Why Is Maintenance Crucial for Conveyor Belts? Learn More
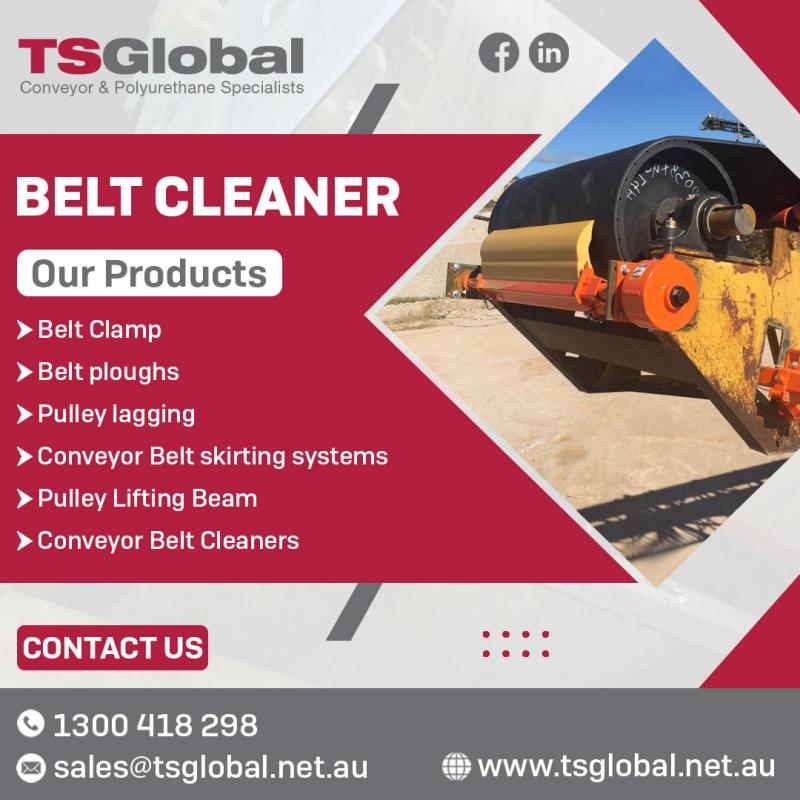
Conveyor belts are the backbone of industries such as manufacturing,
logistics, mining, and food processing. These systems are essential for moving
materials efficiently, reducing manual labor, and boosting productivity.
However, like any mechanical system, conveyor belts require regular maintenance
to ensure optimal performance and longevity. Neglecting this crucial task can
lead to unexpected downtime, increased costs, and even safety hazards. Let’s
dive into the reasons why maintenance is vital for conveyor belts and explore
best practices for keeping them in top condition.
1. Maximizing Operational Efficiency
A well-maintained Conveyor
Belt Scraper operates smoothly, ensuring consistent and reliable
material handling. Maintenance prevents issues like misalignment, slippage, or
uneven tension, which can disrupt the workflow. When a conveyor belt runs
efficiently, it minimizes production delays and enhances overall productivity.
In industries where time is money, ensuring uninterrupted operations can
significantly impact profitability.
2. Preventing Costly Downtime
Unplanned downtime can be a nightmare for any business. A conveyor belt
breakdown not only halts operations but can also lead to financial losses.
Regular inspections and preventive maintenance help identify potential issues
before they escalate into major problems. By addressing minor wear and tear
early, businesses can avoid costly repairs or complete system replacements.
3. Extending Equipment Lifespan
Conveyor belts are a significant investment, and their longevity depends on
proper care. Regular maintenance helps extend the lifespan of both the belt and
its components, such as rollers, pulleys, and motors. Cleaning, lubricating,
and adjusting these parts reduces stress on the system, preventing premature
wear. Over time, this translates into cost savings and a higher return on
investment.
4. Enhancing Workplace Safety
Faulty conveyor belts pose serious safety risks. A misaligned belt, worn-out
rollers, or improper tensioning can lead to accidents, such as materials
spilling or the belt snapping. Regular maintenance ensures that all components
are in proper working condition, reducing the likelihood of workplace injuries.
Additionally, maintenance procedures often include checks for emergency stops
and safety mechanisms, further safeguarding employees.
5. Ensuring Product Quality
In industries like food processing or pharmaceuticals, product contamination
is a major concern. A poorly maintained Conveyor
Belt Cleaner can accumulate dirt, grease, or debris, compromising
product quality. Regular cleaning and maintenance ensure hygienic conditions
and compliance with industry standards. Even in non-food industries, a clean
and well-functioning conveyor belt minimizes damage to goods, preserving their
quality.
6. Energy Efficiency
Conveyor belts that are not properly maintained often consume more energy
than necessary. Issues like misalignment or excessive friction can cause motors
to work harder, leading to higher energy costs. Regular maintenance ensures
that the system operates at peak efficiency, reducing energy consumption and the
associated environmental impact.
Best Practices for Conveyor Belt Maintenance
To reap the benefits of regular maintenance, it’s essential to follow a
structured approach. Here are some best practices:
1. Conduct Routine Inspections
Schedule regular visual inspections to identify signs of wear, misalignment,
or damage. Look for issues like frayed edges, loose fasteners, or unusual
noises during operation.
2. Clean the Belt and Components
Dust, debris, and spills can accumulate on the belt and its components,
affecting performance. Regular cleaning prevents buildup and ensures smooth
operation.
3. Check Belt Tension and Alignment
Proper tension and alignment are crucial for optimal performance.
Over-tensioning can lead to excessive wear, while under-tensioning can cause
slippage. Misaligned belts can damage both the belt and the structure.
4. Lubricate Moving Parts
Bearings, rollers, and other moving components require lubrication to
minimize friction and wear. Use appropriate lubricants and follow manufacturer
recommendations.
5. Replace Worn Parts Promptly
Don’t delay replacing worn-out or damaged components. Timely replacement
prevents minor issues from escalating into major failures.
6. Train Your Team
Ensure that maintenance staff and operators are well-trained in identifying
and addressing potential issues. Proper training can enhance the effectiveness
of your maintenance program.
Conclusion
Maintenance is not just a routine task—it’s a critical investment in the
performance, safety, and longevity of your conveyor belt system.
By conducting regular inspections, addressing wear and tear promptly, and
following best practices, businesses can prevent costly downtime, enhance
efficiency, and ensure workplace safety. A proactive approach to maintenance
not only protects your investment but also contributes to the seamless
functioning of your operations. Remember, a well-maintained conveyor belt is
the key to a productive and profitable operation.
Post Your Ad Here
Comments