What Is an Aluminum Ingot Casting Machine?
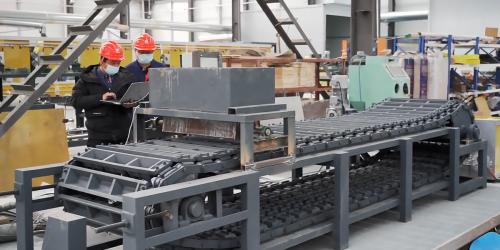
An aluminum ingot casting machine is a device used to produce aluminum ingots through the casting process. It typically consists of several components and operates based on specific principles. Here's a general overview of how an aluminum ingot casting machine works.
Aluminum Ingot Casting Machine Working Process
Melting: The machine starts by melting aluminum scraps or raw aluminum materials in a furnace. The furnace can be electrically powered or fueled by gas or oil, depending on the design.
Degassing and Fluxing: Once the aluminum is melted, the machine may include a degassing and fluxing system. Degassing removes impurities and gases from the molten aluminum, while fluxing helps to remove any remaining impurities and enhance the metal's quality.
Filtration: Filtration systems are often used to remove solid impurities and particles from molten aluminum. This helps improve the ingot's final quality by ensuring a cleaner metal composition.
Mold Preparation: The casting machine prepares the molds for the ingots. Molds can be made of steel or other materials capable of withstanding high temperatures. The molds are preheated to prevent rapid cooling of the molten aluminum when it is poured, which could cause defects in the ingot.
Pouring: The molten aluminum is poured into the prepared molds. The machine ensures precise pouring to achieve consistent ingot sizes and shapes. It may use a tilting mechanism or other methods to control the pouring process accurately.
Cooling and Solidification: After pouring, the molds with the molten aluminum are allowed to cool and solidify. The cooling process can take some time, depending on the size and thickness of the ingots.
Ingot Removal: Once the ingots have solidified, the molds are opened, and the aluminum ingots are removed. The machine may have mechanisms to facilitate the extraction of the ingots from the molds.
Finishing: The freshly cast aluminum ingots may undergo further processing, such as surface cleaning, inspection, and marking, to prepare them for storage, transportation, or subsequent manufacturing processes.
Additional Details about Aluminum Ingot Casting Machines
Machine Types: There are various types of aluminum ingot casting machines available, ranging from small-scale manual machines to large-scale automated systems. The choice of machine depends on the desired production capacity, automation level, and other specific requirements.
Crucible Furnace: The furnace used in the casting machine often employs a crucible, which is a container made of refractory material capable of withstanding high temperatures. The crucible holds the molten aluminum and keeps it heated during the casting process.
Continuous Casting: In some cases, aluminum ingot casting machines utilize a continuous casting process. This method involves a continuous flow of molten aluminum through a series of molds, resulting in a continuous production of ingots. Continuous casting machines are commonly used in high-volume production environments.
Cooling Systems: Cooling is a critical step in the casting process to solidify the molten aluminum into ingots. Cooling systems can vary, but they often involve water or air cooling methods. Water-cooled molds or spray systems are commonly used to accelerate the solidification process.
Automation and Control: Modern aluminum ingot casting machines often incorporate automation and control systems. These systems can monitor and control various parameters such as temperature, pouring speed, mold rotation, and cooling time to ensure consistent quality and efficiency.
Safety Features: Casting machines are equipped with safety features to protect operators and prevent accidents. These features may include emergency stop buttons, temperature sensors, alarms, and safety interlocks to ensure safe operation.
Scrap Recycling: Aluminum ingot casting machines can be designed to handle recycled aluminum scrap. This allows the machine to melt and cast aluminum from various sources, including post-consumer scrap, industrial waste, or excess aluminum from manufacturing processes.
Customization: Depending on specific requirements, aluminum ingot casting machines can be customized. This includes the ability to produce ingots of different sizes, shapes, and weights. Customization options are often available to cater to specific industry needs.
Quality Control: To ensure the quality of the produced ingots, casting machines may incorporate quality control measures such as spectroscopic analysis, non-destructive testing, and visual inspection systems. These measures help identify any defects, impurities, or inconsistencies in the casted ingots.
Energy Efficiency: Some casting machines incorporate energy-saving features to optimize energy consumption during the melting and casting processes. This can include efficient insulation, heat recovery systems, and advanced control algorithms to minimize energy waste.
It's important to note that specific designs and features of aluminum ingot casting machines can vary depending on the manufacturer, intended production volume, and other factors. This overview provides a general understanding of the typical process involved in casting aluminum ingots using a casting machine.
Post Your Ad Here
Comments