Exploring Forging options: How open die and closed die affect automotive production?
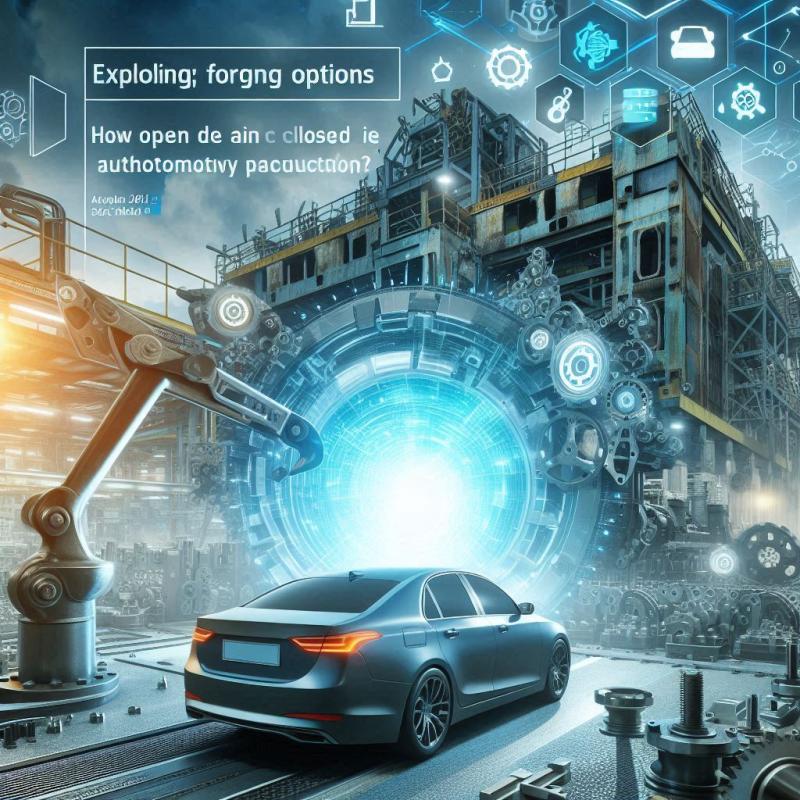
Forging is a manufacturing process where the metal is shaped under high pressure, using compressive forces to form automotive parts with robust strength and durability. The process is done by pressing, hammering or rolling of metal into a desired shape. The process refines the grain structure of metal, improving its mechanical properties, such as toughness and resistance to fatigue making it ideal for automotive industries.
What are the two types of forgings using in automotive production?
The two main types of forgings used in the automotive industry are the open die forging and closed die forging. Open die forging involves shaping of metals between flat or shaped dies without enclosing the material, making it ideal for large, simple components like axles and shafts.
The method provides great strength and durability for heavy-duty applications. Closed die forging compresses the metal within a pre-shaped cavity to produce complicated and precise parts like gears, engine components and connecting rods. The closed die forging is highly efficient for mass production, ensuring tight tolerances and less material waste.
All about open die forging in Automotive Industry-
Open die forging is also known as free forging. The metal is not confined in a cavity, allowing it to be worked in multiple directions. The method is used to create large, simple shapes such as rods, bars and rings.
What are the benefits of open die forging in automotive industry?
Open die components are long-lasting because of the excellent grain flow, making them robust and resistant to fatigue, which is important for automotive parts like axles and shafts. The process is perfect for producing bulky parts used in trucks, buses or off-road vehicles. Also, open die forging is best suited for specialized parts due to lack of expensive tooling needs.
What are the limitations of open die forging?
It is challenging to achieve tight tolerance in open die forging as it required additional machining. The process is not suitable for complex and high-volume parts.
Open die forging is used for manufacturing large and small parts like axles and shafts.
All about Closed Forging in Automotive Industry-
Closed die forging is also known as impression die forging, involves compressing the metal work piece within the set of dies that contain a pre-designed cavity. The closed die forging produces components with intricate shapes and precise dimensions.
What are the benefits of closed die forging in automotive production?
Closed die forging is perfect for mass production, perfect for manufacturing high-volume parts like connecting rods, gears and more. There is less waste because of accurate shaping, thus reducing the material costs. The uniform grain structure boosts the strength and durability, important for safety of critical parts. The closed die forging allows for lightweight component designs, improving fuel efficiency in vehicles.
What are the limitations of closed die forging?
High investment goes in making dies, making closed die forging less suitable for low volume production. There are size constraints and close die forging can be used only on the components that best fit within the die size.
Closed die forging is used for manufacturing intricate and high-volume parts like gears.
Open Die v/s Closed die forging – Choosing the right forging method
When choosing between Open Die v/s closed Die forging in automotive industry; there are varied factors to be considered. The factors include –
- Size of the automotive parts: Open die forging is suitable for large, heavy-duty parts and closed die forging is perfect for smaller and precision automotive components.
- Part Complexities: Closed die forging is perfect in producing complex shapes, whereas open die forging is better for simpler geometrics.
- Production Volume: Open die forging is cost-effective for low production and closed die forging is more efficient for high-volume manufacturing.
- Tooling costs: Open die forging has less tooling costs and closed die forging needs significant upfront investment in dies.
The Future of Forging in Automotive Manufacturing
The forging industry continues to be the pillar of automotive manufacturing. As the automotive sector evolves, because of technological advancements and eco-friendly goals, forging is set to play a key role in shaping the vehicles of tomorrow.
- Emerging trends in forging technology: Integration of the cutting-edge forging technologies like automation, artificial intelligence and data analytics is revolutionizing forging process. The smart forging systems use real-time data to optimize pressure, material flow and temperature, improving precision and minimizing waste. The advancements boost the quality of forged parts while minimizing production costs.
- Role of Forging in Electric Vehicles: One of the most significant trends shaping the future of forging is shift towards electric vehicles to reduce carbon emissions and save fuel. Forging process are changing to work with lightweight materials like high-strength alloys and aluminum, enabling the production of lightweight and long-lasting components such as suspension parts and motor housings.
- Sustainability: Environmental concerns grow and forging industry is embracing sustainable practices. Manufacturers are adopting sustainable processes and recycling scrap materials like solar and wind power in forging manufacturing units is also gaining importance. These initiatives are according to the automotive industry’s broader push towards greener production practices.
- 3D Forging: Future forging methods will accommodate customization, meeting the demand for customization in automotive parts. Hybrid manufacturing and 3D forging in future will blend forging with additive manufacturing, creating complicated and precise parts that traditional methods cannot produce efficiently.
The future of forging in automotive industry lies greatly on its ability in adapting to the changing trends, sustainable approach and technology innovation. When choosing between open die v/s closed die Forging in automotive industry, it is important to consider the above mentioned factors and it is equally important to adopt the changing trends in forging facilities.
In a nutshell, forging will be an important pillar in an automotive industry, shaping new era of sustainable, efficient and high-performance vehicles.