How Does Continuous Casting Machine Work? How Many Types of CCM Are There?
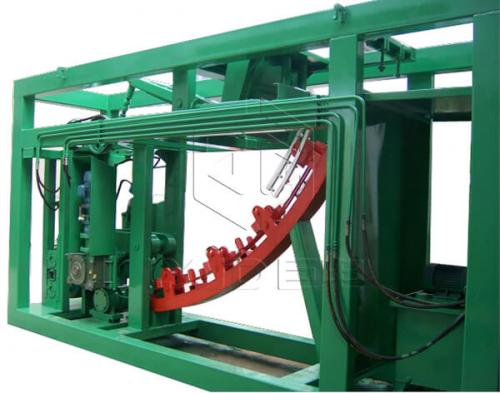
Continuous casting
machine is an equipment to produce steel billets by solidifying the liquid
steel melted from scrap steel or iron ore. Because the drive rolls can withdraw
the solid steel strand continuously from the mould at a casting speed. This speed
ensures the interface of the liquid steel and solid steel steady. Thus, the
casting process can continuously move on.
Continuous Casting Machine Work
Process
The main
components of a continuous casting machine are including a tundish, a water cooled
mould, which is made of copper, several slag covers to protect liquid steel
from exposing to air, drive rolls under the mould to withdraw the steel strands
at a certain speed, and a shear machine to cut the strand to required length.
At the
beginning, carry the liquid steel with a ladle, and flow it into the tundish.
The liquid steel will flow into the water cooled mould from the tundish. The
liquid steel will solidifies in the mould from outside to inside. Then the
drive rolls below will pull the steel strand out of the mould even the inner of
the strand is still liquid. The outside steel shell solidified now acts as a
container to hold the inner liquid until the strand fully solidifies.
For the continuous
casting machine, the first thing we should consider is what the end product is.
According the end product, the strand can be casted to bloom, billet, round,
slab, thin slab, or beam blank. Then, we should know the annual tonnage, because
it determines the capacity of ladle, the pulling speed of the drive roll.
Continuous Casting Machine Types
Continuous
casting machines can be classified in many forms. According to the structure
and shape, the continuous casting machine can be divided into vertical
continuous casting machine, vertical bending continuous casting machine, arc
continuous casting machine with straight section, arc continuous casting
machine, multi-radius elliptical continuous casting machine and horizontal
continuous casting machine. With the development of continuous casting
technology, the research on wheeled continuous casting machine, especially thin
slab continuous casting machine, has been carried out.
If classified
to the size and shape of the section cast, the continuous casting machine can
be divided into slab continuous casting machine, billet continuous casting
machine, bloom continuous casting machine, round billet continuous casting
machine, special-shaped section Continuous casters and thin slab casters. The
billet continuous casting machine also includes the rectangular billet
continuous casting machine. Usually, the casting section or the equivalent
section area is larger than 200×200mm is called the bloom, and the section or
the equivalent section area is less than 160×160mm, a rectangular blank with a
width-thickness ratio greater than 3 is called a slab.
If distinguished
by the number of strands that can be cast by the continuous casting machine
under a common ladle at the same time, it can be divided into single-strand,
double-strand or multi-strand continuous casting machines.
Continuous Casting Machine Development
Because the continuous casting machine simplifies the production process, improves the production efficiency and metal yield, saves energy consumption, greatly reduces the production cost, and has the advantages of good billet quality and other advantages. In today's steelmaking plant, whether it is long-process steelmaking or short-process steelmaking, the continuous casting machines are almost inevitable.
Comments