Ramming Material Refractory Materials for Induction Furnaces
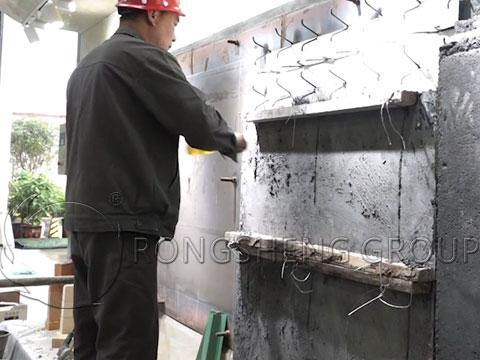
Induction furnaces require refractory ramming materials. Furnace linings for different purposes have different requirements for refractory materials. Induction furnaces can only work effectively if ramming materials that meet smelting conditions are used. Rongsheng Unshaped Refractory Material Manufacturer can provide high-quality refractory ramming materials for induction furnace linings. Contact us for free quotes.
Requirements for the Performance of Ramming Material Refractory Materials in Induction Furnaces
Refractory materials for furnace linings should meet certain conditions to cope with the harsh working environment of the furnace lining. The refractoriness of steelmaking refractory materials should be ≥1700℃, and the refractoriness of smelting cast iron refractory materials should be ≥1500℃. The refractory materials used have good high-temperature stability, strong corrosion resistance, and small difference in basicity with slag. They have certain strengths at room temperature and high temperature. They have low resistance, good insulation, and low specific resistivity. The lining materials should avoid the introduction of ferromagnetic materials that can significantly reduce the specific resistivity and insulation of the materials. The lining materials have good thermal insulation properties, and the refractory materials used should be economical and environmentally friendly.
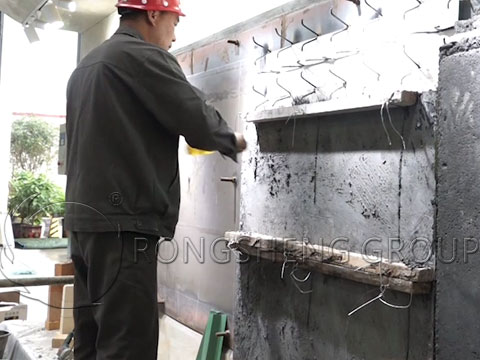
Functions of Each Component of Ramming Material
Ramming material is composed of refractory aggregate, refractory powder, additives, and other parts. Irregularly shaped aggregate particles are conducive to the interpenetration, bite and pinning between particles, which can improve the bonding strength. After sintering, refractory aggregate forms the skeleton of the material, which can improve the thermal stability and strength of the material. Refractory powder has a certain fluidity, which can fill the gaps in the material, increase the volume density of the material, and improve the construction performance. At the same time, the fine powder is more active than the aggregate particles, and can react with the additives in the material first, improve the strength of the material or improve other properties of the material. For amorphous refractory materials, the continuous particle gradation between refractory aggregate and powder has a great influence on the density of the material. It thus affects the volume density, porosity, strength and slag resistance of the material.
The function of the binder for ramming material is to bond the amorphous refractory material into a whole at room temperature or a certain temperature, with a certain shape and strength. The binder needs to have a large surface contact with the refractory aggregate and refractory powder, and at the same time, it is necessary to ensure the good volume stability of the material.
Comments