Common Challenges and Solutions with Thermic Fluid Pumps
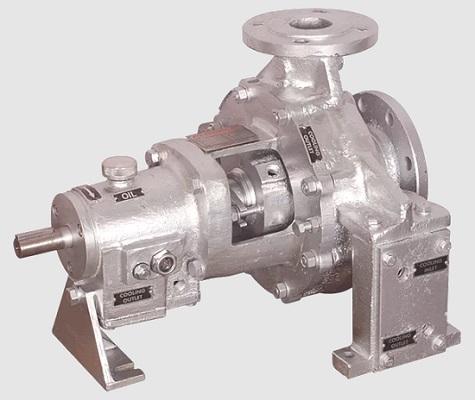
Thermic fluid pumps are essential for efficient heat transfer in industries like chemical handling, power generation, and manufacturing. These pumps circulate thermal fluid or heat transfer oil via systems to move heat at high temperatures, frequently exceeding 350°C (662°F). This makes them vital components in maintaining regular, regulated heat in processes such as reactors, central heating boilers, and heat exchangers.
These pumps can encounter obstacles that affect their efficiency and life expectancy, specifically in high-temperature and demanding environments. Here’s a breakdown of the common issues and sensible remedies to maintain your thermic fluid pumps running successfully.
1. Getting too Hot of Components
Challenge:
Thermic fluid pumps operate in high-temperature environments, which can bring about overheating of crucial parts like seals, bearings, and cases. This can cause early wear, functional failings, and ultimately, expensive downtime. Overheating is a substantial issue since thermal liquid systems commonly run continually in industries such as chemical processing, oil and gas, and power generation.
The extreme heat can place immense stress and anxiety on the pump's elements, especially if the system is not sufficiently made to dissipate heat or if maintenance is overlooked.
Solution:
Select products created to withstand extreme heat, as offered by trustworthy vertical centrifugal pump manufacturers. Carry out cooling down systems or coats around the pump and on a regular basis check temperatures to ensure they remain within safe restrictions.
2. Fluid Leakage
Challenge:
High temperatures can break down mechanical seals in time, causing leak. This not only wastes expensive fluid however likewise postures considerable safety and security threats, especially in industries taking care of dangerous or combustible products. Mechanical seals are crucial in avoiding liquid from getting away the pump, making sure a closed-loop system for thermal liquid blood circulation.
Solution:
Consistently examine and change seals with high-temperature-resistant versions. Upgrade to innovative seal styles like double mechanical or cartridge seals to give added security versus leakages.
3. Cavitation
Challenge:
Cavitation takes place when vapor bubbles develop inside the pump, creating damage to the impeller and reducing pump effectiveness. This phenomenon is specifically bothersome in thermic fluid systems, where the fluid operates at heats and the pump is under consistent thermal and mechanical stress. Cavitation typically happens when suction stress drops below the vapor pressure of the fluid, triggering the liquid to vaporize locally, forming vapor bubbles.
Solution:
Preserve sufficient net positive suction head (NPSH) and make sure the pump is sized correctly for the application. Solutions from centrifugal multi stage pump manufacturers can help in reducing cavitation by providing much better control over suction pressures. Lowering fluid rate and making use of bigger suction lines can also avoid cavitation.
4. Thermal Expansion
Challenge:
Thermal expansion can cause misalignment of interior parts in thermic fluid pumps, bring about boosted wear and tear, particularly on critical parts such as the shaft, impeller, and bearings. When pumps run in high-temperature environments, the materials used in the pump real estate, impellers, shafts, and other inner elements.
Solution:
Pick materials with low thermal expansion residential properties. Routinely examine and correct imbalance, and utilize flexible couplings to make up for expansion during high-temperature operations.
5. Fluid Destruction
Challenge:
Thermic fluids are necessary for transferring warmth in several industrial applications, such as in chemical handling, power generation, and production. Thermic liquids can weaken in time, especially under high-temperature conditions. This deterioration not only lowers the liquid's capacity to move warm efficiently however likewise increases functional costs and can cause significant pump damages if not effectively managed.
Solution:
Monitor fluid high quality with regular testing and use purification systems to maintain pureness. The high requirements of centrifugal chemical pump manufacturers ensure that their pumps can deal with requiring fluid kinds without deterioration issues.
6. Lack of Routine Maintenance
Challenge:
Occasional maintenance can be a substantial threat aspect for thermal liquid pump systems, bring about undetected wear and damage that might cause sudden pump failings, leaks, or failures during crucial functional times. Such failures not only cause pricey downtime yet can also present security risks, environmental dangers, and damage to various other parts of the system.
Solution:
Implement a regular upkeep timetable that consists of evaluation of seals, bearings, lubrication degrees, and alignment. Early detection of issues will help stop major break downs and minimize downtime.
Conclusion
Thermic fluid pumps are workhorses in high-temperature industrial applications, but they require proper care to function effectively. By dealing with typical problems like getting too hot, leak, and cavitation, and executing proactive upkeep strategies, you can ensure your pumps run smoothly and last much longer, decreasing functional disturbances. With proper care, thermic fluid pumps can continue to be trusted workhorses for high-temperature applications, offering regular performance and minimizing operational prices in time.