How to Select the Right Continuous Casting Machine Radius for Your Steel Production Process?
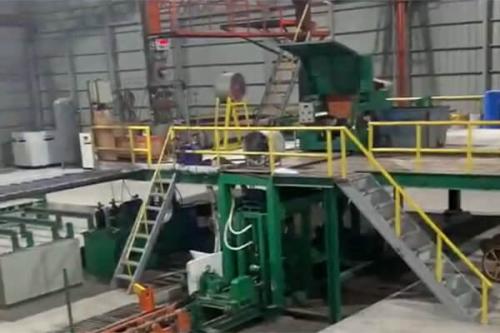
Selecting the
right continuous casting machine radius is crucial to ensure efficient and
high-quality steel production. The radius of the machine plays a significant
role in controlling various aspects of the casting process, including heat
transfer, solidification, and the formation of defects. Here are some key
considerations to help you in selecting the appropriate continuous casting
machine radius for your steel production process.
Understand the Process
Requirements
Begin by
thoroughly understanding the specific requirements of your steel production
process. Factors such as the type of steel being cast, the desired product
dimensions, and the required quality standards will influence the choice of
machine radius.
Evaluate Casting Speed
The casting
speed directly impacts the solidification behavior and heat transfer in the
continuous casting process. Higher casting speeds typically require smaller
machine radii to maintain adequate cooling and solidification rates. Consider
the desired casting speed and its compatibility with different machine radius
options.
Consider Steel Grades and
Sizes
Different steel
grades and product sizes have varying solidification characteristics. Some may
require faster cooling rates to prevent defects, while others may benefit from
slower cooling for improved microstructure control. Evaluate the steel grades
and sizes you typically produce and choose a radius that facilitates the
desired solidification behavior.
Analyze Defect Formation
Defect
formation, such as cracks, segregation, or surface irregularities, can be
influenced by the machine radius. Analyze the common defects encountered in
your steel production process and assess how different machine radii can
mitigate or exacerbate these issues.
Consult with Experts
Seek advice
from experts in the field of continuous casting. Discuss your specific
requirements and challenges with engineers, metallurgists, and equipment
manufacturers who have experience in continuous casting technology. They can
provide valuable insights and recommendations based on their expertise.
Conduct Modeling and
Simulation
Utilize
computer modeling and simulation tools to simulate the continuous casting
process with different machine radii. Virtual simulations can help predict the
solidification behavior, temperature distribution, and defect formation, aiding
in the selection of the optimal radius.
Consider Equipment
Limitations
Take into
account the practical limitations of your existing continuous casting
equipment. The design and capabilities of your casting machine may impose
restrictions on the range of machine radii available. Ensure that the chosen
radius is compatible with your equipment and can be implemented effectively.
Evaluate Cost and Efficiency
Assess the cost
implications associated with different machine radii options. Consider the
investment required for modifying or replacing the casting machine, as well as
the potential impact on production efficiency, energy consumption, and
maintenance costs.
Learn from Industry Best
Practices
Study
successful case studies and industry best practices related to continuous
casting machine radius selection. Understand how other steel producers have
optimized their casting processes by choosing the right radius and adapting
those learnings to your specific requirements.
Continuous Monitoring and
Optimization
Once the
machine radius is selected, continuously monitor and analyze the performance of
your casting process. Regularly evaluate the quality of the produced steel,
track defect rates, and gather feedback from operators and technicians. This
feedback loop will help you fine-tune and optimize the machine radius over
time.
Remember that
selecting the right continuous casting machine radius is a complex task that
requires careful analysis, experimentation, and expertise. By considering the
process requirements, solidification behavior, defect formation, and expert
advice, you can make an informed decision that enhances the efficiency and
quality of your steel production process.
Comments