How the Rolling Mill Rolls Angle Steel?
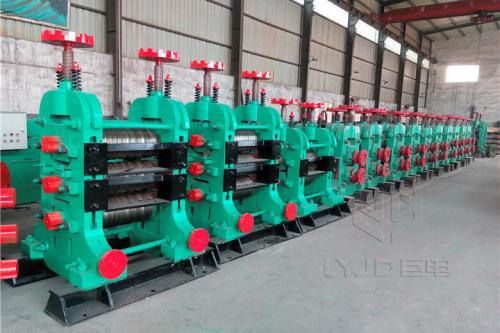
As a common
building material, hot-rolled angle steel is widely used in various industries.
It has good mechanical properties and toughness and can withstand complex
mechanical environments. So, what is the manufacturing process of hot-rolled
angle steel? Let’s learn more about it below.
The
manufacturing process of hot-rolled angle steel mainly includes raw material
processing, hot rolling, cold rolling, cutting, and heat treatment. Below,
these processes will be explained one by one.
Raw Material Processing
Raw material
processing is the first step in the hot-rolled angle steel manufacturing
process. Generally speaking, the raw materials of hot-rolled angle steel are
mainly hot-rolled plates and billets. First, the raw materials are sawed into
blocks of a certain length and width. Next, the blocks are subjected to a heat
treatment to bring them to a certain temperature. Doing so improves the
plasticity of the steel, making subsequent rolling operations smoother.
Hot Rolled
Hot rolling is
the core link in the manufacturing process of hot-rolled angle steel. The
heat-treated steel billet is fed into the hot rolling mill for rolling. The
whole process is mainly divided into two stages: rough rolling and finish
rolling. Rough rolling is mainly to compress the steel billet to a certain
thickness in preparation for entering the next stage of finishing rolling.
Finish rolling is to further suppress the steel billet to reach the required
standard size. During the hot rolling process, the billet experiences constant
pressure and friction, causing the shape and size of the billet to change.
Cold Rolled
Cold rolling is
a complementary link in the manufacturing process of hot-rolled angle steel.
During the hot rolling process, due to the continuous high temperature and
pressure, the internal structure of the steel will change, forming certain
grains and defects. Through cold rolling, the internal structure of the steel
can be rearranged and adjusted, thereby improving the strength and hardness of the
steel. In addition, cold rolling can also improve the surface finish and
dimensional accuracy of steel, making the steel more suitable for various
process requirements.
Cutting
Cutting is one
of the subsequent processing steps in the hot-rolled angle steel manufacturing
process. During the hot and cold rolling processes, steel billets are pressed
into angles of different shapes and sizes. In practical applications, it is
often necessary to cut to a specific length. Therefore, it is very necessary to
cut the steel. The cutting method can be selected according to specific
requirements. Common methods include flame cutting, plasma cutting, and
mechanical cutting.
Heat Treatment
Heat treatment
is the final step in the manufacturing process of hot rolled angle steel.
During the hot rolling and cold rolling processes, the internal structure and
properties of steel will change due to the effects of temperature and pressure.
To further adjust and improve the properties of steel, it needs to be heat
treated. Heat treatment methods mainly include normalizing treatment, quenching
treatment, tempering treatment, etc. Through heat treatment, the hardness,
toughness, and strength of steel can be improved, making it more suitable for
various application scenarios.
In short, the
manufacturing process of hot-rolled angle steel is complex and delicate.
Through raw material processing, hot rolling, cold rolling, cutting, and heat
treatment, hot-rolled angle steel products that meet various standards and
requirements can be produced. Hot-rolled angle steel provides strong and
reliable building materials for various industries with its excellent
performance and wide range of applications.
Comments