Thermal Interface Materials | Thermal Management Solutions - Techni3
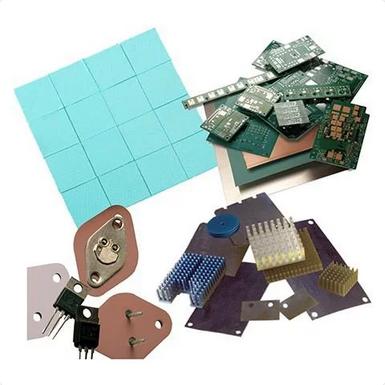
Thermal Interface Materials
What are Thermal Interface Materials?
Successful thermal management of high-power electronic components (single chips, multi-chip modules, integrated circuits, etc.) with high heat dissipation ratings requires careful design engineering. The most important goal in electronic cooling is to maintain junction temperature from rising above prescribed levels. Junction temperature is good predictor of the useful life of the component. Thermal interface materials bridge the interface between hot components and a chassis or heat sink assembly. Heat transfer is increased, and components are kept cooler. An example is a gap filler pad transferring heat between two or more solid surfaces.
How do they work?
Materials formulated in the lab are manufactured and inserted between parts to enhance the thermal coupling. Most applications involve dissipating heat. When two surfaces are interfaced, rough surfaces create insulating air gaps between them. These gaps create thermal barriers to heat transfer due to the low thermal conductivity of air. Heat will transfer and be removed more rapidly because of the presence of an engineered material that has significantly higher thermal conductivity than the air in the interface. Thus, the material helps minimize the resistance of heat flow into, through, and out of an interface.
What are Common Uses?
● Gap Filler Pads – These materials can offer a unique combination of extremely high thermal conductivity and softness. The combined features reduce mechanical stress while maintaining thermal performance. Several offerings are free of silicone, an ideal situation for some applications, Some feature no oil bleed. An example is a gap filler pad transferring heat in a densely packed PCB.
● Dispensable Gap Fillers – Examples include liquid putty gap fillers, thermal pastes, gels, and greases. They are generally non-electrically conductive. Putty is used for filling in gaps that are present between irregular or unusual surfaces or those that do not touch one another. A popular application of liquid gap fillers is handheld gaming systems. Fragile components, design density, and high operating temperatures are common issues to be resolved.
● Phase Change – Components within servers and computers of all types achieve increased processing speeds and overall functionality and reliability improvements with phase change materials. They take advantage of latent heat of fusion to absorb heat, but they change phase only once to allow for the material to fill up all nooks and crevices. Screen-printable formulations deliver the reliability and performance of a phase change material with the low-cost handling of thermal grease.
● Automation Support – Through advancements in robotic motion control, users can now automate the application of all forms of thermal interface materials. These pioneering applications add speed, reliability, and rapid ROI to any application process while lowering overall costs.
● Electrically Insulating -Electrical isolation can be a critical design consideration in numerous applications. Electrically insulating products offer solutions whenever reliability, cut-through resistance, and thermal conductivity are critical factors. Military and aerospace applications are examples.
● Thermally Conductive PCB -Thermal management can be designed directly into PCBs. Design teams can desire systems which eliminate costly, secondary thermal management components, seeking to drastically reduce system size.
Comments