ISO 9001: Key Terminology You Should Know
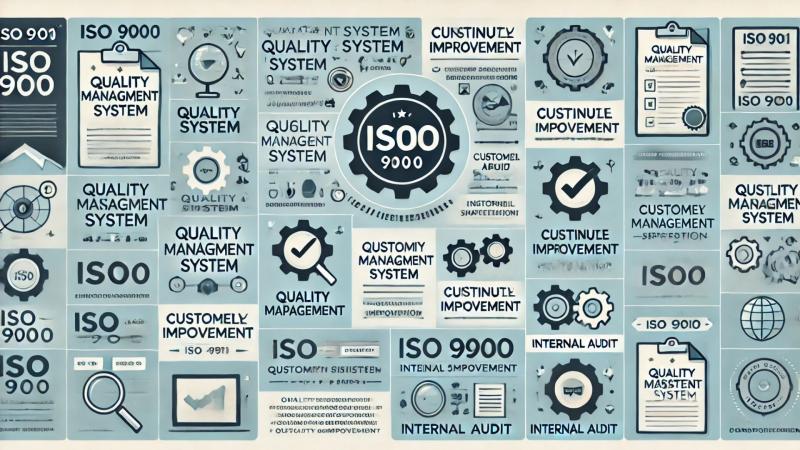
ISO 9001 is an internationally recognized standard for quality management systems (QMS), designed to help organizations consistently meet customer requirements and improve operational efficiency. The latest version, ISO 9001:2015, emphasizes risk-based thinking, leadership involvement, and a process approach to quality management. For businesses across industries, implementing ISO 9001 ensures not only compliance with customer and regulatory requirements but also fosters continual improvement. Through ISO 9001 training, organizations can equip their employees with the knowledge and skills needed to develop, implement, and maintain a robust QMS, enhancing both productivity and customer satisfaction.
Understanding Quality Management System (QMS)
A Quality Management System (QMS) is a formalized system that documents processes, procedures, and responsibilities for achieving quality objectives. The QMS framework in ISO 9001 helps businesses identify key areas for improvement, control quality risks, and ensure that customer satisfaction is always at the forefront of operations. A QMS includes elements like quality policies, objectives, process maps, and performance metrics. Implementing a QMS as per ISO 9001:2015 training enables businesses to manage their processes effectively, resulting in consistent quality outcomes. The components of a QMS work together to enhance overall efficiency and ensure that the organization is responsive to changes in customer needs or market conditions.
Key Terms Related to ISO 9001
When engaging in ISO 9001 training, it’s essential to familiarize yourself with key terms that are frequently used in the standard:
Non-conformity: This refers to a failure to meet a specific requirement or standard. Non-conformities can occur in products, processes, or documentation, and addressing them is crucial for maintaining ISO 9001 compliance.
Corrective Action: Corrective actions are steps taken to eliminate the root cause of a detected non-conformity to prevent its recurrence. It goes beyond merely fixing the immediate issue.
Preventive Action: Unlike corrective actions, preventive actions are measures taken to eliminate the causes of potential non-conformities. They are proactive steps aimed at preventing issues before they occur.
Stakeholders: In ISO 9001, stakeholders are all parties that have an interest in the performance of the organization’s QMS, such as customers, employees, suppliers, and regulatory bodies.
Audit: An audit is a systematic examination of the QMS to ensure that it meets ISO 9001 requirements. Audits can be internal, performed by the organization, or external, carried out by certification bodies.
Understanding these terms is critical for employees as they undergo ISO 9001:2015 training, ensuring that they can effectively contribute to the QMS.
Document Control and Records Management
Document control is a core component of ISO 9001, ensuring that all documented information is current, properly authorized, and easily accessible. In ISO 9001 training, organizations learn to manage key documents and records, which include policies, procedures, work instructions, and records of quality performance. Some key terms related to document control are:
Documented Information: This refers to all information that the organization uses or maintains to support the operation of its QMS. It can include electronic files, written documents, and multimedia records.
Records: Records are a special type of documented information that provide evidence of compliance with requirements. Examples include inspection records, audit results, and corrective action reports.
Versions: Version control ensures that all employees are working with the most up-to-date documents and procedures. Proper management of versions prevents the use of outdated information that may not meet ISO 9001 requirements.
Effective ISO 9001:2015 training helps employees understand how to maintain these documents and records, ensuring that all processes are transparent, traceable, and compliant with the standard.
Roles and Responsibilities
Several key roles are essential within the ISO 9001 framework, each contributing to the QMS’s success:
Management Representative: This individual is responsible for ensuring that the QMS is established, implemented, and maintained according to ISO 9001 standards. They also report on the performance of the QMS to top management.
Internal Auditor: Internal auditors play a crucial role in reviewing the QMS’s effectiveness. They perform regular internal audits to ensure compliance with ISO 9001 and identify areas for improvement.
Roles and responsibilities are clearly defined during ISO 9001 training, helping teams understand their accountability in maintaining and improving the quality management system.
Understanding Process Approach
The process approach is a fundamental concept in ISO 9001, which emphasizes managing and improving processes rather than individual tasks. This approach ensures that all activities within the organization are aligned with achieving consistent quality outcomes. During ISO 9001:2015 training, employees learn how to map and control processes, ensuring that inputs are effectively transformed into outputs that meet quality standards.
By applying the process approach, businesses can identify inefficiencies, reduce waste, and enhance overall performance. The focus is on understanding how different processes interact and contribute to the overall quality of the product or service delivered to customers.
Continuous Improvement Concepts
ISO 9001 promotes a culture of continuous improvement, encouraging organizations to constantly refine their processes and enhance quality performance. Two key concepts in this area are:
PDCA Cycle (Plan-Do-Check-Act): The PDCA cycle is a methodical process for continuous improvement. It involves planning improvements, implementing them, checking their effectiveness, and acting on the results. This cycle helps organizations refine their processes and meet evolving quality goals.
Kaizen: Kaizen is a Japanese term that means “continuous improvement.” It focuses on small, incremental changes that accumulate over time to improve overall efficiency and quality.
In ISO 9001 training, employees are introduced to these continuous improvement concepts, helping organizations foster a culture of ongoing innovation and quality enhancement.
ISO 9001:2015 training plays a crucial role in ensuring that organizations can effectively implement and maintain a quality management system. By understanding key concepts like the process approach, document control, and continuous improvement, employees can contribute to an organization’s success in achieving consistent quality outcomes and customer satisfaction. Investing in ISO 9001 training empowers businesses to enhance operational efficiency and gain a competitive edge in their industry.
Comments