Function of Mold Flux in Continuous Casting Machine
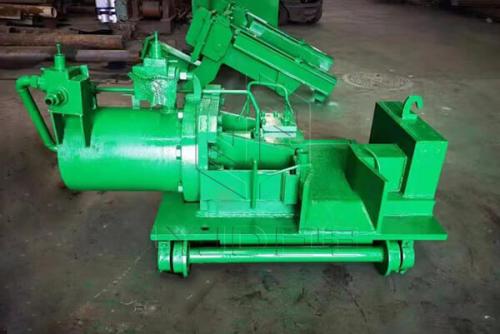
In order to adapt to the development of continuous casting technology,
continuous casting mold flux was developed in the 1960s. Continuous casting
mold flux plays an important role in the continuous casting process. In the
process of exerting its function, there are many critical stages. In each
stage, the continuous casting mold flux must play a good role, otherwise it
will reduce the surface and internal quality of the continuous casting billet.
Selecting and applying suitable continuous casting mold flux can prevent
quality defects such as longitudinal cracks on the surface of continuous
casting billets. Also, it can prevent accidents such as bonding breakouts
during continuous casting production.
Mold flux has the following five functions in the continuous casting machine:
heat insulation, anti-oxidation, absorption of non-metallic inclusions,
lubrication and improvement of heat transfer.
1. Heat insulation and heat
preservation to prevent crusting on the liquid steel surface
Add low-melting-point mold flux on the high-temperature molten steel
surface when casting. Generally, it requires the mold flux to form a three-layer
structure of liquid flux layer, sintered layer and raw flux layer. The
temperature of the three layers of mold flux is different. The temperature of
the liquid flux layer is higher, which is similar to the temperature of molten
steel. The sintering layer is about 800~900°C, and the original flux layer is
400~500°C. After adding mold flux, the heat dissipation of molten steel is 10
times smaller than that of bare molten steel, which can reduce a large amount
of heat loss and prevent crusting.
2. Isolate the air to
prevent secondary oxidation
Mold flux will quickly form a liquid flux layer under the high
temperature of molten steel. It can hinder the diffusion of air to the molten
steel surface. Utilizing the three-layer structure of mold flux to isolate
oxygen and nitrogen, the molten steel is prevented from secondary oxidation and
nitrogen absorption. It not only prevents the secondary oxidation of molten
steel, avoids the oxidation of alloy elements in molten steel, but also plays a
role to prevent molten steel from absorbing nitrogen from the air. It is
beneficial to improve the cleanliness of molten steel.
3. Absorb non-metallic
inclusions in molten steel
The mold flux is required to have a good ability to absorb molten
inclusions. It is considered that the melting speed of inclusions with low
viscosity increases, and the high alkalinity, low SiO2, Al2O3,
high Na2O, and CaF2 of liquid flux are beneficial to
increase the solubility of inclusions.
4. Lubricating effect of flux
film
The surface tension of molten steel in the crystallizer and the cooling
effect of the copper wall form an inwardly curved solidification shell, coupled
with the vibration of the mold and the capillary action of the air gap, the
liquid flux on the meniscus surface can be sucked into the gap between the
billet shell and the copper wall The air gap forms a flux film and acts as a
lubricant.
5. Improve the heat transfer
of the crystallizer
Post Your Ad Here
Comments