Outage Maintenance Management
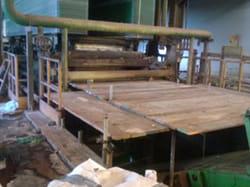
Downtime is a calamity in the intricate world of contemporary industries. For example, it can be in factories, power companies, or computerized items and systems. Therefore, system operation must be smooth always. This is when Outage MaintenanceManagement (OMM) comes in handy. It is defined as the strategic method of managing system breakdowns or maintenance in such a way as to minimize idle time and optimize efficiency.
The Evolution of Outage Maintenance Management
The evolution of Outage Maintenance Management has been substantial through time. In the beginning, it was largely concerned with reactive measures that addressed problems as and when they arose. Unfortunately, this approach resulted in lengthy downtimes and increased operational costs. With the passage of time, the focus shifted towards preventive measures involving regular checks and maintenance to avert possible failures as technology advanced.
Recently predictive maintenance emerged as a revolutionary development. This means organizations can now anticipate defects before they happen using data analytics combined with real-time monitoring which leads to less disruptive and more efficient maintenance regimes. Such an evolution enhances the overall reliability of systems as well as improves operational efficiency.
Key Components of Outage Maintenance Management
Preventive Maintenance: OMM’s most foundational unit is preventive maintenance. In this aspect, it refers to the process of checking and servicing equipment on a routine basis so that they do not fail. This way, organizations can take care of small hitches before they blow out of proportion by always inspecting and servicing their systems. Besides extending the life span of the various equipment, preventive maintenance serves its purpose of minimizing unanticipated equipment failure.
Predictive Maintenance: The act of predictive maintenance builds on the previous standpoint on prevention. It involves the use of data and analytics to see possible failures before they occur and thereby plan for them to avoid unplanned downtimes through predictive maintenance. So it goes without saying that examining how a system performs as well as looking at data trends are some of the other ways organizations can tell when next they should maintain machines. This enhances reduced downtime because issues would have been taken care of earlier on rather than during an unfortunate breakdown.
Emergency Response Planning: Regardless of how well plans are designed to prevent or predict outages, they can still happen by surprise. Part of a good OMM strategy consists of an emergency response plan that is well laid out. The steps that should be taken during an outage, including communication procedures, resource allocation, and recovery protocols, are contained in this plan. If these are done together as one command it may help lessen its duration and impact on quality.
Resource Management: A crucial factor in effective outage maintenance is the efficient management of resources. This requires on-hand tools right spare parts and people with the necessary skills ready to handle different outages promptly (Perkins, 2001). Hence, if resources are managed properly then repairs can be initiated fast enough thus minimizing downtime as well as interference with normal business operations.
Communication: It is important for all parties concerned to know what is happening with the system, what type of failure has occurred, and when it is likely to get back on track again. As such, managing expectations and dampening the blow on business operations becomes easier. When needed, effective communication also means coordinating with outside people or organizations that offer services or goods.
Resource Allocation and Management in OMM
In Outage Maintenance Management (OMM), proper resource allocation is the key ingredient. To reduce downtime and sustain operational effectiveness as much as possible, it is essential to avail the right tools, spares at hand, and even skilled personnel at such a time when their need arises. Hence, careful planning and synthesis are needed to avert delays and interruptions.
It also involves optimizing inventory levels as well as scheduling maintenance activities in line with operational requirements. In addition, organizations should consider the cost of keeping a well-equipped and trained maintenance team. To attain an effective and efficient maintenance strategy, resource availability must be balanced with operational needs.
Integration of AI and Machine Learning in Maintenance
Artificial Intelligence (AI) and Machine Learning (ML) are changing the way when outages happen. Predictive maintenance can also be achieved through analyzing big data, as human intervention depends on machines’ ability to find trends and foresee possible failures. To make recommendations for maintenance, these AI tools can analyze past data, so that they determine deviations or unexpected movements in the system and thus help in reducing human inspections.
Furthermore, AI and ML improve decision-making by giving relevant information and executing routine jobs. As such, this combination allows for improved prediction of what maintenance is needed and better management of resources. These technologies will also play a critical role in improving maintenance strategies and reducing downtime as they evolve.
To Wrap This Up
In different sectors, Outage Maintenance Management is important in reducing system downtime and enhancing efficiency optimally. From unpredictable to predictable and proactive methods of doing outage maintenance management, this has led to a more proactive discipline that uses artificial intelligence and machine learning. Additionally, effective resource, communication, and disaster management can greatly improve the reliability of operations. The mainstay for the smooth running of the system without interruptions is by using such technologies while avoiding excess downtime.
Comments