Unconventional Details About Aluminum Casting for Light Automotive Components
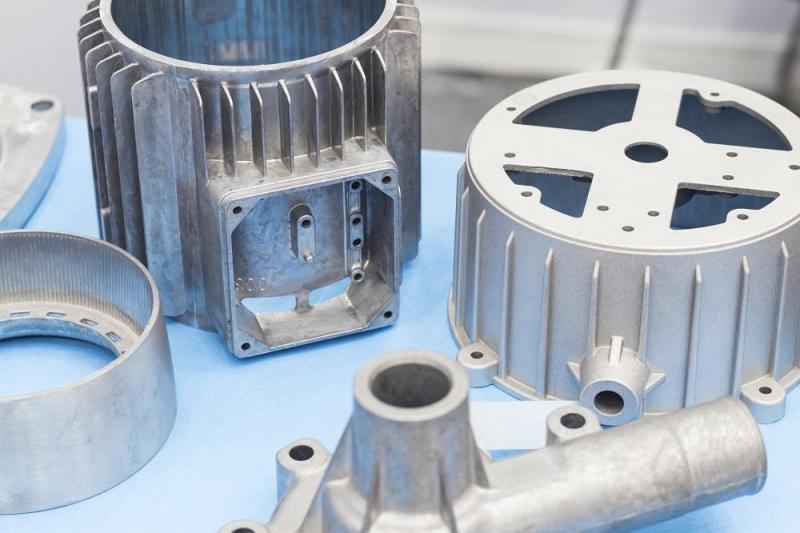
Currently, there is an increased adoption of lightweight, strong materials within the automotive industry. Such has been the culture due to the need to improve fuel consumption, reduce emissions, and increase performance; hence, vehicle manufacturers have found creative ways to cut down the vehicle’s weight without the risk of safety or strength. One innovative solution that has packed a punch is aluminum casting. Thanks to modern aluminum casting technologies, the automotive industry can manufacture lightweight components that are easy to construct and precise in strength. Aluminum die casting has revolutionized the way components are designed and manufactured for vehicles.
Understanding The Necessity Of Lightweight Automobile Components Manufacturing
An improved aspect of automotive manufacture is the inclusion of lightweight components, which assists in the saving of fuel. Weight reduction leads to decreased energy consumption in cars in the form of fuel. This also assists in reducing emissions. With electric vehicles, constructing lighter components assists in improving the distance covered per battery charge.
Moreover, it increases their power characteristics. As a result, the automotive industry is in a constant search for materials with optimum weight-saving properties in particular but which are also reasonably priced and durable. Aluminum casting solutions fit in exactly here.
Why Use Aluminum In Making Parts For Vehicles?
Aluminum is distinguished for its lightweight, its resistance to corrosion, and its strength. These characteristics make it a suitable metal for the automobile industry. When compared to steel, aluminum is about a third the weight but still manages to possess high rigidity and structural strength. It makes lighter but still safe and strong vehicles possible.
In addition, the property of aluminum to be recycled over and over again without its chemical composition altering is in support of the sustainability agenda. Ensuring working with a high-rated aluminum foundry service, the material is maintained in terms of strength, quality, and durability throughout production and recycling processes.
Aluminum Casting Solutions: Techniques and Benefits
In the case of aluminum automotive component casting, there are distinct methods that can be used. These methods have certain advantages depending on the designs or dimensions of the part as well as its accuracy requirements. To understand these, let us consider two methods in greater detail:
1. Aluminum Investment Casting
Aluminum investment casting is a delicate method used to form parts that are by any standard intricate. The technique makes use of a wax pattern that is surrounded by a fine layer of ceramic and then melted out to form the respective cavity. The desired shape is obtained when aluminum is poured into the cavity.
Manufacturers avail metal fabrication service of aluminum investment casting foundry for precision machined elements such as those for the engines, transmission cases, or load bearing structures. The main reason why investment casting is favored in such applications is because shapes with complex details and exact dimensions can be produced without additional operations.
2. Die Casting
Another die and aluminum foundry services is die casting. With this technique, aluminum melt is forced into a die steel tool. Respacing of the surface of the components produced is not required in die casting; thus, the process is quick and cost-effective. This is common for manufacture of engine block components, gearbox housing parts, suspension parts, etc.
High-volume die casting is advantageous in that it makes it possible to manufacture parts of uniform quality—and with complex geometry—in large numbers. It is fast and precise, and so it is much sought after by automobile producers.
Use of Aluminum Casting in Production of Automotive Parts
Aluminum casting is applied to numerous automotive parts for economic, bearing, and safety reasons. Here are a few of the sectors in which aluminum care solutions are most beneficial:
1. Components of Engines
A significant number of companies use aluminum casting to manufacture many engine parts like cylinder heads, engine blocks, pistons, and many others. These parts are made from aluminum because it is light in weight. Hence, it leads to more fuel efficiency. The accuracy achieved by aluminum casting solutions ensures that these components fulfil the necessary performance parameters and can withstand high-temperature stressful operations.
2. Housings of Transmissions and Gearboxes
The housings of the transmission and gearbox serve the purpose of ensuring necessary protection to the internal mechanical systems. Weight reduction is achieved by employing aluminum to make these components. This improves the performance of the vehicle as well as the consumption of fuel. Die-cast aluminum manufacturers make the housings with high precision and durability, as well as offering corrosion resistance.
3. Chassis and Suspension Systems
Additionally, aluminum alloy casting is employed in the manufacture of chassis, suspension arms, and cross members. These elements require strength and rigidity without excess weight. The use of lightweight aluminum components for the chassis improves handling, reduces tire wear, and enhances ride comfort.
4. Wheels and Braking Systems
Today, it is hard to imagine any car not fitted with aluminum alloy wheels. Apart from the most obvious reason, aluminum wheels are used to enhance the heat dissipation during braking, which is important for the brakes. Aluminum casting solutions are also used in designing brake calipers and such other high-stress components where reducing the weight is a priority.
Comments