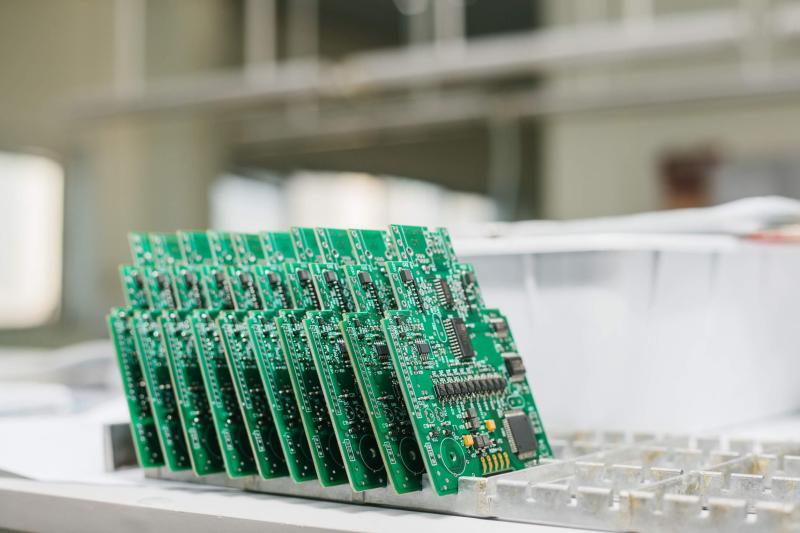
Printed circuit boards or PCBs are the
backbone of modern electronic devices. From the smartphone in your hand to the
computer on your desk, PCBs ensure everything runs smoothly. But what precisely
goes into the cost of a PCB? Understanding these factors is crucial for
businesses and hobbyists alike, as it can help you manage your budget and make
informed decisions.
What is a
Printed Circuit Board?
A printed circuit board serves as the
foundation for most electronic devices. It's a flat board made of
non-conductive materials with conductive pathways etched onto its surface,
allowing for the connection and support of electronic components. PCBs come in
various sizes and complexities, tailored to fit specific applications, from
simple consumer gadgets to intricate industrial machinery.
The function of a printed circuit board is
to mechanically support and electrically connect electronic components using
conductive tracks, pads, and other features etched from copper sheets laminated
onto a non-conductive substrate. Components such as resistors, capacitors, and
integrated circuits are typically soldered onto the printed circuit board,
creating a complete and functioning electronic device.
Understanding the basic structure and
purpose of a printed circuit board is essential, especially when considering
the factors that influence its cost. The design, material selection, and
manufacturing processes all play significant roles in determining the final
price tag of a printed circuit board.
1. Material
Type and Quality
The type and quality of materials used in
the construction of a printed circuit board significantly impact its cost.
Common materials include FR-4, Rogers, and aluminum. FR-4, a glass-reinforced
epoxy laminate, is widely used due to its affordability and good performance.
Rogers materials, known for their high-frequency capabilities, are more
expensive but necessary for specific applications.
Material quality also matters. Higher-grade
materials ensure better performance and durability but come at a higher price.
For instance, using a high-temperature laminate might be essential for certain
applications but will increase the overall cost. It's crucial to balance
material quality with budget constraints, selecting the best option that meets
your project's requirements without overspending.
2. Layer
Count
The number of layers in a printed circuit
board is another critical cost factor. Single-layer PCBs are the simplest and
cheapest, while multi-layer PCBs, which can have up to 30 or more layers, are
more complex and costly. Each additional layer requires more materials and
intricate manufacturing processes, driving up the price.
Complex projects often necessitate
multi-layer PCBs to accommodate various connections and components. However, if
your design can be achieved with fewer layers, it's a cost-effective strategy
to stick with a simpler, single or double-layer PCB. Proper planning and design
optimization can help minimize layer count without compromising functionality.
3. PCB Size
and Thickness
The physical dimensions of a printed
circuit board directly influence its cost. Larger boards require more materials
and take longer to manufacture, leading to higher prices. Similarly, the
thickness of the board can affect the cost. Thicker PCBs might be necessary for
certain applications, like high-power electronics, but they also require more
raw materials and processing time.
Optimizing the size and thickness of your
printed circuit board design can result in significant cost savings. By
carefully planning the layout and ensuring efficient use of space, you can
reduce the amount of material needed without sacrificing performance.
Collaborating with your manufacturer during the design phase can also help
identify potential cost-saving adjustments.
4. Trace
Width and Spacing
Trace width and spacing refer to the
dimensions and distance between the conductive pathways on a printed circuit
board. These factors are crucial for ensuring proper electrical performance and
preventing issues like short circuits or signal interference. However, finer
trace widths and tighter spacing require advanced manufacturing techniques,
which can increase costs.
Balancing trace width and spacing with cost
considerations involves understanding the electrical requirements of your
project. In some cases, slightly wider traces and more generous spacing can
achieve the desired performance while reducing manufacturing complexity and
cost. Consulting with your PCB manufacturer can provide insights into the most
cost-effective design choices.
5. Solder
Mask and Silkscreen
The solder mask and silkscreen layers are essential
for protecting the printed circuit board and providing important information,
respectively. The solder mask is a protective layer applied over the copper
traces to prevent solder bridges and oxidation. Different colors and types of
solder masks are available, with some options being more expensive than others.
The silkscreen layer involves printing text
and symbols on the printed circuit board to label components and provide
assembly instructions. While the cost of silkscreen printing is generally low,
complex designs with multiple colors can add to the overall expense. Choosing
standard solder mask and silkscreen options can help keep costs down without
compromising functionality.
6. Surface
Finish
The surface finish of a printed circuit
board is crucial for ensuring good solderability and protecting the exposed
copper from oxidation. Common surface finishes include HASL (Hot Air Solder
Leveling), ENIG (Electroless Nickel Immersion Gold), and OSP (Organic
Solderability Preservatives). Each option has different costs and benefits.
HASL is one of the most cost-effective
finishes but may not be suitable for fine-pitch components. ENIG, while more
expensive, offers excellent surface planarity and long shelf life, making it
ideal for high-reliability applications. Understanding the specific
requirements of your project will help you choose the most appropriate and
cost-effective surface finish.
7. Quantity
and Turnaround Time
The quantity of PCBs ordered and the
required turnaround time are significant factors affecting cost. Ordering PCBs
in bulk generally reduces the per-unit cost due to economies of scale. However,
smaller quantities or prototype runs may have higher costs per unit.
Turnaround time is another consideration.
Faster production times often come with a premium price. If your project
timeline allows, opting for standard lead times can result in cost savings.
Planning ahead and placing orders in advance can help manage expenses and avoid
rush fees.
The Wrap up
Understanding the factors that influence
the cost of PCBs is essential for anyone involved in electronics design and
manufacturing. By considering material type and quality, layer count, size and
thickness, trace width and spacing, solder mask and silkscreen, surface finish,
and order quantity and turnaround time, you can make informed decisions that
balance performance and budget.
At the end of the day, the goal is to create a high-quality PCB that meets
your project's needs while staying within budget. By optimizing your
design and working closely with your manufacturer, you can achieve the best
possible outcome for your electronic devices.
Comments