5 Aspects to Better Know Medium Frequency Induction Furnaces
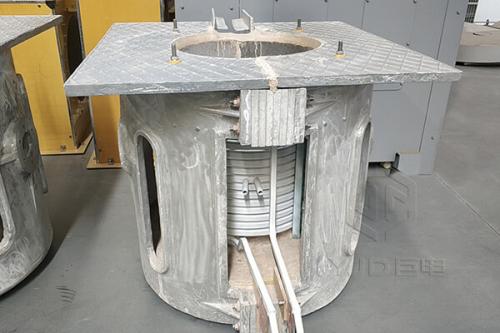
Medium frequency
induction furnaces are mainly used in metal heat treatment manufacturers such
as metal foundries and rolling mills. Because of its energy-saving and
environmental protection characteristics, it is deeply loved by manufacturers.
Below, Luoyang HTGP, a professional intermediate frequency induction furnace
manufacturer, will give you a detailed introduction to five aspects: saving,
environmental protection, heating effect, production efficiency, and
performance.
1. Energy saving:
fast heating speed, high productivity, less oxidation and decarburization,
saving materials and costs, and extending mold life
Since the
principle of intermediate frequency induction heating is electromagnetic
induction, the heat is generated in the workpiece itself. Ordinary workers can
continue to work on the forging task ten minutes after using the intermediate
frequency furnace to work, and there is no need for furnace workers to burn and
seal the furnace in advance. Thanks to the fast heating speed of this heating
method, there is less oxidation. The oxidation burning loss of intermediate
frequency heating forgings is only 0.5%, the oxidation burning loss of gas
furnace heating is 2%, and the coal-fired furnace reaches 3%. The intermediate
frequency heating process saves materials, per ton Forgings save at least 20-50
kg of steel raw materials compared with coal-fired furnaces. Its material
utilization rate can reach 95%. Because this heating method heats evenly and
the temperature difference between the core and the surface is small, it also
greatly increases the life of the forging die in forging. Gas heating saves
energy by 5% to 40%. Good heating quality can reduce scrap rate by 1.5%,
increase productivity by 10% to 30%, and prolong mold life by 10% to 15%.
2. Environmental
protection: the working environment is superior, improving the working
environment of workers and the image of the company, no pollution, low energy
consumption
Compared with
coal furnaces, medium frequency induction furnaces do not expose workers to the
baking and fumigation of coal furnaces under the scorching sun, and can meet
the requirements of various indicators of the environmental protection
department. At the same time, it establishes the company's external image and
the future development trend of the forging industry. Induction heating is an
energy-saving heating method, and the power consumption per ton of heating from
room temperature to 1100°C is less than 360°C.
3. Heating
effect: uniform heating, the small temperature difference between core and
surface, high-temperature control accuracy
Induction heating
generates heat in the workpiece itself, so the heating is uniform and the
temperature difference between the core and the surface is small. The
application of a temperature control system can realize the precise control of
temperature and improve product quality and pass rate.
4. Work
efficiency: The heating rate of the intermediate frequency electric furnace is high,
and the melting furnace iron only uses no more than 500 degrees of electricity,
and the melting is more sufficient and faster.
5. Performance:
It adopts the intermediate frequency electric furnace remote control system,
which is suitable for use in industrial environments. It has the strong
anti-interference ability and high safety. There is no wire connected between
the operating device and the controlled device, that is remote control. For all
complicated operations, press the buttons on the remote control from a long
distance. After receiving the instructions, the intermediate frequency electric
furnace can complete the corresponding operations step by step according to the
best process. Because the electric furnace is a high-voltage electrical appliance,
it is not only safer but also can avoid panic. Misoperation may cause damage to
the electric furnace.
The medium
frequency induction furnaces adopt an intelligent remote control system, which
can adjust the output power at any time. If there is a problem during
operation, such as molten steel splashing, the staff can quickly reduce the
output power to an appropriate value, and then concentrate on dealing with
impurities. When the furnace calms down, the power can be quickly increased to
the maximum. This not only saves the time of furnace workers but also saves
electricity and reduces the loss caused by molten steel splashing.
Post Your Ad Here
Comments