How Digital Twins are Transforming Manufacturing: A Step-by-Step Guide
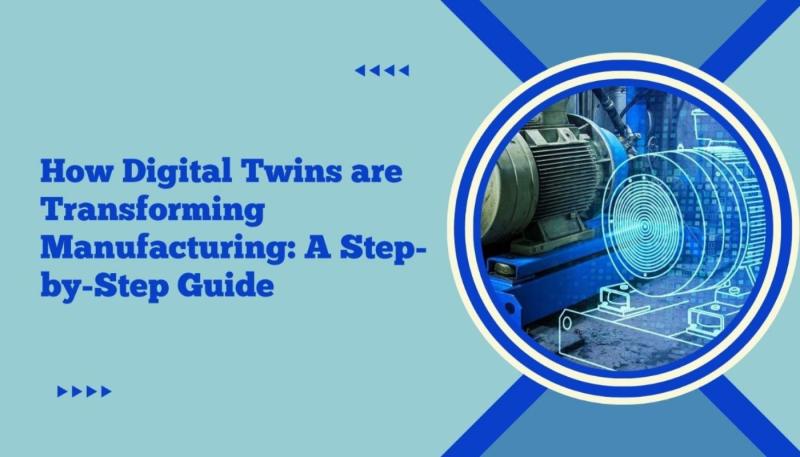
Digital Twin technology is emerging as the game-changer in the manufacturing industry. These digital twins of physical assets, processes, and systems are transforming how manufacturers enhance productivity, estimate when equipment will fail, and drive innovation. In this detailed guide, we will discuss how to use digital twins and learn more about how this technology will revolutionize the manufacturing industry.
What are Digital Twins: The Basics
Digital twins are digital replicas of real processes and objects that allow manufacturers to control, analyze, design, and improve the processes and the outcomes without the necessity of trials and field research. These dynamic representations are a virtual environment in which the manufacturing operations can be tested and improved.
Key Components of Digital Twins
Real-time data: Sensors and IoT devices are the sources of data that are used in digital twins, making the simulations and analysis accurate.
Predictive analytics: Digital twins use machine learning and AI to predict equipment failures, improve the efficiency of the processes, and speed up product development
Interconnectivity: Digital twins complement other advanced technologies such as augmented reality, cloud computing
Creating Your Digital Twin: Decoding the Method
Step 1: Self-Check – Review Your Manufacturing Processes
You can start with the assessment of the current state of the manufacturing processes, the definition of the problems, and the areas of improvement Some of the areas include efficiency, maintenance, and quality of the products.
Step 2: Collection and incorporation of the data
It is important to gather data from sensors, IoT devices, and other devices to feed into your digital twin in real-time. You need to make sure that data is collected from different systems and in different formats and then make a unified virtual model.
Step 3: Build Your Digital Twin
Users can leverage the latest software and simulation tools to develop an accurate model of the manufacturing process. This should be a virtual duplicate of the physical environment and must take into account elements such as the performance of the machines, the process parameters, and the working environment.
Harnessing the Power of Digital Twins in Manufacturing: Use Cases
Predictive Mainatinna
Digital twins can also predict equipment failures by using data from the sensors and the records of previous maintenance. This is because most problems are likely to occur at a certain time and thus can be overcome before they take place hence saving the manufacturer a lot of cash and the assets used in production are also likely to last longer.
Process Optimization
Manufacturers can explore different situations in the digital twin environment and understand how to optimize the process and minimize losses. This is a virtual platform through which real-life scenarios are simulated but without affecting the real processes.
Product Development
Digital twins can potentially help in the reduction of the time it takes to develop a product since physical prototypes may be used virtually. Manufacturers can test product functionality under one or another condition, receive feedback and, if needed, introduce some changes in the product without creating expensive physical prototypes.
Designing Holograms, and Hologram Tables for Holistic Experience
The use of digital twins can be used in the creation of wonderful holographs and hologram tables whereby stakeholders, guests, and employees can be immersed. These modern infographics provide an interesting approach to presenting the manufacturing processes, working with information, and communicating between the teams.
Benefits of Holograms and Hologram Tables
Interactive experiences: Guests get to interact with objects and perform various tasks, thus improving comprehension.
Educational opportunities: Holograms and hologram tables are used as effective means of inculcating knowledge in students and other professionals on the concepts of advanced manufacturing.
Stakeholder engagement: The use of immersive visualizations is to enhance understanding of the complexities and the changes in the manufacturing process among the stakeholders.
The Future of Manufacturing: Digital Twins and Beyond
In the coming years, digital twins are likely to become a central force behind the further development of manufacturing. Historic development of Industry 4. 0 and the constant focus on integration, robotics, and real-time information, digital twins are going to become a must-have to sustain competitiveness in the global environment.
Emerging Trends in Digital Twins:
Increased adoption: Increasingly, manufacturers are using digital twin to design lean adaptive, and fast-responding production processes
Integration with emerging technologies: Digital twins will easily integrate with advanced technologies such as 5G, edge computing, and digital thread to improve their performance.
Expansion into new industries: The use of digital twins will go beyond manufacturing and will expand into sectors like healthcare, transportation, smart cities, and others.
Conclusion!
Digital twins are revolutionizing the manufacturing industry through improving processes, prediction of maintenance requirements, and innovation. The manufacturer can make a simulation of their physical environment to discover aspects that would enable them to make better decisions and enhance efficiency. The future of manufacturing is brighter with the popularity of the adoption of digital twins which are likely to help in increasing efficiency, decreasing costs, and improving quality.
Comments