A Comprehensive Guide to Industrial Valves: Types and Applications
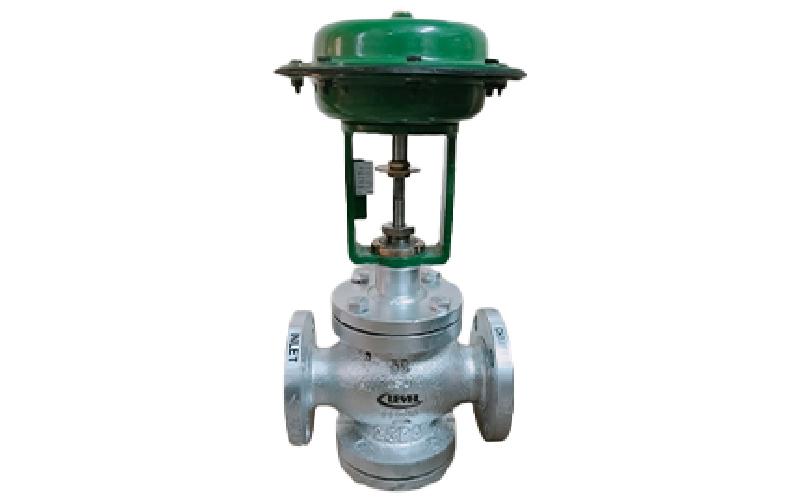
Industrial valves play a pivotal role in controlling the flow of liquids, gases, and slurries in a variety of industrial applications. From manufacturing plants and chemical processing units to water treatment facilities and oil refineries, valves are essential for ensuring that fluids are managed efficiently and safely. Understanding the types of industrial valves and their applications is crucial for choosing the right valve for any given industrial process.
This guide explores the different types of industrial valves, their functions, and the industries that benefit from their use.
What Are Industrial Valves?
Industrial valves are mechanical devices designed to regulate, control, and direct the flow of fluids by opening, closing, or partially obstructing flow paths. Depending on their construction and design, they can control not just the flow but also the pressure and temperature of the fluids passing through them. They are available in various materials such as steel, cast iron, brass, and plastic, depending on the environment in which they are used.
The design and functionality of industrial valves have evolved over time to cater to specific needs across multiple industries, with each type of valve having unique features tailored for certain tasks.
Common Types of Industrial Valves
Here are some of the most common types of industrial valves and their respective applications:
1. Ball Valves
Ball valves use a spherical ball to control the flow of liquid or gas. The ball, with a hole through its center, rotates to either allow or block flow. They are known for providing a tight seal, making them ideal for applications requiring minimal leakage, such as in gas and oil pipelines, water systems, and chemical storage tanks.
Applications: Oil and gas pipelines, chemical storage, water treatment.
Advantages: Durability, easy operation, minimal leakage.
2. Gate Valves
Gate valves operate by lifting a gate (wedge) out of the path of the fluid. These valves are designed to be fully open or fully closed and are typically used when a straight-line flow of fluid is required. They are common in systems where low resistance and uninterrupted flow are essential.
Applications: Water supply systems, wastewater treatment, petrochemical industries.
Advantages: Minimal flow restriction, durability.
3. Globe Valves
Globe valves are used for throttling flow. The valve disc moves perpendicular to the seat, allowing precise control over the flow rate. These valves are often used in applications where the regulation of flow is more important than a complete shut-off.
Applications: Steam control systems, fuel oil systems, cooling water systems.
Advantages: Good throttling capabilities, ease of repair.
4. Butterfly Valves
Butterfly valves feature a rotating disc that opens and closes to control the flow. These valves are lightweight and require less material than other types of valves, making them cost-effective. They are often used in large-diameter pipelines for water supply, air systems, and vacuum services.
Applications: HVAC systems, water treatment plants, food and beverage industries.
Advantages: Lightweight, cost-effective, fast operation.
5. Check Valves
Check valves are used to prevent backflow in a system. These valves automatically allow flow in one direction and prevent it from reversing. They are essential in preventing contamination and protecting equipment from damage due to reverse flow.
Applications: Pump systems, sewage systems, chemical processing.
Advantages: Prevents backflow, low maintenance.
6. Needle Valves
Needle valves provide precise control of flow. They are typically used for fine adjustments in low-flow applications. These valves are designed to regulate flow in sensitive environments such as fuel injection systems or pneumatic systems.
Applications: Instrumentation, fuel injection, pneumatic systems.
Advantages: Precise flow control, compact design.
7. Diaphragm Valves
Diaphragm valves are designed to control the flow of fluids with the help of a flexible diaphragm. These valves are widely used in pharmaceutical, food processing, and wastewater treatment industries, where cleanliness and avoiding contamination are critical.
Applications: Food processing, pharmaceutical industries, water treatment.
Advantages: Hygienic, minimal contamination risk, easy to clean.
Key Considerations When Choosing an Industrial Valve
Selecting the right valve for your application involves understanding several factors, including:
Media Type: The type of fluid (liquid, gas, slurry) will influence the material and type of valve to choose. For example, corrosive chemicals may require valves made of stainless steel or plastic.
Pressure and Temperature: Valves are rated for specific pressure and temperature ranges. Using a valve outside its recommended limits can lead to failure.
Flow Control Requirements: Some valves, like globe or needle valves, offer precise flow control, while others, like gate valves, are better suited for on/off applications.
Maintenance Requirements: Certain valves require more maintenance than others. For instance, ball valves are relatively low maintenance, while globe valves may need more attention.
Cost and Availability: The overall cost of the valve, including installation and maintenance, should be considered. It's also essential to check the availability of the valve type, especially if you're sourcing from industrial valves manufacturers in Ahmedabad or other key industrial hubs.
Applications of Industrial Valves
Industrial valves are used in a variety of sectors, including:
Oil and Gas: Valves control the flow of oil and natural gas through pipelines, storage systems, and refineries.
Water and Wastewater Treatment: Valves regulate water distribution and control the treatment of wastewater to prevent contamination.
Chemical and Petrochemical Industries: Valves are used to control the flow of hazardous chemicals and prevent leaks.
Pharmaceuticals and Food Processing: Hygienic valves are essential in these industries to maintain product quality and avoid contamination.
HVAC Systems: Valves control the flow of air and fluids in heating, ventilation, and air conditioning systems.
Conclusion
Choosing the right industrial valve for your application is crucial to ensuring the efficient and safe operation of your system. By understanding the various types of valves available and their applications, industries can enhance their productivity and operational safety.
When sourcing valves, it is important to collaborate with trusted industrial valves manufacturers in Ahmedabad, who provide a wide range of solutions tailored to specific industry needs. With the right valves in place, companies can ensure smooth operations, reduced downtime, and better control over fluid and gas flow.
Comments