Disinfectant Mistakes to Avoid in B2B Environments: What You Need to Know
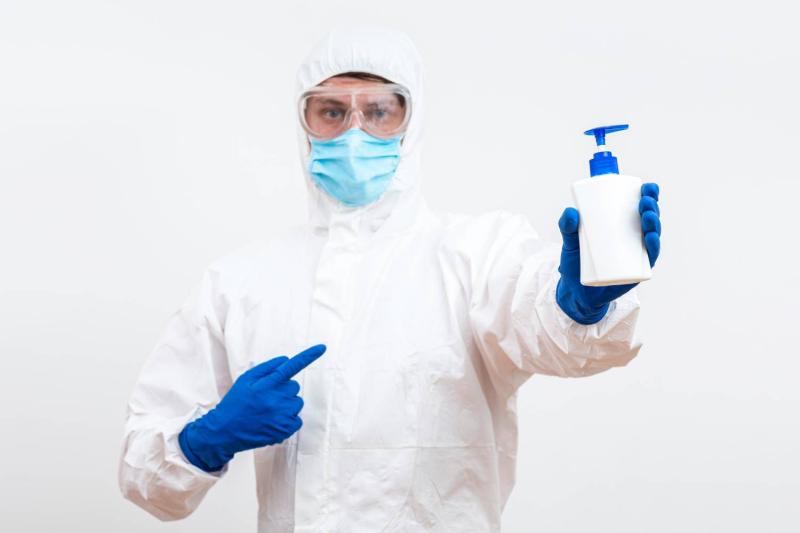
In today's business world, maintaining a clean, sanitized, and safe working environment is essential, not only for the health and well-being of employees but also for the reputation of your business. In B2B environments—whether you're running an office, warehouse, healthcare facility, food production plant, or any other commercial space—the proper use of disinfectants is crucial in preventing the spread of germs, bacteria, and viruses. However, improper usage of disinfectants can lead to ineffective cleaning, exposure to harmful chemicals, and even compliance issues.
In this comprehensive guide, we’ll explore the common disinfectant mistakes many businesses make, how to avoid them, and why understanding these pitfalls is vital for ensuring a safe, healthy, and compliant workplace. We’ll also touch on how the right disinfecting products can improve efficiency and help safeguard your business.
What Are Disinfectants?
Before diving into common mistakes, let’s clarify what disinfectants are and their role in cleaning. Disinfectants are chemical agents used to eliminate harmful microorganisms, including bacteria, viruses, and fungi, from surfaces. Unlike regular cleaners, which may remove dirt and debris, disinfectants are specifically formulated to kill pathogens, making them essential in both everyday cleaning and more specialized environments like hospitals, kitchens, or industrial sites.
Disinfectants come in a wide range of products—sprays, wipes, wipes, liquids, and concentrates—and are classified based on the type of pathogens they target (e.g., broad-spectrum disinfectants, virus-specific disinfectants). It’s crucial to choose the right disinfectant for the job, considering factors like surface material, microbial target, and contact time.
Common Disinfectant Mistakes in B2B Environments
1. Using the Wrong Disinfectant for the Job
Mistake: Not all disinfectants are suitable for every situation. A disinfectant that works well in a healthcare setting might not be appropriate for a food manufacturing environment, and vice versa.
Why It Matters: Different industries have varying cleanliness standards. For instance, in healthcare, it’s critical to use disinfectants that can effectively kill viruses and bacteria to prevent cross-contamination. In food production, on the other hand, cleaning agents must be safe for food contact and non-toxic.
Solution: Always choose the right disinfectant based on the industry-specific needs of your business. If you're working in a high-risk environment, opt for hospital-grade disinfectants or ones that have been approved by relevant regulatory bodies, like the Environmental Protection Agency (EPA). Make sure your products are compliant with regulations (e.g., NSF/ANSI certification for food safety).
2. Incorrect Application and Dosing
Mistake: Many businesses overuse or underuse disinfectants, assuming that more product means better results. On the other hand, using too little may lead to insufficient disinfection.
Why It Matters: Disinfectants are formulated for specific concentrations to be effective. Overuse leads to unnecessary chemical exposure, potential damage to surfaces, and higher costs. Underdosing, however, means you're not effectively eliminating harmful pathogens.
Solution: Always follow the manufacturer’s recommended dilution ratios and application instructions. In many cases, too much disinfectant can lead to residue buildup, which can actually attract dirt and germs. Ensure your staff are trained on how to mix and apply disinfectants properly, and use measuring devices to ensure accuracy.
3. Failing to Allow Sufficient Contact Time
Mistake: One of the most common mistakes in B2B environments is not allowing disinfectants enough time to work. Often, businesses will quickly wipe off or rinse off surfaces before the disinfectant has had the chance to fully disinfect.
