How to Reduce Energy Consumption and Improve Efficiency of Rolling Mill?
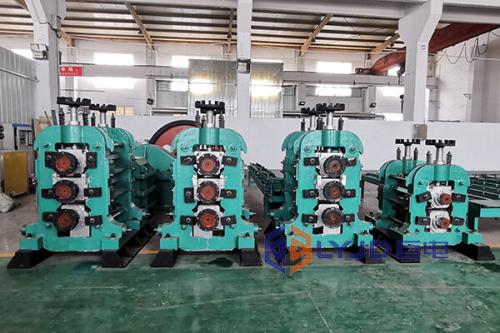
How to improve the operating efficiency of the rolling mill, reduce
the energy consumption of the rolling mill, reduce mechanical wear, and prolong
the service life of the rolling mill is very important. Various types of
rolling equipment are similar. They are heavy-duty equipment with a certain
constant torque to meet the requirements of the rolling mill for passing steel.
The high current of the rolling mill and the low efficiency of the operation
are the main reasons for the serious waste of energy consumption when the
rolling mill is working.
Generally speaking, the comprehensive energy consumption per ton of
steel in the rolling process includes three aspects: electricity consumption,
fuel consumption, and oxidation burning loss. Although there are many factors
that can affect the comprehensive energy consumption per ton of steel in the
rolling process, any factor may affect the energy consumption, but the most
important factor is the heating temperature during the production and
processing of the rolling process. Our analysis of the impact of comprehensive
energy consumption per ton of steel rolling process must first be divided from
the energy-saving links of the steel rolling process, which can be divided into
rolling mills, steel rolling heating furnaces, and some auxiliary equipment,
such as rolls, mechanical components, and other components. In addition, the
level of energy consumption structure can be mainly divided into electricity
consumption, fuel consumption, steam, energy recovery, and other related media
energy consumption. These other media energy consumption include many parts,
such as water, Oxygen, and nitrogen consumption in different degrees affect the
comprehensive energy consumption per ton of steel to a certain extent.
The rolling speed of the rolling mill is affected by many aspects
such as the rolled piece, product specification, material, etc. It is necessary
to consider the frequency conversion speed regulation of the rolling mill to
save energy. The range of the speed change is not large, and the rolling mill
may be suitable for adjusting the rolling speed. Since the motor of the rolling
mill operates in a constant voltage power supply mode, the energy consumption
of the magnetic field of the motor remains unchanged, that is, the inductive
current component remains unchanged. As the load decreases, the resistive
current component decreases. This is the reason for the low power factor of the
light load operation. When the load changes, the step-down constant power
factor power supply method is adopted for the asynchronous motor, and the
inductive current component is adjusted by adjusting the supply voltage, which
can not only reduce the iron consumption but also reduce the copper consumption
of the stator and rotor, so as to achieve the purpose of energy saving. As the
load factor decreases, the operating efficiency of the motor is gradually
improved, and the power factor increases.
Rolling mills can save energy by using inverters to adjust the speed
of motors below the base frequency. The range of energy saving is related to
the range of speed regulation. However, the range of adjustable speed of
rolling mills is limited, and the energy-saving benefits are not obvious. From
the perspective of energy-saving operation of steel rolling equipment, under
the premise of meeting the same load power, according to the power factor of
the minimum energy consumption optimization target, determine the best
adjustment voltage to reduce the input active power of the motor to improve the
operating efficiency of the rolling mill.
Post Your Ad Here
Comments