Choosing the Right Industrial Valve for Your Application
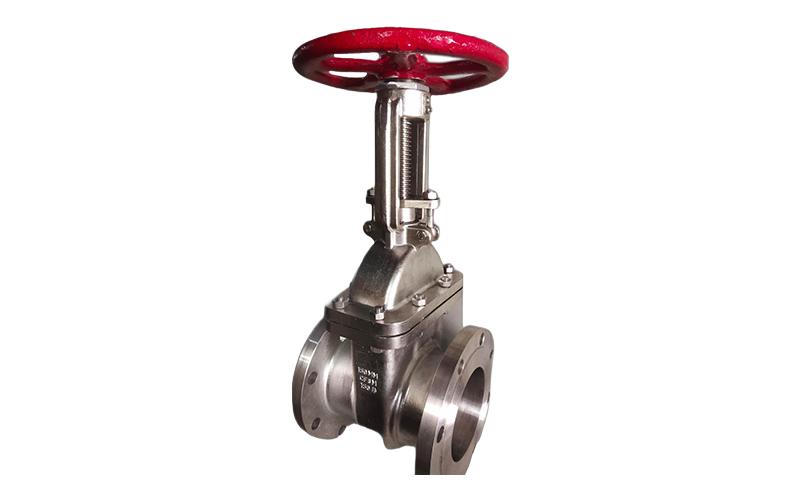
Industrial valves are critical components in a variety of industries, including oil and gas, chemical, water treatment, pharmaceuticals, and manufacturing. They serve the essential function of controlling the flow of liquids, gases, or slurries within a system. Whether it’s regulating pressure, isolating a process, or directing the flow, selecting the right industrial valve for a specific application is crucial to ensuring system efficiency, safety, and longevity. With numerous valve types available, ranging from ball valves to butterfly valves, the decision can become overwhelming. Here’s a comprehensive guide to help you choose the right industrial valve for your application.
Understand the Application Requirements
The first step in choosing the right industrial valve is to thoroughly understand your system’s requirements. Every application has its unique demands, including flow rate, pressure, temperature, and the nature of the media (liquid, gas, or slurry). Valves must be selected based on their ability to handle these specific conditions.
For instance, in high-temperature applications, such as steam or chemical processes, valves made from materials that can withstand extreme heat without degrading are essential. Similarly, if the media is corrosive, such as certain chemicals or saltwater, valves with corrosion-resistant coatings or materials are a must. Industrial valves manufacturers typically offer various materials, including stainless steel, brass, bronze, and specialized alloys, each designed to meet the needs of different industries.
Types of Valves
Understanding the different types of industrial valves is crucial in making the right selection. Each valve type serves a distinct function in controlling the flow of fluids or gases. Let’s look at some of the most common valve types:
Ball Valves: These are excellent for on-off applications. They offer a tight seal and are durable, making them ideal for applications involving high pressure and temperature. Ball valves are commonly used in industries like oil and gas, water treatment, and manufacturing.
Butterfly Valves: Known for their compact size and quick action, butterfly valves are ideal for regulating flow. They are used in applications requiring tight shutoff and moderate throttling capabilities, such as in HVAC systems or water treatment plants.
Gate Valves: These are used when a straight-line flow of fluid and minimal restriction is required. Gate valves are typically used in applications where the valve remains fully open or fully closed, such as in water distribution systems.
Globe Valves: Globe valves are designed for regulating flow in a pipeline. They are commonly used when precise throttling and control are necessary, making them ideal for steam, oil, and gas applications.
Check Valves: These are unidirectional valves, allowing fluid to flow in only one direction. They are typically used in pump systems or where backflow could cause damage to equipment.
Needle Valves: These valves are perfect for applications requiring precise control of flow. They are typically used in low-flow applications and are often found in the oil and gas industry, where accurate metering of fluids is essential.
Choosing the right valve type ensures that your system operates smoothly and meets the application’s needs. Industrial valves manufacturers offer detailed specifications to help you determine which valve type is suitable for your system.
Consider the Flow Characteristics
Different valves have varying flow characteristics, which is the relationship between the valve position and the flow rate. Some valves provide a linear flow characteristic, where flow increases proportionally with valve opening. Others, like ball and butterfly valves, exhibit quick-opening characteristics, where a small change in valve position results in a large change in flow. If your application requires precise flow control, consider a valve with linear flow characteristics, such as a globe or needle valve.
Additionally, consider the Cv (flow coefficient) rating, which indicates how much fluid can pass through the valve. The higher the Cv, the more fluid the valve can handle. Be sure to choose a valve that has the appropriate Cv rating for your system to avoid over-pressurizing or under-utilizing the valve.
Pressure and Temperature Ratings
Every industrial valve has specific pressure and temperature ratings that dictate the conditions under which the valve can operate. Ensure that the valve you select can handle the maximum pressure and temperature of your system. Valves not rated for the conditions they will encounter can lead to system failures, leaks, or hazardous working environments. Many industrial valves manufacturers provide detailed ratings to ensure that users select the appropriate valve for their applications.
For high-pressure systems, valves like ball, gate, and globe valves are suitable choices due to their robust construction and ability to handle intense pressure. On the other hand, for lower pressure systems, butterfly valves and diaphragm valves are more economical choices.
Material Compatibility
Valve material plays a critical role in ensuring durability and long-term performance. Different media can interact with valve materials in various ways, leading to corrosion, erosion, or degradation. For example, if the valve will be exposed to corrosive chemicals, stainless steel or other corrosion-resistant materials are essential. In applications involving food and beverages, where hygiene is a concern, food-grade stainless steel or plastic materials might be required.
When choosing the right industrial valve, it is crucial to consider the material compatibility with the media. Most industrial valves manufacturers offer a range of materials to suit different application environments, from chemical plants to water distribution systems.
Maintenance and Durability
The maintenance requirements and durability of industrial valves are other key factors to consider. Some valves, such as ball and butterfly valves, require minimal maintenance and offer long service life, making them ideal for applications where accessibility is limited. In contrast, valves like globe valves may require more frequent maintenance due to their complex design and control functions.
Selecting a valve that offers easy maintenance and durability can significantly reduce downtime and operating costs. Many industrial valves manufacturers provide valves with design features that enable quick maintenance or repair without the need for complete system shutdowns.
Conclusion
Selecting the right industrial valve for your application involves a thorough understanding of your system’s requirements, the type of valve needed, flow characteristics, pressure and temperature ratings, material compatibility, and maintenance considerations. By considering these factors, you can choose a valve that enhances system performance, minimizes downtime, and ensures safe operation. Most importantly, collaborating with reputable industrial valves manufacturers is vital to obtaining high-quality valves that meet the specific needs of your industry.
Comments