The Main Technological Process of Electric Furnace Steelmaking
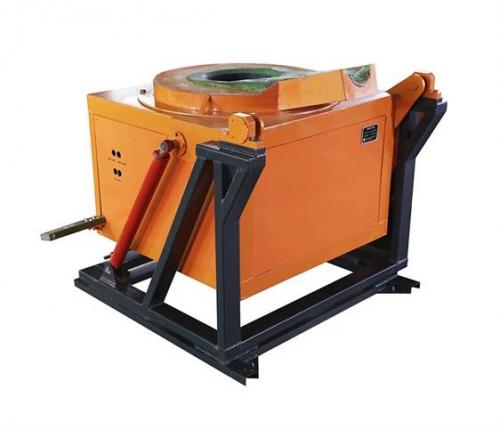
After crushing and sorting
the recycled scrap steel, it is preheated and added to the electric arc
furnace. The electric arc furnace uses electric energy as energy to melt the
scrap steel, remove impurities (such as phosphorus, sulfur) and tap the steel, and
then obtain it through secondary refining. Qualified molten steel, and then the
molten steel is solidified and formed into a billet by continuous casting, and
finally becomes a steel product through the rolling process.
Electric furnace
steelmaking is a high -temperature melting ore and metal electric furnace
generated by the electrode arc. When the gas discharge forms an arc, the energy
is very concentrated. The temperature of the arc area is above 3000 ° C. For
melting metals, the arc furnace is more flexible than other steelmaking
furnaces. It can effectively remove impurities such as sulfur and phosphorus.
The area is small, suitable for the melting of high -quality alloy steel.
Electric furnace steel is
mostly used to produce high-quality carbon structure steel, tool steel and
alloy steel. This type of steel is excellent and uniform. When the carbon
content is same, the strength and plasticity of the electric furnace steel are
better than the flat furnace steel. The electric furnace steel uses similar
steel scrap steel as the main raw material, and also uses sponge iron instead
of some scrap steel. Adjust the content of chemical ingredients and alloy elements
by adding iron alloys.
The electric furnace with
scrap steel as the raw material is less than the investment in infrastructure
than the blast furnace -to -furnace method. At the same time, due to the direct
restoration of the development, it provides most of the scrap steel for the
electric furnace. Therefore, the electric furnace steelmaking has been greatly
promoted. There are about 1,400 large electric furnaces in the world, and the
electric furnace is developing towards large, ultra -high power, and automatic
control of electronic computers. The maximum electric furnace capacity is 400
tons.
Scrap steel is the main
material of electric arc furnace steelmaking. The quality of scrap steel
directly affects the quality, cost and electric furnace productivity of steel.
Therefore, there are some requirements for scrap steel:
l The surface of the scrap steel
should be cleaned and rusty. Due to the debris such as sediment in the waste
steel, the conductive performance of the furnace material will be reduced, the
melting time will be extended, and the phosphorus effect of the oxidation
period will also affect the phosphorus effect and erosion of the lining. When
the scrap steel is severely corrosive or when it is stained with oil, it will
reduce the income from steel and alloy elements, and increase the hydrogen
content in steel.
l Waste steel must not be
mixed with non-ferrous metal, such as lead, tin, arsenic, zinc, copper and
other non -ferrous metals. The density of the lead, low melting point,
insoluble in steel liquid, easy to deposit in the gap in the bottom of the
furnace, cause leakage accidents. Tin, arsenic and copper, it is easy to cause
steel and crispy.
l Sealing containers must not
be mixed in scrap steel, flammable, explosive and poisonous to ensure safe
production.
l The chemical composition of
scrap steel should be clear, and the content of sulfur and phosphorus should
not be too high.
l The size of the scrap steel
should not be too large (the cross -sectional area should not exceed 150mm ×
150mm, and the maximum length should not exceed 350mm). The raw iron is
generally used to improve the amount of carbon distribution of the furnace in
the arc furnace steelmaking, and usually does not exceed 30%of the furnace
material.
Post Your Ad Here
Comments