Why Do We Use Induction Furnace for Melting Aluminum?
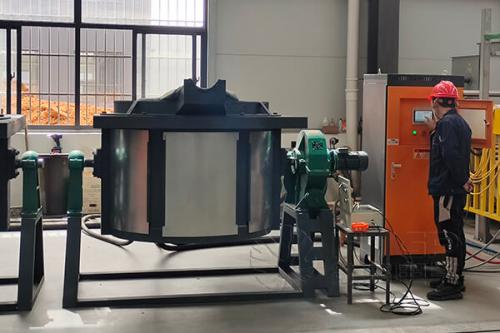
Induction melting furnaces use a process called electromagnetic
induction to melt metal. The furnace consists of an induction coil made of
copper tubing, which is wrapped around a refractory-lined crucible that holds
the metal being melted. When alternating current (AC) is passed through the
coil, it creates a rapidly changing magnetic field around the crucible. This
magnetic field induces an electric current in the metal, which generates heat
due to the resistance of the metal to the flow of electric current. This heat
then melts the metal.
An induction melting furnace is a type of furnace used for melting
metal using electromagnetic induction. The furnace consists of an induction
coil, which creates a magnetic field that induces an electric current in the
metal being melted. This electric current generates heat, which in turn melts
the metal.
Induction melting furnaces are commonly used in the metalworking
industry for melting and refining various types of metals, including iron,
steel, copper, aluminum, and brass. They are often used in foundries for
melting scrap metal, as well as in the manufacturing of castings, forgings, and
other metal products.
Induction melting furnaces offer several advantages over traditional
melting methods, including faster melting times, better temperature control,
and improved energy efficiency. They also produce fewer harmful emissions than
other types of furnaces, making them a more environmentally-friendly option.
Electric induction furnaces are commonly used to melt aluminum
because they offer several advantages over other types of furnaces.
Firstly, induction furnaces can provide very precise temperature
control, which is important for achieving the desired melting point and
maintaining consistent quality in molten aluminum. The electromagnetic field
generated by the furnace heats the metal directly and uniformly, resulting in a
more efficient heating process and reducing the risk of hot spots or cold spots
in the molten metal.
Secondly, induction furnaces are highly energy-efficient, as they
use electricity to generate the heat required to melt the metal. This can
result in lower operating costs and a smaller carbon footprint compared to
other types of furnaces that rely on fossil fuels or other energy sources.
Finally, induction furnaces can be more compact and easier to
operate than other types of furnaces, making them a popular choice for
small-scale aluminum melting operations. They are also well-suited for melting
aluminum alloys with specific chemical compositions, as precise temperature
control and uniform heating can help ensure that the desired alloy composition
is achieved.
Here are some additional details about why induction furnaces are a
popular choice for melting aluminum:
Speed: Induction furnaces can melt aluminum very quickly, with some
models capable of melting several hundred pounds of aluminum per hour. This
makes them a good choice for high-volume melting operations.
Precision: Induction furnaces can provide precise temperature
control, which is important for achieving the desired melting point and
maintaining consistent quality in molten aluminum. This precision can also help
reduce the amount of scrap produced during the melting process.
Energy efficiency: Induction furnaces are highly energy-efficient,
as they use electricity to generate the heat required to melt the metal. This
can result in lower operating costs and a smaller carbon footprint compared to
other types of furnaces that rely on fossil fuels or other energy sources.
Safety: Induction furnaces are generally considered safer than other
types of furnaces, as they do not produce open flames or emit harmful gases.
This can help reduce the risk of fires and other accidents in the workplace.
Flexibility: Induction furnaces can be used to melt a variety of
aluminum alloys, including those with specific chemical compositions or
properties. They can also be used to melt other non-ferrous metals, such as
copper, brass, and bronze.
Post Your Ad Here
Comments