Why It Matters: Disinfectants need adequate contact time (sometimes referred to as “dwell time”) to effectively kill pathogens. Rushing through the disinfection process may leave harmful germs behind, rendering your cleaning efforts ineffective.
Solution: Always adhere to the contact time specified by the product manufacturer. Some disinfectants may require a few seconds of contact, while others could need several minutes. This is critical for ensuring that the cleaning process is thorough and compliant with health guidelines.
4. Using Disinfectants on Surfaces Not Suitable for Chemicals
Mistake: Applying disinfectants on surfaces that are not compatible with the chemicals, like certain metals, fabrics, or finishes, can lead to damage.
Why It Matters: Harsh disinfectants can corrode metals, discolor fabrics, and even damage sensitive electronics. This not only affects the appearance and integrity of your workplace but can also cause long-term issues, like deteriorating machinery or surfaces that need expensive repairs.
Solution: Always read product labels carefully to check for compatibility with the surfaces you intend to disinfect. In cases where the disinfectant might cause damage, look for alternatives such as eco-friendly products or those formulated for sensitive surfaces.
5. Mixing Different Disinfectants
Mistake: Some businesses mix different cleaning and disinfectant products in an attempt to boost effectiveness, but this can create dangerous chemical reactions.
Why It Matters: Mixing certain chemicals (like bleach and ammonia) can lead to toxic fumes or harmful reactions, putting employees at risk of respiratory issues, burns, or even poisoning.
Solution: Never mix cleaning agents unless the product labels explicitly say it is safe to do so. Stick to one disinfectant at a time, or, if you need different products for various surfaces, apply them separately with proper ventilation.
6. Overlooking Ventilation and Personal Protection
Mistake: Inadequate ventilation or failure to provide personal protective equipment (PPE) during disinfecting processes can expose workers to harmful chemicals.
Why It Matters: Many disinfectants contain harsh chemicals that can cause respiratory distress or skin irritation if not handled properly. In enclosed spaces, the fumes can accumulate and pose serious health risks.
Solution: Ensure that your workspace is well-ventilated during cleaning. Use exhaust fans, open windows, or even air purifiers in confined areas. In addition, provide employees with appropriate PPE, including gloves, masks, and protective eyewear, depending on the level of chemical exposure.
7. Not Following Proper Disinfection Procedures
Mistake: Many businesses rush through the cleaning process without following the proper procedures for disinfecting high-touch areas or neglected spots.
Why It Matters: High-touch surfaces like door handles, light switches, keyboards, and shared equipment are prime areas for pathogen transmission. Skipping these spots or not cleaning them thoroughly increases the risk of cross-contamination.
Solution: Establish a cleaning and disinfection protocol that addresses all areas of the workspace, with particular attention to high-touch surfaces. Consider using a touchless cleaning solution, such as UV-C light systems or automated disinfecting machines, to ensure thorough disinfection.
8. Ignoring Regular Cleaning and Maintenance of Disinfectant Equipment
Mistake: Neglecting to clean and maintain disinfecting equipment (like sprayers, mops, and cloths) can lead to contamination and reduce the effectiveness of the disinfectant.
Why It Matters: Dirty or clogged equipment can reduce the effectiveness of disinfectants, causing them to be less efficient at eliminating pathogens. Additionally, residues from previous cleaning sessions can contaminate new surfaces, spreading germs instead of eliminating them.
Solution: Ensure that all cleaning equipment is regularly cleaned and maintained. Replace or sanitize mop heads, cleaning cloths, and sprayers as needed. Additionally, inspect and clean any automated disinfection systems (e.g., foggers or UV sanitizers) regularly.
Why the Right Disinfectant Matters
Choosing the right disinfectant for your business needs can prevent many of the common mistakes we’ve discussed and help your company maintain a clean, safe, and healthy working environment. High-quality disinfectants, like those you can find in our ecommerce store, are formulated to meet the highest standards of efficacy, safety, and environmental responsibility.
In addition to protecting employee health, using the right disinfectant helps your business stay compliant with health regulations (such as OSHA, CDC guidelines, and local laws), minimizing risks of violations or fines. It also reflects well on your company’s commitment to hygiene, which is increasingly important in today’s health-conscious business world.
Conclusion: Disinfect Correctly, Stay Safe
The importance of proper disinfectant usage in B2B environments cannot be overstated. By avoiding common mistakes like using the wrong product, improper application, and neglecting safety protocols, businesses can ensure a healthier, safer workplace. Moreover, investing in the right disinfectants and educating your team on their correct use not only protects your employees but also enhances your business’s reputation and operational efficiency.
As you stock up on cleaning products, ensure that you choose high-quality, industry-approved disinfectants that will effectively eliminate harmful pathogens. Remember, a clean business is a productive and safe business—one that fosters trust among employees and clients alike.
Comments