The Benefits of Lean Manufacturing Consulting for Streamlining Operations
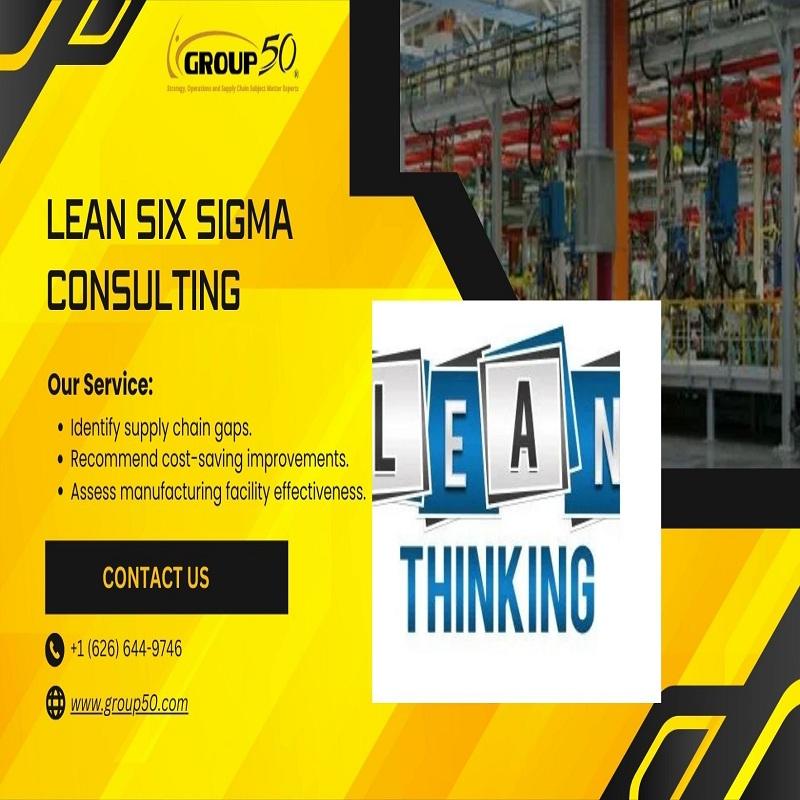
Lean manufacturing is a production philosophy and methodology aimed at reducing waste, improving efficiency, and maximizing value for the customer. It focuses on creating more value with fewer resources by streamlining processes, eliminating non-value-added activities, and enhancing quality. The goal is to deliver products or services faster, with less cost, and with higher quality, all while meeting customer demands. Lean manufacturing consulting company can help an organization develop customized strategies to improve efficiency, reduce costs, and enhance product quality.
Lean manufacturing consultants of specialist firms like Group50 can help an organization reduce waste with specialist services in areas like:
Process Assessment and Value Stream Mapping
Waste Elimination (Muda)
Continuous Improvement (Kaizen)
Just-in-Time (JIT) Implementation
Performance Metrics and Monitoring
Problem Solving and Root Cause Analysis, and more
The specialists at Group50 lean manufacturing consulting firm work with organizations to make them more efficient and effective by minimizing waste in the following 8 areas:
Transportation and movement
Inventory
Motion
Waiting
Overproduction
Over-Processing of components
Defects in products, services and business processes
Human resource
Value Stream Mapping
These 8 categories of effort can be applied anywhere in a business, but manufacturing, distribution and supply chains who focus on these areas of waste have the lowest cost, shortest lead times, highest quality and highly skilled people. It requires utilizing the proper tools and methodologies for identifying the areas of waste inside a company that will generate the maximum ROI by addressing strategic and operating gaps. Group50’s lean manufacturing consultants utilize tools such as Value Stream Mapping, Financial Modeling, Spaghetti Diagrams, Workflow analysis, Supply Chain Modeling, Six Sigma Tools and techniques such as the DMAIC process, and many others to identify and root out wasted effort.
Lean Six Sigma manufacturing consulting
Comments