About Aluminum Ingot Casting Line, All You Want to Know Are Here
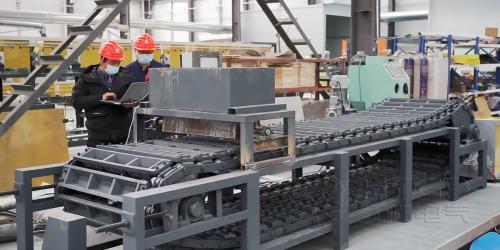
The aluminum
ingot casting line is a production line equipment used to produce aluminum
ingots.
Aluminum Ingot Casting Line
Composition
Aluminum
melting furnace: used to melt aluminum raw materials into liquid aluminum.
Ingot casting
machine: The ingot casting machine is the core equipment in the aluminum ingot
casting production line. It includes a mechanical frame, aluminum liquid
distribution system, cooling system, demoulding system, transmission system,
mold, and other components. The molten aluminum is evenly injected into the mold
through the molten aluminum distribution system while ensuring the depth of
the molten aluminum casting.
Mold: The mold
is used to shape aluminum ingots and is generally made of high-temperature-resistant alloy steel.
Cooling
equipment: used to cool the cast aluminum ingots.
Handling
equipment: used to carry cooled aluminum ingots from the casting line.
Other auxiliary
equipment: Depending on production needs, it may also include automatic ingot
casting machines, automatic ingot stacking machines, environmental protection
equipment, forklifts, spectrum analyzers, floor scales, refiners, and other
equipment.
How should the aluminum ingot casting line's melting furnace and ingot casting machine be
configured?
In the aluminum
ingot casting line, the configuration of the melting furnace and ingot casting
machine can be determined according to actual production needs and production
scale.
Generally
speaking, the number and capacity of melting furnaces are determined based on
the production capacity of the aluminum ingot casting line and the demand for
molten aluminum. At the same time, to ensure the stability and quality
of molten aluminum, more than one melting furnace is usually configured.
The
configuration of the ingot casting machine should also be determined based on
actual production needs. Depending on the specifications and quantity of
aluminum ingots to be cast, one or more ingot casting machines can be
configured. When configuring an ingot casting machine, factors such as its
production capacity, stability, reliability, and maintenance convenience need
to be considered.
In addition, to ensure continuous production of the aluminum ingot casting line and
improve production efficiency, the distance and height between the melting
furnace and the ingot casting machine must also be reasonably designed and
controlled. Generally speaking, the height difference between the melting
furnace and the ingot casting machine should not be too large to avoid
temperature loss and oxidation while transporting molten aluminum.
How to determine the number
of molds for the aluminum ingot casting line?
In an aluminum
ingot casting line, the number of molds depends on many factors, including the
specifications of the aluminum ingot, casting speed, production cycle, etc.
Generally speaking, the greater the number of molds, the higher the production
efficiency, but the corresponding cost will also increase. Therefore,
determining the number of molds requires comprehensive consideration of
multiple factors.
First, the
number of molds must be determined based on the specifications and shape of the
aluminum ingot. If aluminum ingots of different specifications and shapes need
to be produced, molds of different specifications and shapes need to be
configured accordingly.
Secondly, the
casting speed and production cycle should be considered. If higher casting
speed and shorter delivery time are required, the number of molds needs to be
increased to speed up production.
In addition,
equipment limitations and maintenance needs must be considered. If the size of
the equipment is small or maintenance is inconvenient, the number of molds
needs to be reduced accordingly to avoid equipment failure and maintenance
difficulties.
Summary
Aluminum ingot
casting lines have a wide range of applications, including but not limited to
automobile, construction, electronics, aerospace, shipbuilding, and other
industries. At the same time, with the continuous advancement of technology and
the continuous expansion of application requirements, the application prospects
of aluminum ingot casting lines are also extensive.
Comments