5 Requirements for Refractory Materials of Aluminum Melting Furnaces
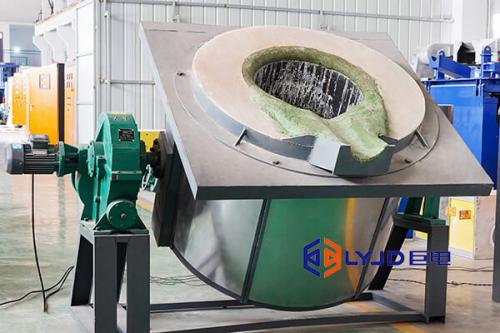
Aluminum melting furnaces require very high temperatures when melting scrap aluminum. Therefore, the refractories used in aluminum melting furnaces are also highly required. Then, what features do the refractories have? Today, let’s talk about it.
Good Chemical Stability
Metal aluminum and aluminum alloys not only have high chemical activity but also have strong fluidity of the melt. The viscosity of molten aluminum at 750°C is quite close to that of water at 20°C, which is the main reason why it easily penetrates the furnace lining and undergoes chemical reactions. At the temperature where the molten aluminum is in contact with the refractory material, it has strong reducibility. SiO2, TiO2, FeO, and other oxides in refractory materials should be reduced by aluminum. The reaction between the molten aluminum and the lining refractory not only affects the quality of the product but also causes nodules, bulges, and sedimentation on the surface of the lining. What's more, there is a danger of cracks at the interface of the refractory material impregnated with aluminum liquid, and it will cause spalling when the furnace is shut down. Therefore, the furnace lining material in contact with molten aluminum has high chemical stability and as little impregnation as possible.
Good Erosion Resistance
Generally, to make the furnace have higher electrical efficiency, the furnace wall material is designed to be very thin. However, during the operation of the furnace, due to the action of the electromagnetic force, the molten metal in the furnace is constantly churning and stirring, which continuously scours and wears the furnace lining. For the heart induction furnace, due to the use of the jet-type melting channel, the erosion and wear of the refractory material of the melting channel are more serious. Therefore, the refractory materials used are required to have high mechanical strength and hardness.
High Density and Volume Stability
As a refractory material for melting furnaces, it is hoped to obtain higher density and volume stability under the condition of certain materials. The level of volume and density reflects the number of pores inside the molded body, especially the degree of sintering. The higher the volume stability of the material, the smaller the possibility of cracks during sintering and use, the smaller the width of the cracks, and the stronger the penetration resistance.
Less Likely to Produce Furnace Tumor
Furnace nodules are formed on the inner wall of the aluminum melting furnace due to impurities (such as Al2O3) existing on the surface or inside of the melt. Furnace warts can significantly reduce furnace capacity. Moreover, the metal tumor itself is dense and tough, making it difficult to remove.
Not Easily Wetted and Penetrated by Molten Metal
As we all know, refractory materials are brittle materials, and cracks will inevitably occur during heating and cooling. But one of the key factors determining its life is the size of the crack and the speed at which it propagates. The crack growth is related to the wetting and penetration ability of the molten metal to the contacting material. The worse the wetting ability, the more favorable it is.
The above are several requirements for the refractory materials used in the aluminum melting furnace introduced by Luoyang Judian. I hope that everyone can choose the right product when purchasing an aluminum melting furnace. If you have any questions about refractory materials for aluminum melting furnaces, Luoyang Judian welcomes your consultation at any time.
Comments