Seven Methods for Energy Saving of Medium Frequency Induction Furnace
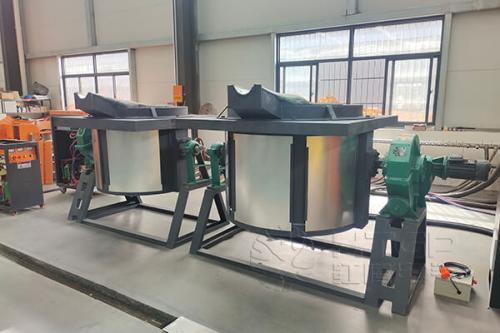
Medium frequency induction melting furnaces are widely used in the
metal smelting industry. It has the advantages of fast heating speed, high
melting efficiency, low energy consumption, and simple operation. So, what are
the ways to save energy when using a medium frequency induction melting
furnace?
The energy-saving work of the medium frequency induction melting
furnace is a systematic project, and one or two energy-saving measures alone
are not enough. System engineering requires the application of a variety of
technical measures, the organic combination of technical energy conservation
and management energy conservation, and the comprehensive control of raw materials,
equipment, processes, and management in order to achieve good energy-saving
effects. The following are several effective energy-saving measures for medium
frequency induction melting furnaces.
1. Appropriate size and thickness of furnace charge, light and thin
steel scrap can be packaged, a returned charge should be cleaned before use,
scrap steel should be descaled, all charges should be preheated, and the
ingredients should be accurate.
2. The higher the bulk density of the furnace material in the lower
part of the crucible, the better, and the heating efficiency will be improved
accordingly. The cold material should be added continuously for preheating and
avoiding the phenomenon of melting a small amount of molten iron.
3. Reasonable power supply system and front-of-furnace operation
technology. In the beginning, about 60% of the power is supplied. After the
current impact stops, the power is quickly increased to a maximum value to
accelerate the melting of the furnace charge.
4. Control the high-temperature refining and tapping temperature.
After each tapping, there should be a remaining part of the molten iron in the
furnace, which is convenient for melting and rapid melting.
5. Try to adopt the smelting operation mode of continuous operation.
6. Shorten the time of no-load auxiliary operations, such as
feeding, slag removal, temperature measurement, sampling, waiting for testing,
adjusting chemical composition, waiting for pouring, etc. The shorter the time,
the higher the production efficiency and the lower the energy consumption.
7. Pay attention to maintaining the normal operation of the
intermediate frequency power supply unit, furnace body, cooling water system,
etc., reduce the failure rate, reduce the number of furnace shutdowns in the
middle, save energy consumption, and ensure smooth production.
The above is the energy-saving method of the intermediate frequency
induction melting furnace introduced by Luoyang Hongteng. Of course, improving
the energy-saving effect of intermediate-frequency induction melting furnaces
requires the cooperation of manufacturers and users. In addition, it can be
used in conjunction with dust removal and purification equipment, focusing on
water recycling, using energy-saving raw materials, and improving energy-saving
awareness are also very critical measures.
Post Your Ad Here
Comments