Major Factors behind Lockout Tagout Accidents
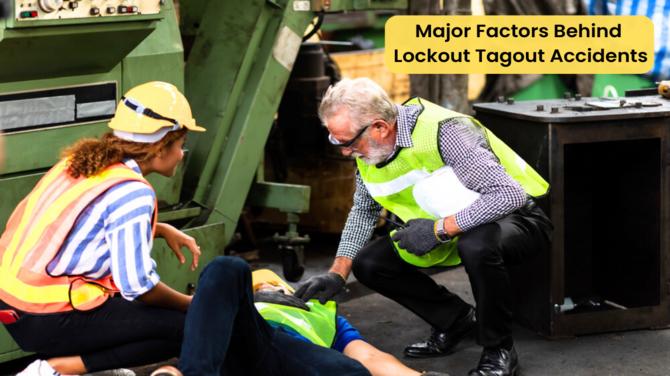
E-Square has always been the top most industry serving its customers, keeping in mind the safety and wellbeing of each and every employee at the workplace. We are the pioneers and innovators who understand the prerequisite of every industry, and provide them with the finest Lockout Tagout products for their Energy Isolation needs.
Being professionals and EHS workers for the past 22 years, we are working hard and trying our best to become the strength of companies and their employees aiming for Zero-accident workplace. After detailed study and research, our experts have concluded that the causes that lead to fatal accidents during maintenance or servicing, can be avoided if proper care is taken. So, we need to know and understand them in order to safeguard ourselves.
Although, the causes are incalculable, because the reasons are many…. There are some major reasons illustrated, that lead to destructive accidents and injuries during maintenance, due to our negligence and obliviousness. They are:
1. Lack of Awareness of LOTO at administrative and operative level
To implement a successful and working Lockout Tagout Program, it is important to have awareness about the importance of LOTO. Lack of knowledge and negligence on the employer’s part lead to uncalled eventualities. It is the responsibility of the Top-Management to generate awareness about the importance of proper Lockout Tagout, in all its employees including the temporary ones and contractors.
2. Failure to Lockout different types of Dangerous Energies
Maximum risk for most industries, including the top-class companies occur, when they fail to lockout all different kinds of Hazardous energies, leading to serious injury or death of workers. The biggest mistake the organisations make is considering only the electrical energy as the hazard, and rest of the energies are not taken seriously. Thus, failure to identify and isolate all types of Hazardous Energies, lead to fatalities and accidents.
3. Overlook the importance of disconnecting the machine from power source:
Many serious accidents have happened when someone thought a machine was safely shut off. This is an act of negligence that leads to calamities. It is not enough to just ‘shut them off’ by the control circuit and make repairs, as the machine is still energized. According to OSHA, machines need to have power circuits isolated and be locked & tagged, prior to servicing or maintenance.
4. Failure to Release stored energy
Sometimes, during the maintenance process also the stored energy builds up to a dangerous level. Turning the power off or removing the energy source doesn’t guarantee that the equipment is safe. If workers do not relieve the stored energies like chemicals, liquids, vapors, springs, elevated parts, etc. then their sudden release could cause serious injury. Also care should be taken that stored energy does not build up to a dangerous level until the entire maintenance process is completed.
5. Failure to Verify isolation & Zero energy state
Verification of isolation and ZERO Energy State is must before beginning any maintenance. Many times, workers make mistakes of not verifying the Isolation assuming that Zero energy state has been achieved. The step of verifying is as important as Lockout and Tagout. That is why it is known as LOTOTO - Lockout, Tagout & Tryout or LOTOV - Lockout, Tagout and Verify.
6. Failure to develop Machine/Equipment Specific procedures
While performing LOTO, risks are high as multiple energies are involved. Skipping even one step while performing Lockout Tagout can lead to fatality. When a workplace does not have proper MSP, such mistakes do take place. Therefore, it is most important to have an updated Machine specific procedure for each machine.
7. Sudden start up of machines
Even if an employee shuts down the equipment before performing maintenance, someone else might restart the machine unknowingly. This leads to accidental restarting of the machine. Communication gap amongst the workers or lack of systematic LOTO Procedures, leads to serious injuries at the workplace.
8. Lack of LOTO program, periodic training and audit in a plant
An effective Lockout tagout program goes beyond the locks, tags and devices. In fact, the majority of citations are a result of lack of proper lockout procedures, program documentation, periodic inspections, lockouttagout training or any other procedural element. To avoid injuries and fatalities, one must have an effective LOTO Program.
The causes that lead to accidents are many. One needs to stay attentive and alert and not overconfident when performing, even their regular task. Lockout Tagout is a must even if the work is repetitive or needs only a few minutes to get it done.
Seek help of LOTO professionals at E-Square to make your journey of systematic LOTO Implementation Seamless, Organized and Time bound.
Comments