the performance of machines in real time, companies can optimize production schedules and improve output without disrupting the actual machinery.
Sustainability in Industrial Equipment: A Green Revolution
As environmental concerns become more pressing, industries are under pressure to reduce their carbon footprint and embrace sustainable practices. This is leading to a significant shift in the design and use of industrial equipment, with a focus on energy efficiency and waste reduction.
Electric and hybrid-powered machinery are gradually replacing traditional fuel-powered equipment. According to the International Energy Agency (IEA), the global energy efficiency market in industry is projected to grow by 9% annually through 2025, as more companies invest in energy-efficient solutions. Equipment such as electric forklifts, battery-powered tools, and solar-powered generators are becoming more popular in manufacturing plants and construction sites.
Additionally, manufacturers are incorporating recyclable and biodegradable materials into their tools, as well as adopting circular manufacturing processes. This includes refurbishing old equipment and reusing parts, a trend expected to reduce overall equipment costs by 15% by 2025, according to Accenture.
Collaborative Robotics: Enhancing Human-Machine Interaction
While automation is reducing the need for manual labor, the rise of collaborative robots—also known as cobots—shows that machines and humans can work together in harmony. Cobots are designed to assist human workers in tasks that require both precision and dexterity. These robots are equipped with sensors to ensure safety, enabling them to work alongside humans without barriers.
A report by MarketsandMarkets projects that the global collaborative robot market will reach $12.3 billion by 2027, growing at a CAGR of 41%. Cobots are increasingly used in applications such as assembly, packaging, and machine tending, where their ability to perform repetitive tasks frees up human workers to focus on more complex, creative aspects of production.
By combining human flexibility with robotic precision, companies can enhance their productivity and minimize workplace accidents. In sectors like healthcare, cobots are being used for delicate tasks like surgery, while in the automotive industry, they assist in the assembly of intricate components.
Key Challenges: Cost, Training, and Cybersecurity
Despite the many benefits of advanced industrial equipment, there are challenges to widespread adoption. The high upfront costs of robotics, automation, and smart tools can be prohibitive for small and medium-sized enterprises (SMEs). Additionally, integrating these technologies requires a skilled workforce capable of operating and maintaining them.
According to a 2023 survey by the World Economic Forum, 40% of manufacturing companies cited a lack of skilled workers as a major barrier to adopting new industrial technologies. This highlights the need for training programs and educational initiatives to equip workers with the necessary skills to operate advanced machinery.
Cybersecurity is another pressing concern as industrial equipment becomes increasingly connected. Smart tools and IoT devices are vulnerable to cyber-attacks, potentially disrupting production and compromising sensitive data. A report by Cybersecurity Ventures estimates that cybercrime will cost manufacturers over $6 trillion globally by 2025, underscoring the need for robust cybersecurity measures to protect industrial assets.
Conclusion: The Future is Smarter, Faster, and Greener
The future of industrial equipment and tools is being shaped by technological innovation and the need for sustainability. Automation, precision tools, and smart equipment are revolutionizing the way industries operate, offering new levels of efficiency and accuracy. At the same time, the rise of collaborative robots and data-driven manufacturing is enhancing the synergy between humans and machines.
Comments