Guide to Fix Four Problems in PET Bottles Process
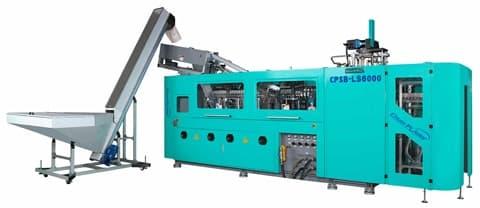
Many manufacturing industries create PET bottles as part of the products they provide to customers. The method involved is precise and ideal for achieving superior quality products. However, even stretch blow molding isn’t always perfect. Following are four of the main problems that arise and what manufacturers can do to correct them.
Four Problems With a Stretch Blow Molding Machine
1. Insufficient Top-load Strength
To reduce both resin and cost, the top-load strength of the machine used for stretch blow molding has become increasingly more important. Manufacturers go through a series of calculations to determine how stacked bottles on pallets perform during delivery. For instance, what happens when a truck goes over a bump in the road?
Since the performance of top-load almost always comes back to the thickness of the plastic wall produced by a stretch blow molding machine, as well as the overall design, a viable solution consists of moving more plastic material to the weakest part of the bottle.
2. Pearlescence and Haze
During the reheat stretch blow molding process, some bottles come out looking white or hazy. Often, overstretching the material causes this. As for pearlescence, this always occurs inside the bottle. The reason is that the interior must stretch more than the exterior. To correct this, manufacturers should allow any thin areas to cool. Then, for the area of the bottle below the thin part, they should heat it. That’ll bring additional material to the whitish portions.
When manufacturers use the two-stage reheat stretch blow molding process, they should change the settings for either the ventilation or lamp. As for PET bottles appearing hazy, this happens when the heat exceeds 240-degrees F. This causes the PET molecules to form crystals. Unlike pearlescence, haze occurs on the outside of the bottle. So, it’s important to cool this part of the PET bottle more than the inside.
3. Insufficient Rocker Bottom or Base Clearance
This is yet another problem seen with stretch blow molding. Bottles all have an inward curve on the bottom as part of the design. This allows them to sit flat on the outer rim. However, if the plastic becomes too hot following the molding process, the material begins to protrude further than the rim’s limits. That causes the bottle to rock.
This can also occur as part of the stretch blow molding process if the residual air pressure within the bottle pushes the center portion of the bottom out once the mold opens. If the machine doesn’t have cooling jets, a manufacturer needs to either increase the cooling time or lower the heat on the bottom of the bottle.
4. Drop Impact Failure
This is the fourth issue that occurs with a stretch blow molding machine. What it means is that a bottle filled with 40-degree F water can’t withstand a drop from four to five feet up, as it should. PET won’t break at its thinnest corner. The only time that occurs is when there’s haze or pearlescence present. If the drop test fails, it’s likely due to a lack of orientation.
Most notably, this happens with custom bottles with small stretch ratios. It’s also seen more often in the single-stage process rather than the two-stage method. For the single-stage reheat stretch blow molding process, adding hold or cool time will help. For the two-stage process, manufacturers should cool the preform temperature.
Turning to a Trusted Source
When you need the best stretch blow molding machine to produce quality PET bottles, contact us at PET All Manufacturing, Inc.
Comments