Why a metal core PCB is better than a regular PCB
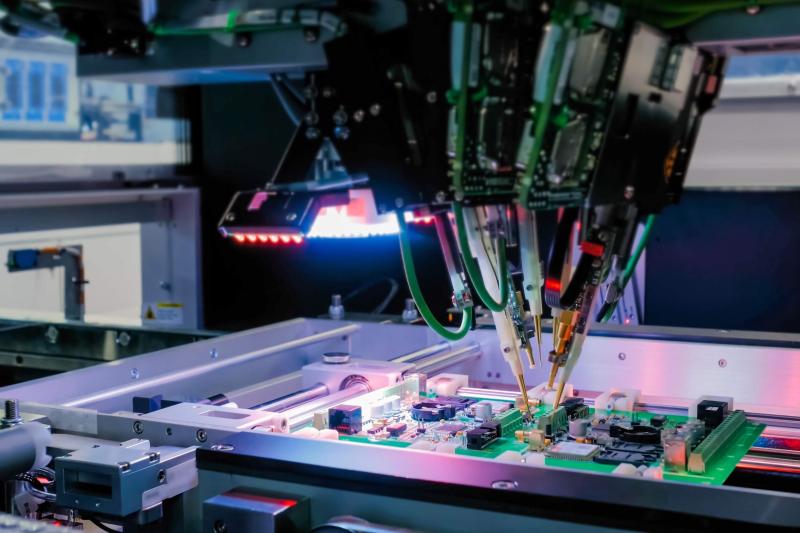
Printed Circuit Boards or PCBs are the
backbone of modern electronics. From smartphones to industrial machinery, they
are integral to the functionality of countless devices. But not all PCBs are
created equal. When it comes to performance, durability, and thermal
management, a metal core PCB or
MCPCB stands out.
Understanding
Metal Core PCBs
It is a type of printed circuit board that
features a metal material as its base. The most common metals used are
aluminum, copper, and a mixture of metal alloys. The metal core in these PCBs
serves as a heat sink, efficiently dissipating heat away from the components.
MCPCBs are designed for high-power
applications where heat dissipation is critical. Unlike regular PCBs, which use
fiberglass as their base material, MCPCBs have a metal core that significantly
enhances their thermal management capabilities. This makes them ideal for
applications in LED lighting, power converters, and automotive industries.
The
Structure of MCPCBs
The structure of an MCPCB
typically includes a metal base, a thermally conductive but electrically
insulating layer, and a copper circuit layer. The metal base provides
mechanical stability and heat dissipation, while the insulating layer ensures
electrical separation between the metal base and the copper circuit layer.
The combination of these layers allows
MCPCBs to handle higher current loads and better thermal performance. This
structure is particularly beneficial in applications where heat can degrade the
performance or lifespan of electronic components.
Typical
Applications
MCPCBs are commonly used in industries
where heat management is crucial. Some of the most common applications include:
·
LED lighting systems, where
efficient heat dissipation is essential for maintaining brightness and
extending the lifespan of LEDs.
·
Power supplies and power
converters, where high currents can generate significant heat.
·
Automotive electronics, where
durability and thermal management are critical due to the harsh operating
environments.
Understanding the structure and
applications of MCPCBs highlights the unique benefits they offer over regular
PCBs, especially in high-power and heat-sensitive applications.
Seven
Reasons Why a Metal Core PCB is Better than a Regular PCB?
1. Superior
Thermal Management
One of the primary advantages of MCPCBs is
their superior thermal management. The metal core acts as a heat sink,
efficiently dissipating heat away from the components. This prevents
overheating and ensures the stable operation of electronic devices.
In contrast, regular PCBs with fiberglass
bases lack the same level of thermal conductivity. This can lead to
overheating, which can degrade the performance of components and reduce their
lifespan. In high-power applications, effective thermal management is crucial
for maintaining reliability and performance.
2. Enhanced
Durability
MCPCBs are more durable than regular PCBs
due to their robust metal core. The metal base provides mechanical stability
and resistance to physical stress. This makes MCPCBs suitable for applications
in harsh environments where durability is essential.
Regular PCBs, on the other hand, are more
prone to damage from physical stresses such as vibration and impact. This can
limit their use in demanding applications and environments where durability is
a key requirement.
3. Higher
Current Carrying Capacity
The metal core in MCPCBs allows them to
handle higher current loads compared to regular PCBs. This is particularly
important in applications such as power supplies and power converters, where
high currents are common.
Regular PCBs with fiberglass bases have
limited current-carrying capacity, which can restrict their use in high-power
applications. The ability to handle higher currents makes MCPCBs a better
choice for power-intensive applications.
4. Improved
Reliability
The enhanced thermal management and
durability of MCPCBs contribute to improved reliability. By efficiently
dissipating heat and withstanding physical stresses, MCPCBs ensure stable and
reliable operation of electronic components.
In contrast, the limited thermal management
and durability of regular PCBs can lead to overheating and physical damage,
reducing the reliability of electronic devices. For applications where
reliability is critical, MCPCBs offer a significant advantage.
5. Compact
Designs
MCPCBs enable more compact designs by
efficiently managing heat and allowing higher current loads. This can reduce
the need for additional cooling components, such as heat sinks and fans,
resulting in smaller and more streamlined designs.
Regular PCBs may require additional cooling
components to manage heat, which can increase the size and complexity of
electronic devices. The ability to achieve compact designs is particularly
valuable in applications where space is limited.
6.
Versatility in Applications
MCPCBs are versatile and can be used in a
wide range of applications, from LED lighting to automotive electronics. Their
ability to handle high currents and efficiently dissipate heat makes them
suitable for various industries and environments.
Regular PCBs, with their limitations in
thermal management and current-carrying capacity, may not be suitable for all
applications. The versatility of MCPCBs makes them a better choice for diverse
and demanding applications.
7.
Cost-Effectiveness in the Long Run
While MCPCBs may have a higher initial cost
compared to regular PCBs, they can be more cost-effective in the long run. The
improved reliability, durability, and thermal management of MCPCBs can reduce
maintenance costs and extend the lifespan of electronic devices.
Regular PCBs, with their limited thermal
management and durability, may incur higher maintenance costs and have a
shorter lifespan. Investing in MCPCBs can result in long-term savings and
improved performance.
Final Words
MCPCBs offer several advantages over
regular PCBs, including superior thermal management, enhanced durability,
higher current-carrying capacity, improved reliability, compact designs,
versatility in applications, and cost-effectiveness in the long run. These
benefits make a metal core PCB a better choice for high-power and
heat-sensitive applications.
If you are looking to optimize the
performance and reliability of your electronic devices, consider integrating
MCPCBs into your designs. Their unique benefits can help you achieve better
thermal management, durability, and overall performance.