Comprehensive Guide to Effective Containment Solutions
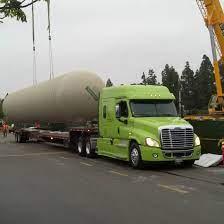
Effective containment solutions play a vital role across various industries, ensuring that hazardous materials and sensitive substances are safely managed. Whether in pharmaceutical manufacturing, chemical processing, or food production, implementing robust containment strategies is essential for protecting workers, and the environment, and ensuring product integrity.
Types of Containment Solutions
There are several types of containment systems designed to meet industry-specific requirements. Each containment solution has its own set of advantages and use cases, depending on the level of protection required. Here, we’ll explore the most common types of containment systems:
1. Primary Containment
Primary containment focuses on providing the first line of defense in controlling the spread of hazardous substances. This typically involves the use of containers, sealed enclosures, and specialized equipment designed to contain dangerous materials at the source.
- Applications: Laboratories, medical facilities, and industries handling hazardous chemicals.
- Examples: Glove boxes, isolators, and safety hoods.
2. Secondary Containment
Secondary containment offers an additional layer of protection beyond the primary containment system. Its primary purpose is to contain any leaks or spills from the primary system, ensuring that no harmful materials are released into the surrounding environment.
- Applications: Chemical storage facilities, fuel tanks, and large-scale manufacturing.
- Examples: Double-walled tanks, spill containment pallets, and berm systems.
3. Tertiary Containment
Tertiary containment solutions are typically used in large-scale operations where hazardous materials could pose a significant environmental threat. These systems provide a third barrier of protection, such as earthworks or reinforced structures, designed to contain any potential catastrophic failures of the primary and secondary systems.
- Applications: Oil refineries, nuclear power plants, and large chemical production plants.
- Examples: Dikes, containment ponds, and concrete bunds.
The Importance of Compliance in Containment Solutions
Compliance with industry standards and government regulations is crucial for the effective implementation of containment systems. Various regulatory bodies, including the EPA (Environmental Protection Agency), OSHA (Occupational Safety and Health Administration), and the FDA (Food and Drug Administration), provide guidelines for containment that ensure safety and environmental sustainability.
Key Regulatory Standards
- EPA’s Spill Prevention, Control, and Countermeasure (SPCC) Rule: This regulation mandates that facilities handling large quantities of oil must have containment strategies to prevent spills.
- OSHA’s Hazardous Waste Operations and Emergency Response (HAZWOPER): Focuses on the safety of employees involved in the cleanup and handling of hazardous materials.
Adhering to these guidelines not only ensures compliance but also promotes safer working environments and mitigates the risk of accidents.
Containment Solutions in the Pharmaceutical Industry
In the pharmaceutical sector, containment systems are essential for maintaining product quality and ensuring the safety of workers handling potent compounds. These solutions are specifically designed to prevent cross-contamination and ensure compliance with stringent regulatory standards.
Containment in Manufacturing Facilities
Pharmaceutical manufacturing involves several critical steps, such as milling, blending, and tableting, which may produce hazardous dust and fumes. Implementing both primary and secondary containment systems ensures that these hazardous substances are properly controlled.
Best Practices in Pharmaceutical Containment
- High-Efficiency Particulate Air (HEPA) Filters: HEPA filters are widely used to capture airborne particles in cleanrooms, ensuring that no contaminants enter the production environment.
- Barrier Isolation Technology: This includes glove boxes and isolators, designed to protect both the operator and the product from contamination.
Designing Effective Containment Systems
The design and implementation of containment systems should be tailored to meet the specific needs of each facility. This includes evaluating the materials being handled, the potential risks, and the operational processes involved. Effective containment solutions are a combination of engineering controls, administrative controls, and personal protective equipment (PPE).
Key Considerations for Containment System Design
Material Compatibility: It’s crucial to ensure that containment materials are compatible with the substances they are intended to contain. This prevents the risk of degradation or chemical reactions.
Leak Detection Systems: Continuous monitoring systems should be installed to detect any potential leaks and allow for immediate intervention.
Ease of Maintenance: Containment systems should be designed for easy access and maintenance to minimize downtime and ensure consistent protection.
Mermaid Diagram of Containment System Workflow
mermaidgraph TD; A[Substance Handling] --> B[Primary Containment] B --> C[Secondary Containment] C --> D[Tertiary Containment] D --> E[Leak Detection Systems]
Containment Solutions and Environmental Impact
The implementation of containment solutions significantly reduces the environmental impact of industrial activities. By preventing spills, leaks, and emissions, containment systems protect ecosystems and reduce the risk of contamination of water sources, soil, and air.
Sustainable Containment Practices
- Recycling Containment Materials: Many industries are adopting sustainable practices by using recyclable or reusable containment materials, reducing waste, and minimizing their environmental footprint.
- Green Engineering: The integration of energy-efficient and eco-friendly materials in the design of containment solutions is becoming a standard practice to enhance sustainability.
Conclusion
Containment solutions are critical in protecting workers, products, and the environment from the harmful effects of hazardous substances. Whether in pharmaceuticals, chemicals, or other industries, the design and implementation of robust containment systems are essential for maintaining safety and compliance. By adhering to best practices and continuously improving containment technologies, companies can reduce risks and ensure sustainable, long-term operations.
Comments